Big Pharma: Tackling the industry’s greatest contamination risk
Senior scientist reveals how her team of analytical experts are combating contamination to protect consumer health, and ensure businesses thrive
27 Jun 2022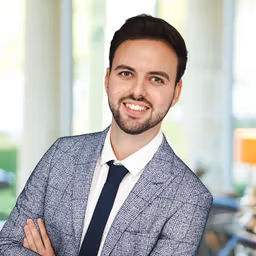
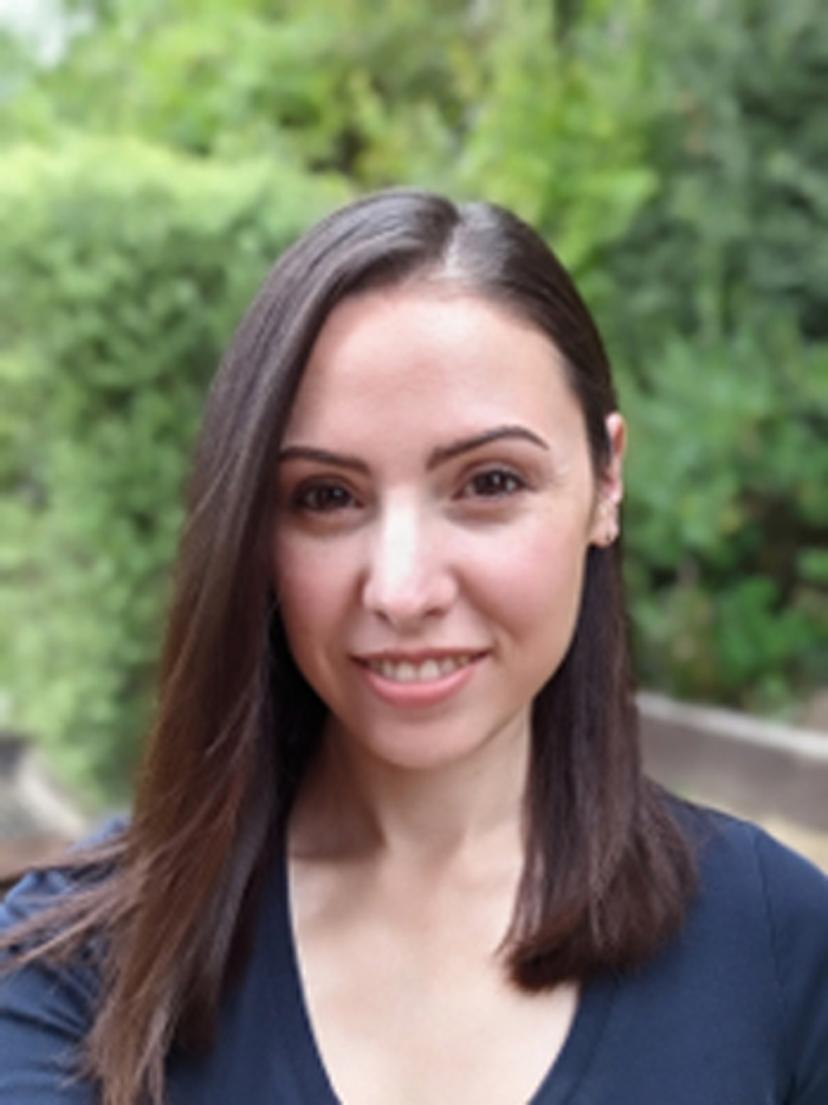
The pharmaceutical industry is responsible for the research, development, production, and overall distribution of medical products, while also being one of the most heavily regulated industries in the world. Pharmaceutical contamination poses a significant threat to public and environmental health. Pharmaceutical businesses struck down by contamination will suffer substantial financial losses, and this could also potentially damage the relationship between manufacturer and customer. There are many potential sources of contamination that can arise during the pharmaceutical manufacturing process, including improper ventilation, poorly trained personnel, incorrect handling of raw materials, and the lack of statutory-compliant hygiene and cleanliness standards.
In this SelectScience® interview, we speak with Fatma Salahioglu, Senior Scientist at Drug Development Solutions (DDS), to find out more about the identification of foreign particulate matter (FPM), and how she works closely with her expert colleagues to effectively examine, analyze and identify unknown particles found during the manufacture of pharmaceutical and biopharmaceutical products. Salahioglu outlines the technology she uses to identify small contaminants and explains how she supports customers to ensure they succeed, while protecting consumer and environmental health.
