How Merck aids lateral flow test development
From the manufacture and supply of raw materials to risk mitigation and assay development capabilities, learn how Merck is helping IVD developers bring new devices to market
13 Jul 2024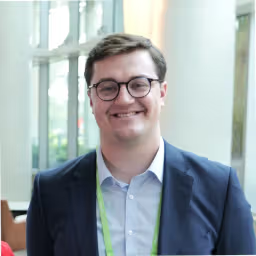
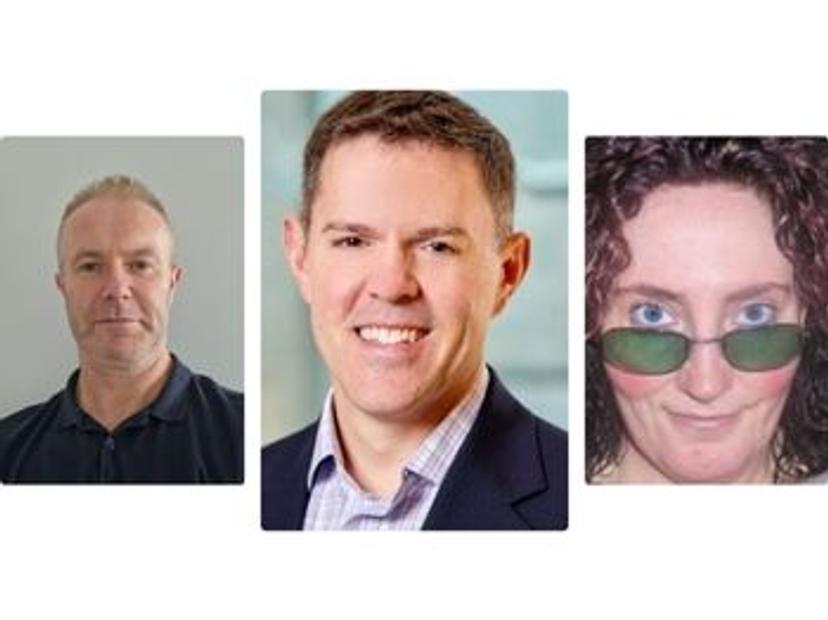
(left) Peter Curley, Principal Scientist, (middle) Shawn Gaskell, Head of Diagnostic Manufacturing Materials, (right) Lisa Fitzpatrick, Diagnostics Field Marketing Manager, at Merck
Taking a lateral flow test from the design stage through product development to final manufacturing is never easy. The test strip design, the materials used, their integration with reagents, and manufacturing processes can all affect the consistency of performance. Moreover, as manufacturers adjust to new regulations for invitro diagnostics (IVDs) and medical devices, meeting raw material quality and traceability requirements, as well as ensuring supply chain security, has never been more important.
Partnering with a reputable raw material supplier and leveraging their expertise can make it easier to navigate these challenges. Shawn Gaskell, Head of Diagnostic Manufacturing Materials, Peter Curley, Principal Scientist, and Lisa Fitzpatrick, Diagnostics Field Marketing Manager, at Merck, are working to help their customers streamline assay development, comply with the new IVDR, and reduce the time and costs associated with bringing novel lateral flow tests to market.
From raw material supplier to development partner
Securing supplies of high-quality raw materials and chemicals is a crucial step in any assay development process. “An assay, at the end of the day, is only as good as the raw materials that go into it,” explains Curley. However, it’s not just the quality and consistency of raw materials that matter.
“Even when products meet manufacturing criteria and specifications, a customer's unique assay or combination of raw materials can necessitate adjustments,” explains Gaskell. “It's not solely about meeting specifications consistently; it's also about enabling customers to integrate these products holistically, adapting to their specific needs.”
This is where IVD developers can benefit from working with a supplier with application and/or development expertise, and why Merck has recently complemented its raw material offering by introducing Assay Development Services. “We offer a fee-for-service to customers to design and develop lateral flow assays,” explains Curley, who works in the Assay Development Services Department at Merck’s membrane manufacturing site in Cork, Ireland – one of four facilities the company has across the globe, including an assay development laboratory in the U.S and two customer application support laboratories in China. “Our customers range from those who have an idea for a lateral flow test but limited knowledge on how to start their development, to companies that might be halfway there and just want our input,” he adds.
We understand the materials that go into a lateral flow test because we make them.
