Could Correlative Microscopy Solve the Energy Problems of the Future?
Find out how materialography methods are being developed at the IMFAA, Germany, to enhance research into materials for energy conversion, additive processing and energy storage
2 Oct 2017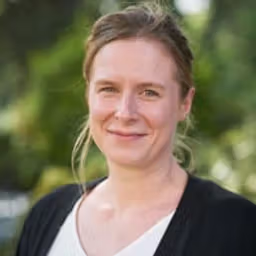
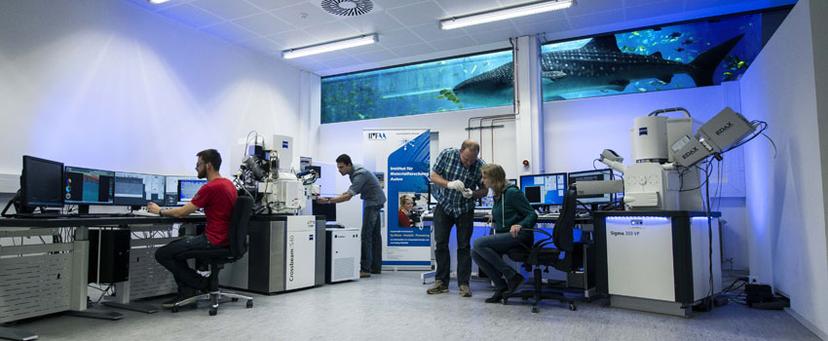
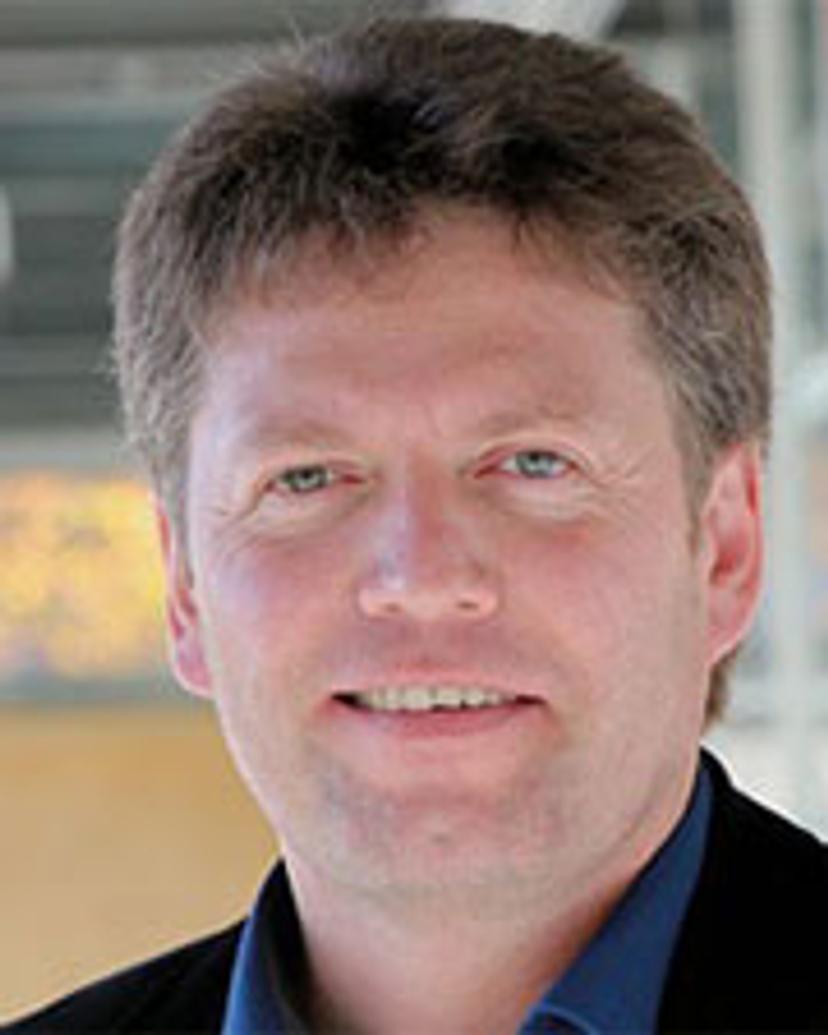
Dr. Timo Bernthaler, IMFAA, Aalen University
The Materials Research Institute (IMFAA), at Aalen University of Applied Sciences, focuses on the application and further development of materialography methods. SelectScience® speaks to Dr. Timo Bernthaler, materials scientist at IMFAA, to find out how microscopy is helping to advance this important research.
SS: Please briefly introduce yourself and your place of work.
TB: My name is Timo Bernthaler, I’m a materials scientist with a background in materials engineering and surface engineering. I specialize in understanding materials and their characterization, with a focus on using microscopy to predict the properties of certain compounds and to understand how this relates to their processing.
I now work at the Aalen University in Germany and I am a member of the management board of the IMFAA, which has approximately 45 employees. The background of our team is widely ranging and includes materials scientists, mechanical engineers, chemists, physicians and informatics specialists, working on approximately 30 research projects.
