How a proactive and collaborative stakeholder-focused approach to risk mitigation tackles supply, quality, and regulatory challenges
A leading risk mitigation expert shares insights on the benefits of engaging in open conversations on risk
27 Jun 2022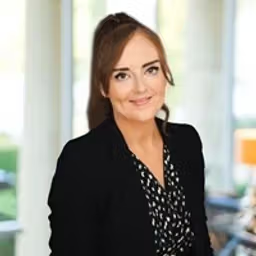
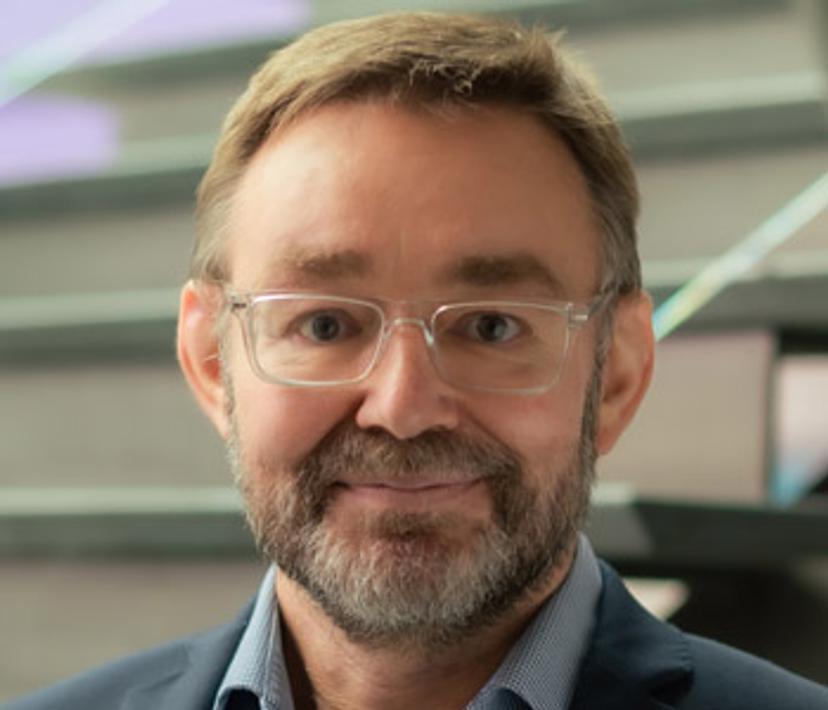
The pandemic-fueled focus on risk mitigation has highlighted supply chain challenges, and potential improvement areas that need to be addressed across industry. In this SelectScience interview, we speak with Caspar Robinson, Risk Mitigation Program Lead at Merck. He shares his insights on how open communication and strategic partnerships can facilitate supply chain security and other risk factors like quality and regulatory challenges, which in turn can protect consumers and enable good business practices.
Over the past two years, supply chain channels across industries have been significantly disrupted by the COVID-19 pandemic. Elaborating on the key challenges in the post-pandemic environment, Robinson explains that interruptions to the supply chain have caused an unprecedented and unforecasted rise in the demand for specific raw materials. This situation has only been further exacerbated by the disruption of global and local transportation networks. To add to this, limited headcounts and COVID-19 imposed quarantine requirements have stalled manufacturing and testing operations.
Refocusing the limelight on risk mitigation
Such challenges have warranted an inspection of factors, such as supply chain reliability, quality of materials, regulatory support, and procurement best-practices. Risk mitigation activities have been pushed into the limelight, with industries questioning the assumptions and thinking that has traditionally gone into contingency planning.
As a result, the pandemic has led to a refocus on maintaining business continuity, says Robinson. “Risk mitigation is the removal, reduction, or effective accommodation of any element that could disrupt a business’s operations or services.” The negative aspects of unaddressed risk can be quite severe, he continues: “On one extreme, it can result in consumer or patient harm, as in the case of the healthcare sector. But it can also contribute to reputational damage, negative regulatory findings, operational disruptions, increasing costs, and even loss of business.” This makes it crucial that companies conduct risk assessments and plan for risk mitigation, while also actively choosing to work with suppliers who can help reduce risk.
Engaging in proactive and open conversations
Given the diverse regulatory standards across industries, the lens with which risk mitigation is viewed might differ, explains Robinson. “Heavily regulated sectors, such as healthcare, already come with an embedded expectation of having an active supplier management program in place that would cover risk mitigation. This might not be the case for less regulated or unregulated sectors,” he explains. Nonetheless, the focus across industries is to ensure business operations remain robust and reliable. Towards these common goals, risk mitigation should be a standard part of good business practice for any industry.
“Within the three key categories – supply chain, quality and regulatory – many tangible actions can be undertaken to reduce and manage risk. However, a common theme underlying all risk mitigation actions is proactive and regular communication between the client and supplier”, explains Robinson.
“There may always be certain aspects of a business that may be out of one’s control, such as global shortages of certain raw materials at any given point in time”, Robinson clarifies. Therefore, the key is to identify alternative solutions to addressable issues in the supply chain, with a focus on improving quality and supply chain reliability, while maintaining business consistency. Having an open and structured conversation on risk allows the adoption of new, impactful solutions.
Facilitating risk mitigation through strategic partnerships
“To overcome the challenges that our commercial partners typically face, we work to gain a thorough understanding of their current and future needs,” shares Robinson. As a raw material manufacturer and service provider with a global presence, Merck engages in active communication to build a collaborative partnership.
As a testament to their willingness to invest in risk mitigation, the Merck team enters into strategic partnerships, with the support of the respective senior management teams on both sides. “We have found that support from cross-functional stakeholders allows both organizations to work together to address risks from the initial product development through to final manufacturing,” continues Robinson. “This manner of working empowers both teams to think about risk and how best to address it in a holistic manner across the full commercialization journey.”
These discussions, with a diverse range of stakeholders, will give rise to productive conversations, allowing a range of perspectives and different needs to be brought to the forefront, mentions Robinson. Highlighting functional needs, identifying current pain points, and gaining clarity on where future business objectives lie are all key to kickstarting the conversation on risk mitigation efforts. “As a manufacturer and service provider, we always welcome an in-person discussion because that allows us to get down into the details, which ultimately proves valuable in tailoring a solution to our customers’ needs. In advance of these discussions, we have built a lot of useful online educational resources to enable customers to understand potential solutions,” says Robinson.
Merck’s goal as a manufacturing and service provider is to reduce unnecessary challenges – including that of unaddressed risk – that its customers face. “Our aim is to enable our clients to focus on the core aspects of their business, without having to worry about hurdles. We are here to help clear their path to success,” concludes Robinson.