Festo introduces an open-source gantry robot for automated liquid handling at SLAS 2022
This solution allows OEMs to develop instruments targeted specifically to their application in minimum time
7 Feb 2022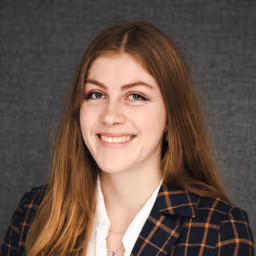
Festo introduces at SLAS 2022 the Modular Gantry Robot platform for laboratory-based automated liquid handling. Open sourced, customizable, and utilizing world-class components, this new solution enables equipment designers to quickly realize their unique solutions with fewer mechanical and electrical engineering resources, speeding time to market.
Festo also introduces a complete family of building blocks for developing pressure/time-based automated dispensing and pipetting applications. This platform is compatible with a broad range of media, offers exceptional repeatability at high speed, and can be easily calibrated for targeted applications. A core component of the family, the PGVA pressure/vacuum generator, supplies microfiltered air and vacuum for lab fluidic applications, including dispensing and pipetting. A single automated pipetting system equipped with a PGVA can transfer a range of liquid volumes from milliliters on up with ± 2% precision. Dispense/pipette heads are available in variants from 1 up to 96 channels for high throughput applications.
These new solutions were developed at the Festo Life Science Technology Engineering Center (TEC), Billerica, Mass. Established in 2018 as part of the Festo research and development arm, the TEC pioneers the development of new high speed, high accuracy fluid handling and dispensing solutions and collaborates with original equipment manufacturers (OEMs) to bring their laboratory equipment to market faster and with less risk based on Festo world-class automation components and global technical support.
COVID has accelerated both product development and individualized work at the TEC. To speed development, personnel used a strategy of modular building blocks that can be applied quickly and mixed and matched as needed. COVID accelerated development led to the new Modular Gantry, open-loop pipettes, and PGVA air box.
Modular Gantry
Modular gantries feature an open-source motion and fluidic application programming interface (API) with Python, Java, and .NET/C# drivers. Utilizing a library of common drivers reduces the learning curve and enables integrators to easily develop an optimized control strategy for their machine – strategies that support the end-use customer’s success and satisfaction with the machine. The flexibility and ability to customize eliminates the need for OEMs to purchase a generic machine and then adapt their test or assay solution onto it.
Modular three-axes gantry robots can be delivered as ready-to-assemble kits, including cabinet and all necessary supporting components, or as preassembled systems. The Modular Gantry Robot platform follows a Lego-like building block strategy of hundreds of interoperable components designed to be assembled with simple hand tools. Festo Life Science engineers guide customers in the selection of the optimum modules for the target application, including the level of three-axis robot required to handle speed and load. Other modules can include dispense head, pipettes, capper/decapper, and bar code reader. Simple modular Gantries can ship in 8 to 12 weeks, and production scaled up rapidly where needed to suit urgent applications such as Covid testing.
Open-loop pipettes
Utilizing compressed air and vacuum, Festo open-loop pipettes transfer liquid volumes in microliter ranges with up to ± 2% precision. The system can provide fast clog detection and liquid level sensing. Sterile pipettes are available with 20, 300, and 1,000 ul tips, with filters and without. They are compatible with Festo dispense heads, gantries, and PGVA, creating the benefits of modular automation. By the end of 2022, Festo will be offering the “smart” closed loop pipette. Programmed easily using a built-in web interface, the smart pipette will be used in applications benefiting from high accuracy and multiple sensor feedback that enables volume verification.
PGVA pressure/vacuum generator
In the PGVA unit, pressure and vacuum are generated by a quiet 50 dB pump and stored internally in individual reservoirs. Air is filtered to -0.001µm purity. Flow is servo controlled by a fast, silent, energy efficient piezoelectric regulator. For easy operation, PGVA can be controlled from any RS232, USB, or Ethernet port. Open-source Python, C#, and Java drivers are posted and supported on Github: GitHub - Festo-se/PGVA-1: Pressure and Vacuum Generator This all-in-one 24V system has a footprint of 8"x3"x8". The PGVA received in 2021 an IDEA! gold award and LEAP engineering design silver award.