Enhance antibody and lateral flow assay development through partnership with experts
Learn how choosing a reputable, qualified, and expert partner can overcome challenges and increase chances of success
20 Nov 2023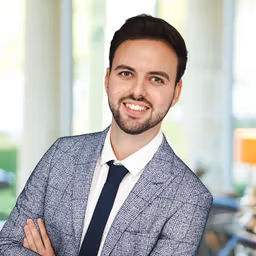

Partnering with a contract development and manufacturing organization (CDMO) and leveraging their expertise makes it easier to navigate the challenges of antibody and lateral flow assay development to improve assay performance, reduce cost and risk, and shorten commercialization timelines.
Antibody and lateral flow assay (LFA) development is fraught with challenges that can impact assay performance, cause delays in getting products to market, and incur high costs. Common challenges include developing antibodies and assays that have a sufficiently high level of specificity, sensitivity, stability, and reproducibility; whilst also ensuring they adhere to stringent regulatory and quality control standards and have the potential to be manufactured at scale, to tight deadlines and budgets.
BBI Solutions provides a unique combination of custom antibody development, LFA development, and manufacturing services to ensure customers are supported from concept to commercialization. In this article, Moya Mellors, Lateral Flow Services Project Manager, and Nathalie Forster, Antibody Development Project Manager, at BBI Solutions, explain how partnering with them can improve the antibody development process and add value to the overall design and development of an LFA. They also provide a brief overview of how BBI works with customers to enhance this process and impart valuable advice for developers.
Benefits of custom antibody development
Commercially available antibodies are readily accessible, allowing researchers to acquire them quickly without the need for extensive development or production. This is sometimes seen as the most convenient option, saving time, money, and resources. However, developers are more likely to run into issues when using commercially bought antibodies. A lack of transparency around clone origins when using commercially brought antibodies can lead to researchers testing the same antibody from different resources, believing that they are unique. Additionally, a lack of visibility on important facts such as how the clones were selected in development can derail researchers' work.
Custom antibody development through a CDMO partnership offers several advantages over purchasing commercially. For example, BBI’s antibody development service involves tailoring antibodies to specific analyte presentations to ensure correct specificity, which minimizes false positives and negatives in lateral flow tests. Forster says, “Close collaboration with customers continues to yield positive feedback and demonstrate success in recent projects. This has resulted in significant improvements in antibody sensitivity and the ability to target specific analytes, surpassing commercially available alternatives.”
Mellors adds, “Collaborating with the antibody development team here at BBI ensures compatibility with subsequent development steps, optimizing stability and performance. This is crucial since the choice of antibodies at the outset heavily influences lateral flow test performance, contributing to approximately 80% of its overall success. Having control and a customized design from the beginning sets a strong foundation for the entire development process. This level of control and customization is not possible with commercially bought antibodies which increases chances of failure.”
Collaborating with the antibody development team here at BBI ensures compatibility with subsequent development steps, optimizing stability and performance.
Moya Mellors
BBI Solutions
Consistency in antibody performance is vital for the success of lateral flow assays, as it ensures that each manufactured batch meets the same high standards, providing reliable and accurate results to end-users. In-house control processes at BBI ensure antibody reproducibility between lots and consistency, ensuring the best possible results, and minimizing the risk of field issues. Developing custom antibodies also enables control over antibody supply, allowing for easier planning, scalability, and marketing without licensing restrictions or royalty payments.
Working together is key to success
BBI Solutions adopts a collaborative approach to antibody and lateral flow assay development, and manufacturing. This increases the chances of successful outcomes and ensures that all end-to-end services run smoothly and efficiently. Customers are treated as equal partners and are involved at various stages throughout their project. Through this regular communication with customers, BBI is better able to track project progress, assess risks from both project and end-user perspectives, and make informed design decisions for cost-effectiveness and product reliability during manufacturing.
Forster says, “Antibody development success relies on key inputs from customers, and we take the time to fully understand their needs and project goals before we get started. These inputs drive the creation of a robust project plan that identifies potential risks and contingency plans to avoid surprises. For antibody development specifically, obtaining high-quality reagents and antigens is crucial for success.”
“The output of our antibody development service is data from various screening stages, which is shared with the customer along with recommendations. This information then guides the production of the required antibody,” she adds.
Antibody development success relies on key inputs from customers, and we take the time to fully understand their needs and project goals before we get started.