Energy and 3D printing
SS: What projects involving correlative microscopy are you currently working on?
TB: Our materials research projects are investigating a variety of different fields of interest. We have a focus on materials science linked to e-mobility or sustained mobility, such as lithium ion batteries for energy storage, and magnetic materials for E-Motors. We are also involved in renewable energy materials, such as stationary storage systems for wind or sun energy, and also wind energy generators. In addition to this, we carry out research on lightweight materials for car manufacturing and the airplane/airbus industries.
Finally, we are also involved in the field of additive manufacturing and 3D printing, in particular in metal printing and composite materials. The big advantage of additive manufacturing is the high flexibility in creating new geometries, for example to integrate functionality in a component such as cooling channels, which is impossible to do using conventional techniques.
SS: Which microscopes do you use in your research, and why?
TB: Microscopy is the core technology for all of these fields as it is the microscope that enables us to analyze the relationships between the materials. We have a great relationship with ZEISS, and lots of ZEISS microscopes in our department. We have a number of light microscopes, as well as a ZEISS Axio Imager Vario, ZEISS Axio Imager for polarized microscopy and ZEISS Smartzoom 5 microscopes. All of which are automated and computer controlled. ZEISS provides us with the basic software and we then develop it further. The interfaces are open source so we are able to adapt them to suit our specific needs.
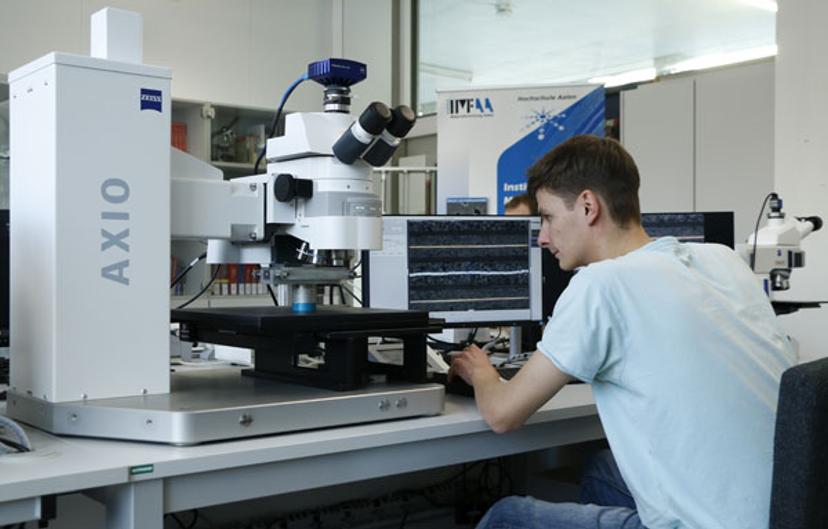
We also have scanning electron microscopes, the ZEISS Crossbeam 550, a focused ion beam scanning electron microscope (FIB-SEM) and the ZEISS Sigma 300, a field emission scanning microscope (FE-SEM). If we need higher resolution to obtain more details from the materials, that’s when we use the electron cross beam. We use the focus ion beam technology to cut into the materials and obtain higher resolved information from the microstructure. All of our microscopes are adapted with chemical analysis or crystallography.

SS: Can you tell us more about your collaboration with ZEISS?
TB: ZEISS is a very popular company that produces excellent machines, the optical resolution of the microscopes is fantastic. Their use of the field emission gun in the electron microscope is quite unique, and they utilize excellent electron beam technology. The microscopes are very simple to handle, but with brilliant results in terms of resolution and usability. ZEISS is also one of only a few companies that combines X-ray, light and electron microscopes into one workflow. We call this correlative microscopy – and it enables us to link all of our image information and data together.
An evolving field
SS: How has materials science research evolved over the years?
TB: We started researching battery materials 10 years ago, when there was very little conversation around the topic, but we were convinced that there would be a need for them in the future. We now work in a very niche, but very important area which is the use of microscopy to investigate non-typical materials such as batteries. These samples require a lot of careful preparation, and we have specific expertise in the grinding and contrasting of samples for artifact-free preparations to develop the microstructure.
SS: What is the future for your research?
TB: We believe that energy is a future problem for the humanity. Do we have the resources and the materials to build our own energy products? What about mobility, for example how will a car be powered? Will it be diesel, petrol or electricity? We are convinced that we have to spend a lot more money on materials, on lithium batteries, energy storage, magnetic materials, energy for motors and conversion of energy. There is also a lot of work that still needs to be carried out on additive manufacturing and we expect to continue to be involved in this field moving forwards.
We are also working in the field of artificial intelligence (AI), on software tools and machine learning. We want to apply concepts and approaches such as face detection and camera entry systems to microscopy. This would enable microscopes to use AI for materials investigation, where software tools will analyze structures automatically. With this more intelligent software, we could, for example, train algorithms to find defects in the batteries, such as foreign inclusions.
To learn more about ZEISS microscopes, visit the product directory