How to design a cleanroom for life science and pharmaceutical applications
We explore the importance of cleanrooms in life science labs, and discuss challenges and considerations for cleanroom design
9 Jan 2024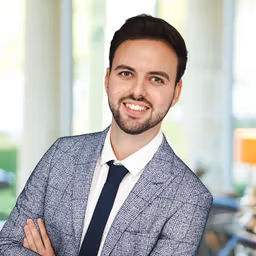
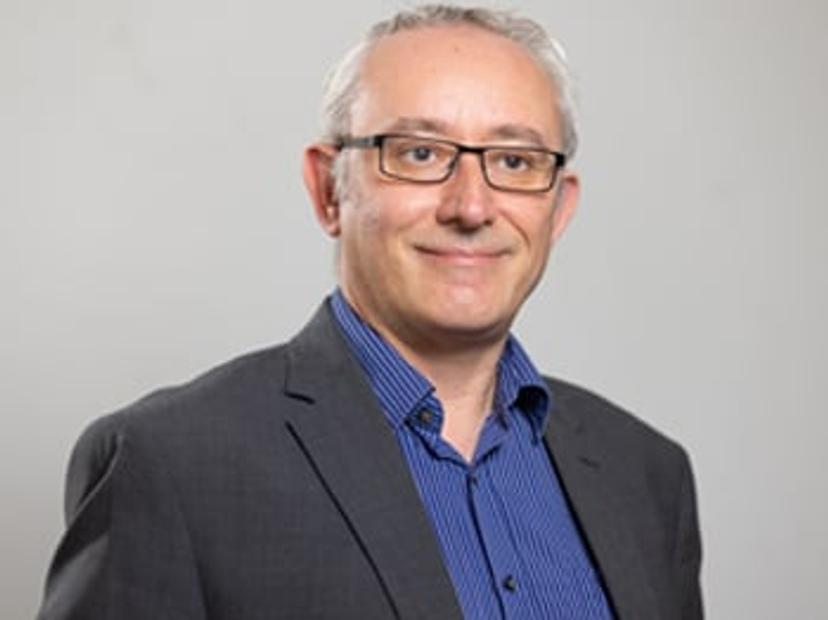
A cleanroom is an artificially engineered environmental system designed to maintain a very low concentration of airborne particulates and has applications in scientific research and industrial manufacturing. Maintenance of a contained environment such as this requires several parameters to be highly controlled, monitored, and measured. In this article on how to design a cleanroom, we’ll speak to a leading microbiology expert and learn about key considerations and challenges in cleanroom design.
Scientists looking to design a cleanroom may have a number of questions. What value do cleanrooms bring to a life science research project? What equipment is needed to create an efficient cleanroom, and how is this equipment vetted to be considered cleanroom classified? To answer these questions and find out more about the role of cleanrooms in life science research, we spoke with Dr. Tim Sandle, a leading microbiologist at Bio Products Laboratory (BPL), Hertfordshire, England. BPL is a manufacturer of plasma-based products, which are designed to help people with immune disorders and conditions, such as hemophilia.
Sandle has a strong background in pharmaceutical microbiology, and expertise in contamination control and quality risk management. As well as working at BPL, Sandle teaches pharmaceutical microbiology at the University of Manchester. He is also a visiting tutor for University College London (UCL) where he helps to train new QP candidates (qualified person in the pharmaceutical industry).
How to design a cleanroom: key considerations
“Cleanrooms are the foundation of preparing medicines in pharmaceuticals and broader life sciences,” explains Sandle. However, there are many underlying aspects to consider when building and selecting suitable products for a proficient cleanroom. “The area must be easy to clean with strict controls around equipment and the permitted level of particles that a piece of operating equipment is able to produce. There must also be very strict controls around people, in terms of the way they behave and the way they gown,” he says.
The important aspects that go into designing a cleanroom can be broken down into four key requirements, Sandle explains. “The first is that the air going into the room is filtered and passes through a filter of appropriate article retention capacity. These are high-efficiency particulate air (HEPA) filters. Within pharmaceuticals and areas where sterile medicines are being produced, these HEPA filters need to be of a high retention capacity. Normally they're 99.97% efficient.”
Contamination control measures mean that we can prepare medicines in a way that minimizes contamination, and that's why cleanrooms are so important to the pharmaceutical sector.
Dr. Tim Sandle
Bio Products Laboratory
“The second important principle and a key design element to reduce contamination is the retention of particles within the cleanroom. So, the cleanroom must have a relatively fast air change rate. This is the time taken for the cleanroom to replace its given volume of air with fresh air. Typically, you'd expect that to happen every two to three minutes to make sure any produced contamination has been removed.”