Cut down on contamination
Fatma Salahioglu, understands the importance of producing safe medicines, “it is paramount to deliver safe and effective medicines to patients. The presence of contamination can compromise not only patient safety, but also the company’s reputation, sometimes leading to financial loss, recalls, or even regulatory action.” Even though pharmaceuticals are acknowledged as a heavily regulated industry, contamination still does occur, even under the strictest regulations. “We strive to help companies overcome this challenge and continue to deliver safe and effective medicines that comply with current regulations,” explains Salahioglu. Since harmful contamination can occur at any point throughout the manufacturing and packaging process, no single step can be taken to completely eliminate the risk of contamination. Being able to effectively understand how and why contamination occurred is critical for a business, “knowing the identity of an unknown is the first step in determining where it has come from. Without any information about the nature or composition of contamination, one would be in the dark trying to figure out what might have gone wrong during manufacture,” says Salahioglu. Accurately identifying contamination, or at least having an idea of its composition can shed light onto this process.
Once the identity has been determined, the scientist can then begin to eliminate potential sources of contamination to narrow the search down to a single source. “Knowing the source of contamination then allows the company to remedy the issue and prevent future reoccurrence,” states Salahioglu. The services offered by DDS directly reduces undesirable pharmacological and/or toxicological effects that occur from contamination, leading to safe, efficient, and high-quality products.
The technology helping to better extract foreign particles
The most common contaminants found in pharmaceutical products range from cellulose and synthetic fibers, to silicone, plastics, metal and glass particles, and skin flakes. The highly experienced staff at DDS are skilled in contamination investigations and can accurately identify trace levels of impurities using bespoke analytical methods. “Due to the vastly varying nature of matrices that contaminants are found in, we have developed and refined different methods of extracting particles. Our methods vary depending on particle size, nature, and the media it is found in. Wherever possible, we will always employ the method that is the most straightforward and will not cause any change in the nature of the contaminant during sampling, such as direct isolation of the contaminant from the matrix using tweezers, fine-tip needle, or any other suitable tools,” explains Salahioglu.
It is important to note that when extracting particles each contaminant is different, so there is no one-size-fits-all method. The team at DDS ensure they always adapt their approach according to the given sample, such as recognizing that particles within liquid media cannot be directly removed, but can be filtered or centrifuged, and embedded particles can be extracted directly or by dissolving the surrounding media. “Our experience allows us to manually isolate particles down to ~40 µm in size, and we employ other methods for particles smaller than this. We always strive to be innovative and creative in our approach, and depending on the challenge at hand, we will explore and try out new techniques,” says Salahioglu.
DDS work directly with a range of customers to help them combat contamination, comply with regulations, and improve consumer safety. “The main challenge our customers face is knowing where the contamination came from. In the past, regulatory guidelines only focused on the quantity of foreign matter, that is, depending on the product and its dosage form, and understanding how many particles were present in certain size ranges, the identity and source of the particles were not as heavily scrutinized. Over the last several years, we have observed regulators being stricter with their expectations from companies with respect to how they deal with the contamination they come across,” explains Salahioglu. The current regulators now expect pharmaceutical companies to determine what the contamination is, and to also perform root cause analysis to figure out where the contamination came from. These investigations will demonstrate the business has better control over their own processes.
The FPM team are a highly experienced group of specialists that are trained to deal with all forms of contamination. “We aim to deliver high quality results in a short amount of time, as we know time can be of the essence, especially when batch production comes to a halt, while awaiting answers on that contamination. We combine the data we generate on our instruments with literature research and any relevant background information, as well as our experience, to come to the most scientifically accurate, clear, and concise conclusions,” explains Salahioglu.
Tech giants join forces to combat contamination
The team at DDS decided to collaborate with Specac to help further advance their analytical capabilities. “We regularly purchase accessories and consumables from Specac, particularly for Fourier-transform infrared spectroscopy (FTIR) spectroscopy. We use the DC-3 Diamond Compression Cell for sample preparation of small particles. These could be any particle, fibre or material that is too small to be analysed using the Attenuated Total Reflectance (ATR) accessory of the FTIR spectrometer,” explains Salahioglu. The Diamond Compression Cell has been specifically designed for FTIR microscopes, which operate to compress samples to an ideal thickness for transmission experiments and deliver excellent signal throughput. “The compression cell is simple and straightforward to use, and it compresses the sample into a very thin layer to allow the infrared light to pass through the sample. Without this, the sample would be too thick, and we would not get any useful signals through.” This specialized technology has allowed the team of analytical experts to analyse problematic samples that do not generate a suitable spectrum using the ATR accessory, such as black rubber. “Compressing a piece of the rubber very thinly gives us a chance at obtaining at least some spectral features that can help us identify the type of rubber,” states Salahioglu.
Looking ahead, the DDS team hope to continue to deliver excellent services in the field of contamination, to enable companies to identify sources of their contamination accurately and rapidly. “We understand the implications of the presence of foreign matter in products and aim to be a trusted partner to our customers rather than just a Contract Research Organisation who churns out results, that may or may not be helpful to the customer”. Salahioglu believes that her work will continue to help the industry deliver safe and effective products worldwide.