Nathalie Forster
BBI Solutions
Mellors explains that lateral flow development has a similar initial process that also begins with detailed input from the customer. This involves scoping meetings to understand the assay's purpose, target users, project scale, commercial aspects, and regulatory requirements.
“Following these initial meetings, BBI work with their customers to identify the target analyte and the clinical matrix. The antigen characteristics, such as structure, sequence, size, and presentation are also determined. This is crucial because these inputs guide the antibody and lateral flow design and determine its format and functionality for end-users, ultimately improving assay performance. Our customers have recognized the value of this collaborative approach and are experiencing its benefits firsthand,” says Mellors.
Quality is a top priority
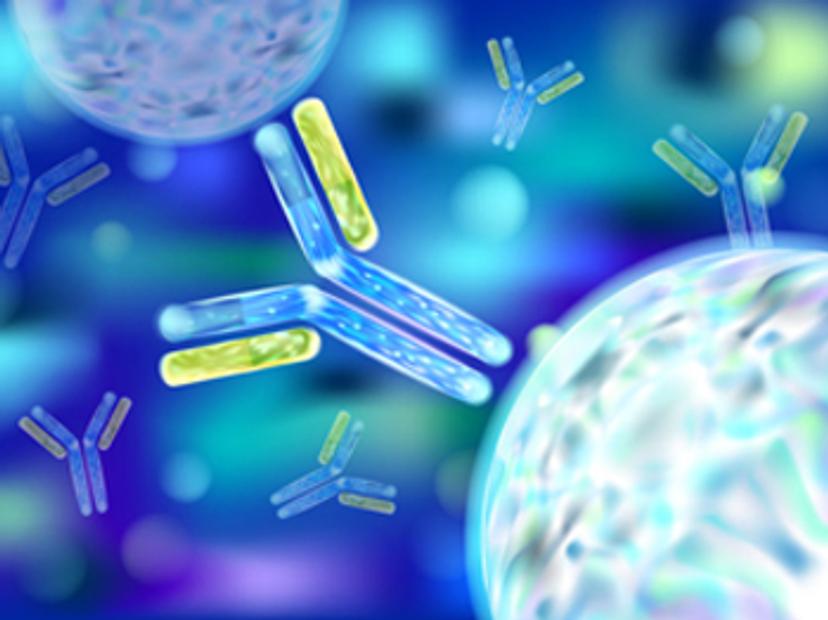
Effective collaboration across teams, stringent processes, and a focus on quality control are essential for a streamlined and high-quality antibody development process. Forster states, “We have a very strong quality control program. Every stage of the antibody development process is controlled by standard operating procedures (SOPs) and reviewed by our quality control team to maintain the highest quality standards. We also have an operations team that supports the entire process, from pilot production to analytics, and focuses on ensuring consistent, high-quality products. This team is trained to identify and address any issues that may arise during production.”
Lateral flow projects also involve a well-structured collaborative approach between various teams, including a dedicated project management and technical team that handles customer projects and a design team that encompasses quality assurance, regulatory, quality control, operations, and validation. Monthly meetings are held between these teams to track project progress, assess risks, and share lessons learned. Formal stage-gate design reviews in compliance with ISO 13485:2016 are also conducted to ensure that project requirements and deliverables are met before moving on to the next stage.
"To support development and manufacturing, a transfer representative collaborates from the early stages to coordinate with manufacturing, ensuring future manufacturing considerations are addressed,” explains Mellors. She continues, “Technical operations teams also come into play during validation and production batches to address any operational issues quickly, drawing on their knowledge of the unique aspects of the project. This structured approach helps ensure smooth project progression and timely product delivery for customers.”
Advice from the experts
Forster and Mellors advise customers to take advantage of the services offered by BBI Solutions to improve antibody and LFA development processes and get products to market quicker. Mellors says, “If you use commercially supplied antibodies, you are more likely to run into issues such as availability, high costs, limited quantities, and challenges related to traceability and clone control. But by opting for custom antibody development services like those offered by BBI Solutions it is possible to avoid these problems.”
Mellors goes on to emphasize that developers must first thoroughly understand their target analyte, its characteristics, and how it appears in their test system before starting development. She elucidates, “This includes recognizing whether the target is intact or fragmented compared to its native state and determining the detection range that is needed. The more customers know about their needs, the better the development plan can be tailored to meet them.”