The third principle is related to air movement and air direction. “Within a conventional cleanroom, we need to make sure that it is designed in such a way that the air is in constant motion, and the degree of turbulent flow keeps any contamination in suspension. This is so it can be pulled from the room as part of this air exchange basis. There's a different type of air requirement for medicines that are dispensed under EU GMP, Grade A. Here, the air needs to be of a very fast velocity, traveling around 9.5 meters per second in one direction,” explains the expert. This is referred to as unidirectional airflow and creates a curtain of cleanliness to help protect product components, particularly open product files.
“The fourth and final key principle is air direction, or pressure differentials. Here, we would design a facility with a pressure cascade, which means that air always moves from a cleaner area into a less clean or lower grade area by maintaining a positive pressure differential,” explains Sandle. The laws of physics dictate that contamination would not be able to move against a stronger outward airflow. As a result, cleanroom users tend to have many rooms of varying degrees of cleanliness, having at least the pressure differential of 15 pascals between each.
“It's those four contamination control measures that mean that we can prepare medicines in a way that minimizes contamination, and that's why cleanrooms are so important to the pharmaceutical sector.”
Addressing common challenges in the cleanroom
When considering how to design a cleanroom, it is vital that users keep these four requirements in mind. Nevertheless, designing and maintaining an efficient cleanroom is a challenging and complex task, and therefore there are some key challenges that must be considered to reduce contamination risk. Sandle describes his experience of challenges faced when working within a cleanroom, and explores two common sources of adversity: cleanroom design and human workforce. “The design element is more about the selection of equipment to go into the cleanroom. The equipment needs to be designed in such a way that it's fully cleanable. It needs to minimize the number of perfusing ledges, and so on. The reason for this is that, in terms of air distribution in a cleanroom, the closer air gets to a surface, the slower that air becomes. It starts to move in different ways and there can be a risk of water seeds forming,” he says.
“Wherever there are interactions between equipment and a cleanroom, there is a risk of particles dropping out and landing where you don't want them to land. There are some additional complications with equipment, which can add to that effect.” Sandle continues, “One is that sometimes, when equipment is operating, it can be a source of particles, particularly where equipment isn't very well maintained. Certain motors, for example, could be pushing out particles. Another issue is with heat, in that if items get very hot, they can also disrupt the airflow.” These challenges add a layer of complexity when considering how to design a cleanroom, with airflow being a key factor.
Sandle discusses the best approach to design and setup to mitigate these challenges. “An important way to overcome these challenges is to undertake mapping. The best approach to mapping is a technique called CFD, which stands for computational fluid dynamics. CFD is focused on air speeds and temperatures and enables users to predict the way the air might move, so that they can take the necessary action. It's important to do a lot of that work up front to try and minimize some of these challenges later on.”
The second challenge Sandle describes is more difficult to plan and mitigate for during the design stage. “The second challenge is always the people working within the cleanroom setting. People are the biggest source of contamination because people shed a high number of skin cells and a number of those skin cells will be carrying microorganisms. Even though people will gown correctly, there will always be limitations on what a cleanroom suite can contain. Plus, people can behave in unpredictable ways, such as inadvertent touching, movements that are too rapid, incorrect PPE, or they may have even been wearing their gowns for too long. These are all factors that can lead to an increase in contamination.”
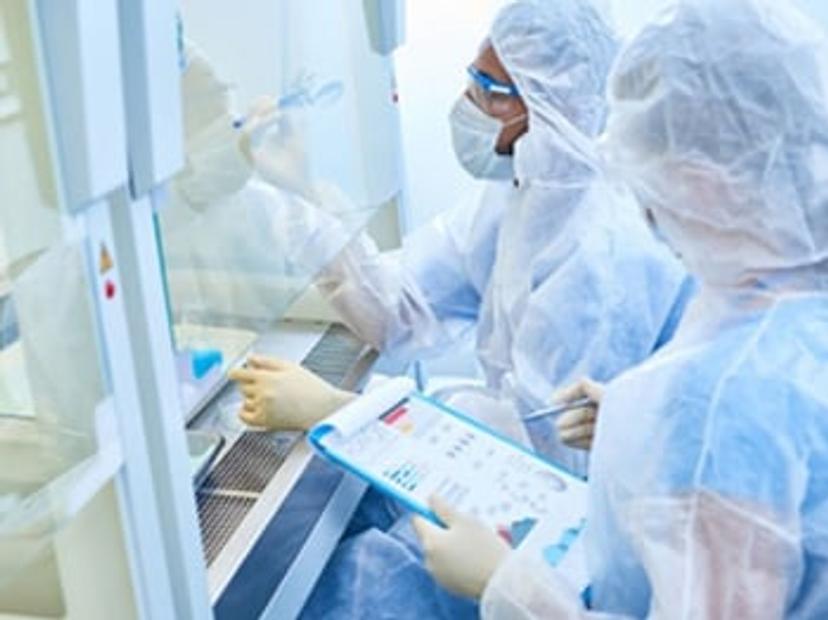
To overcome these complex challenges, users must minimize the number of people entering the cleanroom and ensure that people fully understand their roles and responsibilities. “There should be a lot of emphasis focused on training, both in terms of behavior but also teaching them the knowledge and understanding of how contamination can be deposited into the airstream,” explains Sandle.
