9 Ways to Improve Laboratory Efficiency with the Lean Lab Checklist
Assess the efficiency of your lab and identify areas for improvement
15 Mar 2018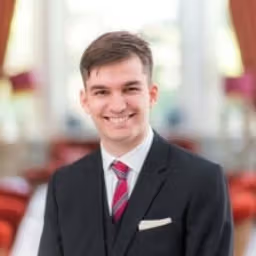
Lean Laboratory is a fast-growing trend, developed from the well-established principles of lean manufacturing which originated in the Japanese automotive industry. Applying a lean approach in a laboratory environment has been shown to increase efficiency and productivity, in industries such as pharmaceutical, chemical, and cosmetics, as well as the food and beverage industry.
The Lean Lab Checklist, developed in collaboration with external experts, is an ideal place to start with the implementation of Lean Laboratory principles. This 9-point checklist helps lab managers of any sized lab, by providing a simple way to evaluate how lean a lab currently is, and identify which actions could have the greatest potential to improve efficiency in that situation.
The checklist is organized into nine areas of improvement, with 35 questions in total. To use this checklist, the respondent simply needs to tick "Yes" or "No" in answer each question. The total number of "Yes" responses is an indicator of how lean the laboratory is, and whether there is still room for improvement. Helpful tips and recommendations are also provided in each section.
Many lean manufacturing principles can be applied directly to the laboratory situation. Tools such as value stream mapping can help reduce lead times, costs, and levels of work-in-progress (WIP). They also improve levels of right first time (RFT) and overall quality that impacts both internal processing and the end-user experience.
To get started on improving efficiency in the laboratory and eliminating unnecessary workflow steps in order to realize significant productivity improvements, download the Mettler-Toledo 9-point Lean Lab Checklist now.