Peter Curley Principal Scientist, Merck
A perfect synergy of expertise
Marrying developers’ specialist knowledge with Merck’s extensive manufacturing expertise is central to these efforts. “In my experience, medical device designers are always the experts in the design of the device and their end application, but we bring to the table expertise of the raw material itself; how to handle it, how it behaves in a specific application, and things to avoid when you're manipulating or handling the product,” explains Gaskell. “We can bridge that gap and incorporate our technical knowledge into the design of the finished device.”
Sometimes all it takes is one conversation. “Often just jumping on a call for half an hour with a designer can solve a problem they’ve been struggling with for weeks,” he enthuses. “You can cut a development lead time from six months down to three or four months simply because of the insight and guidance a technical expert at the manufacturing site can supply.”
Curley echoes this sentiment. “We understand the materials that go into a lateral flow test because we make them,” he quips. “Not every lateral flow assay service provider can do that. Some just provide materials, design support, or do custom development, but Merck encapsulates all those things in one program.”
How to manage risk and ensure IVDR compliance
Risk mitigation has always been a core focus for IVD manufacturers, but the introduction of the new In Vitro Diagnostics Regulation (IVDR) has brought this into a new light. The IVDR imposes a broader scope of responsibility throughout the product lifecycle, with heightened requirements for testing incoming materials, ensuring supply chain transparency, and conducting post-market surveillance.
“Your responsibility doesn't end when you've put your test in a box and chucked it on a truck out the door. Now you're responsible for when it's out in the world,” explains Fitzpatrick. “That has been a huge change, and that kind of risk mitigation and management isn't just in the manufacturing, it's right at the beginning when you're looking to source your raw materials.”
The shift necessitates meticulous documentation and detailed oversight of critical raw materials to demonstrate compliance, which in turn underscores the importance of partnering with suppliers with high levels of traceability and transparency.
“It's so important for an IVD or medical device manufacturer to have that traceability because if something does happen, you can trace it all the way to the original raw material source,” explains Gaskell. “The transparency piece is the communication – the follow-up with the customer – which includes things like change notifications. If you're a benchtop researcher you may not need to know if there was a packaging change on a reagent you're working with, but an IVD or medical device manufacturer needs to know because they may need to assess that risk.”
Clear and concise material specs for hassle-free audits
One way Merck is helping customers comply with IVDR is through aiding their choice of raw materials. “We've got a really great program called M-Clarity™, which groups products by quality and the associated documentation,” explains Fitzpatrick.
The M-Clarity™ Program is designed to improve product and service transparency throughout Merck’s broad life science portfolio. In this program, chemicals and consumables are classified into six quality segments (MQ100-MQ600). Equipment is classified into four quality segments (EQ1-4) and spare parts into two quality segments (SP1-2). Each segment provides specific documentation and services. The segments have increasing attributes to meet the application and regulatory requirements.
This transparency empowers manufacturers to choose products aligning with their specific needs and compliance requirements, ultimately facilitating easier regulatory adherence. “Let's face it, nobody likes audits, people hate them, but the smoother you can make that audit by having everything in place, the happier everybody is,” Fitzpatrick enthuses.
In addition to M-Clarity™, which encompasses all of Merck’s life science products, the company has also curated a portfolio of products that are fit-for-use for IVD development and manufacturing, in a program called Elevate®.
“With Elevate, rather than saying to customers that we have all these different product numbers available, we use our experience to recommend a selection of the best ones to look at first,” explains Fitzpatrick. “These come with change notifications, can be part of a quality agreement, site quality self-assessment, etc. – they’re ready to go.”
“The Elevate dossiers bring together all the key information you need without having to search for it, saving customers a lot of time and pre-work,” adds Gaskell. “They can just check the risk boxes and say, ‘Yeah, we've assessed this. It's all right here."
“The regulatory environment continues to evolve weekly and is regionally dependent. We’re just trying to stay ahead of the curve, or at least alongside it, to help manufacturers, all our customers, navigate those complexities,” he concludes.
Top tips for those seeking an IVD partner for lateral flow
- Less is more – From a procurement perspective, maintaining around 10 to 20 supplier relationships is recommended for managing risks and building strong vendor rapport.
- Development support - A partner who can offer expert R&D knowledge will help to avoid common development pitfalls and accelerate commercialization while reducing time and supplies during optimization.
- Think global – During times of supply constraints, partners with global manufacturing and distribution footprints are better positioned to maintain sufficient safety stock by mobilizing secondary and tertiary sourcing.
- Ask questions – What are the critical raw materials for your application? Does your raw supplier materials have change notifications? Can you get materials on a quality agreement? Do you have a good relationship with your supplier? Do they have the knowledge and expertise?