Why classification matters: Considerations for selecting cleanroom equipment
To learn more about selecting suitable cleanroom equipment, Sandle describes the importance of choosing cleanroom classified equipment to reduce the chance of the equipment being a source of contamination itself. “For equipment to be considered cleanroom classified, the first consideration is the materials of construction. Most equipment would need to be robust and hard-wearing, but it also needs to be easily cleanable, with ideally smooth and polished surfaces. The equipment also needs to be compatible with the variety of different detergents and disinfectants that are commonly used within cleanrooms.”
Most cleanrooms require the use of sporicidal disinfectants, which contain aggressive chemicals such as chlorine - since they are designed to eliminate all microorganisms. However, as Sandle explains, this can cause problems. “If the equipment fabric and materials are not the correct design, then reactions will occur with these chemicals. The ideal types of materials for equipment are plastic or stainless steel-based. Typically, a high grade of stainless steel would be required, so it's common to use 316L stainless steel for certainly anything that's a product contact part. But even here, care must be taken that the surfaces of the equipment don’t become scratched or roughened and also that they don't react with the disinfectant.”
Sandle continues to describe other considerations for selecting the best instrument for a cleanroom. “Equipment must not be generating particles itself, particularly when it's operating. The equipment needs to be easily to transport, if it needs to be moved or, if it's fixed in place, then in the ideal location. It should also provide a degree of contamination protection as well. So, we don't want to use equipment that might be the source of product cross-contamination or damage itself.”
Where can you find appropriate equipment for use in a cleanroom? Sandle draws from his previous experience to provide us with some insight. He explains that the selection process of off-the-shelf or more bespoke equipment bring distinct challenges, and the experience of the manufacturer also plays an important role in the suitability of equipment. “Some manufacturers are very knowledgeable and are up-to-date with the latest regulations. Others might be less so, or sometimes people design things that might be suitable for one grade of cleanroom, but aren't necessarily suitable in other grades of cleanrooms. The best way to address such a challenge is spending time working on a good user requirement specification (URS) and ensuring that there's sufficient level of detail within that URS.” A URS should contain specifications for anything from electrics and wiring to valve type and considerations of how easy the equipment is to clean.
Sandle also points out that data integrity is, of course, an important consideration for equipment used within pharmaceuticals: “how information is captured and how that information can be secured is quite important for equipment used within the cleanroom, so, the URS is key.”
It's important to spend a lot of time on the planning and not rush too hastily into the execution.
Dr. Tim Sandle
Bio Products Laboratory
Contamination control: Cleaning and disinfectant
Beyond design and planning, cleaning and disinfection protocols are an important process for the maintenance of your cleanroom to reduce contamination. “Contamination can arise from a number of sources. But principally, the types of contamination will be bacterial or fungal, microbial byproducts, general particulates, and chemical residues. The sources of contamination are largely from people. It has been estimated that people are probably responsible for about two-thirds of contamination found within the cleanroom. Other sources include water. If there are spillages or poorly controlled water supplies, then that can be a contamination source. Water presents a double problem because it's quite an effective vector, so it's easy to spread aerosol droplets around, for example. Also, water provides a medium for quite a lot of different bacteria to grow in.”
Sandle highlights that air is another common contamination source and can spread contamination around the cleanroom. The transfer of items into the cleanroom is another aspect to consider, Sandle explains. “Transfer disinfection is a very important control measure. That comes down to ensuring items are multi-wrapped and different layers of wrapping are removed at different stages, together with being supported by cleaning and disinfection.”
