High-Pressure Dosing Pumps from KNAUER Play Important Role in Manufacturing Methanesulfonic Acid
KNAUER’s high-pressure dosing pumps, based on HPLC technology with pump head heating, produce methanesulfonic acid
10 Oct 2018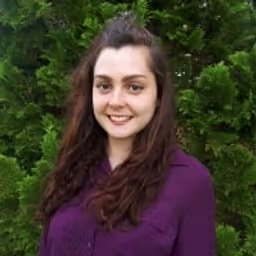
The Berlin-based manufacturer of laboratory measuring instruments KNAUER Wissenschaftliche Geräte GmbH, has reported that its high-pressure metering pumps played an important role in the development of the groundbreaking new manufacturing process of methanesulfonic acid (MSA) directly from methane and sulfur trioxide, which was successfully realized by researchers from Duisburg's Grillo-Werke AG.
Currently, methanesulfonic acid is already produced on an industrial scale. Its strongly acidic but non-oxidizing properties make it an interesting catalyst for many reactions in organic chemistry, especially in polymerizations. Methanesulfonic acid is also used in electroplating and increasingly also in industrial cleaners, where it is used as a substitute for phosphoric, hydrochloric or sulfuric acid because it is less harmful to the environment at comparable or greater efficacy than the mineral acids used previously. The preparation of methanesulfonic acid is currently relatively expensive, because of multi-stage processes, which are partly dependent on toxic intermediates such as dimethyl disulfide.
The direct reaction of methane with sulfur trioxide would be the most obvious solution. Researchers worldwide have long been experimenting with the direct activation of methane. As early as in the 1950s, a US patent was filed using sulfur trioxide, however, the achieved yields of methanesulfonic acid were low and the number of unwanted by-products high. [2]
The Grillo researchers took a different approach than most other researchers. They relied on relatively mild temperatures below 100 degrees Celsius and pressures around 50 bar only. The cunning in their process is an activator molecule that triggers sulfonation and can easily be re-synthesized from MSA and sulfuric acid in a secondary process. By the way, sulfuric acid serves as a solvent in the process.
A tricky part of the new MSA synthesis is the precise metering of sulfur trioxide (SO3) into the chemical reactor. Sulfur trioxide is only liquid in a narrow temperature range between 32°C and 44°C, reacts violently when in contact with water and chars most plastics very quickly. This means that it is very difficult to handle.
"In search of suitable pumps for this task, we had already received a few cancellations from suppliers before turning to KNAUER. KNAUER also could not offer us a model off the shelf, but they were the only manufacturer to embark on a little development trip," said Dr. Timo Ott, Head of Product and Process Development for the chemistry branch at Grillo.
KNAUER high-pressure dosing pumps are based on HPLC technology and inherently provide high chemical resistance, excellent flow rate precision, and low pulsation. However, pumping liquid sulfur trioxide required customization, especially with regard to plastic parts in the flow path. Another important prerequisite for the success was the powerful pump head heating offered by KNAUER in order to keep sulfur trioxide fluid even at low flow rates or necessary stops.
"It is part of our company philosophy that we find beneficial solutions for our customers and together with them. We are particularly pleased that we were able to make our contribution to the success of Grillo’s MSA synthesis, which is, in my opinion, a research project of global importance,” states Dr. Christian Benkhäuser, Head of Hardware Development at KNAUER.
The special feature of the methanesulfonic acid production process developed by the Grillo researchers is that it works much more efficiently than previous processes and makes methane usable as a carbon source for sulfonation. Certainly, with this process methane is becoming more important as a raw material. Wasting methane through flaring will hopefully become less common. Using biogas as a source of methane, the process can do without a fossil carbon source. A recently published comparative life cycle assessment (LCA) study from the University of Zurich concludes that the new process has a three times smaller environmental impact than previous methods. Greenhouse gas emissions are 85% lower. [3]
"When the new manufacturing process for methanesulfonic acid will be introduced on an industrial scale, the environment will benefit of it," Dr. Ingo Biertümpel is convinced. He is Head of R & D in the Chemistry Branch of Grillo-Werke AG and the company’s Sustainability Officer. Something else is already clear today: It is worthwhile, as Grillo has done here, to leave the beaten path, it is also worthwhile, like KNAUER, not to say hastily "we can’t deliver that" and it is fun working together to develop new solutions.