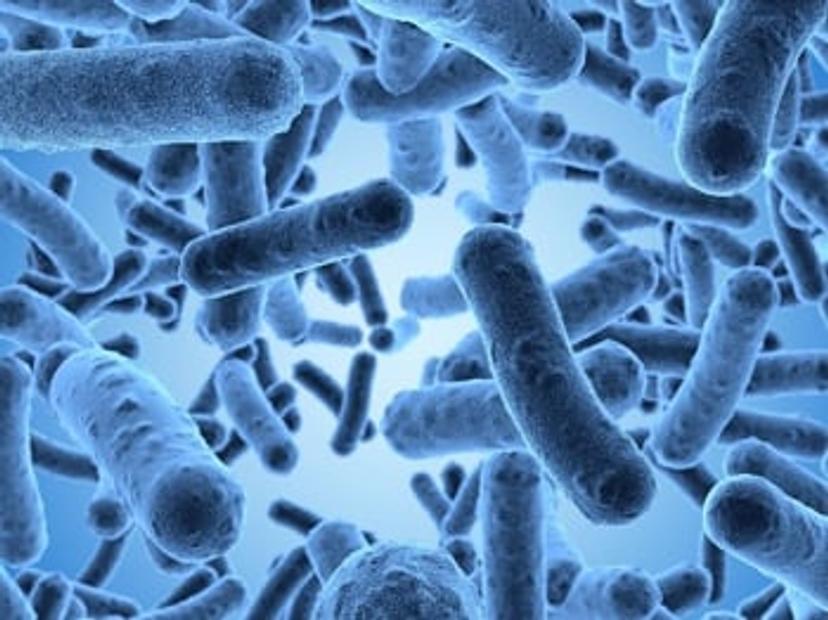
To address all those contamination sources, users need to have a robust cleaning and disinfection program in place. Sandle describes cleaning as the application of detergent with the goal to remove any traces of soiling. “This can be from grease, protein, dirt, and particles. The reason cleaning is so important is because disinfectants are very effective at killing microorganisms, but they do have quite a poor ability to penetrate through the soiling, so we need to clean first.”
After cleaning, Sandle explains, disinfectants should be applied to cleaned surfaces. The selection of disinfectants is an also an important choice. “It's very important to select disinfectants that are able to kill a wide range of microorganisms. That's what's referred to as the spectrum of activity; we want to be able to kill organisms from all these different contamination sources and we want them to do so as rapidly as possible. But it's important that the disinfectant comes into contact with the microorganism for a sufficiently long period of time to allow the disinfectant chemical to interact or penetrate the microbial cell walls. This is referred to as contact time.”
“Achieving contact time requires a good method of application. It's important to train cleanroom personnel to be able to wipe and mop effectively, for example. There's also a requirement to rotate between two different types of disinfectant for pharmaceutical manufacturing. This is to overcome any resistant microorganisms that might be developing. So, by using two different disinfectants of different chemistries and different active ingredients, we can overcome that effect. There's also a requirement to use a sporicide that will tackle the toughest microorganisms in the cleanroom, which are bacterial spores.”
Looking ahead
There are many factors to consider when exploring how to design a cleanroom. Fundamentally, good planning, training, and maintenance are key to building and maintaining an effective cleanroom, which promotes accurate results, free from contamination. Looking forward, Sandle hopes that his work and expertise will help improve and optimize the detection of contamination, to enable those who run cleanrooms to react more quickly. “It's about improving the response time and understanding the types of contamination, their origins, and formulating appropriate corrective measures that cleanroom managers can put into effect, which will help to protect products and ultimately patients,” concludes Sandle.
Technology for your cleanroom
PHC Corporation of North America, manufacturer of PHCbi branded products, provides a portfolio of ISO-classified PHCbi brand ultra-low freezer and cell culture incubators.
From the large capacity CO2 incubator, MCO-80ICL-PA, to the more compact design of the MCO-170AICUVHL-PA and MCO-230AICUVL-PA, PHCbi has a solution to fit your unique cleanroom needs. These incubators were designed to optimize decontamination protocols while minimizing contamination risks, making them an ideal solution for any cleanroom. You can benefit from key features including maximized storage space, touchscreen control panel, and enhanced production yield of cell culture experiments.
The TwinGuard Series Ultra-Low Temperature Upright Freezer is another ISO classified solution designed to fit all your long term storage needs. With intuitive smart controls and monitoring, and two independent refrigeration systems, gain unparalleled protection for vaccines, cell cultures and tissues, rare specimens, biological materials, and other high valued products.
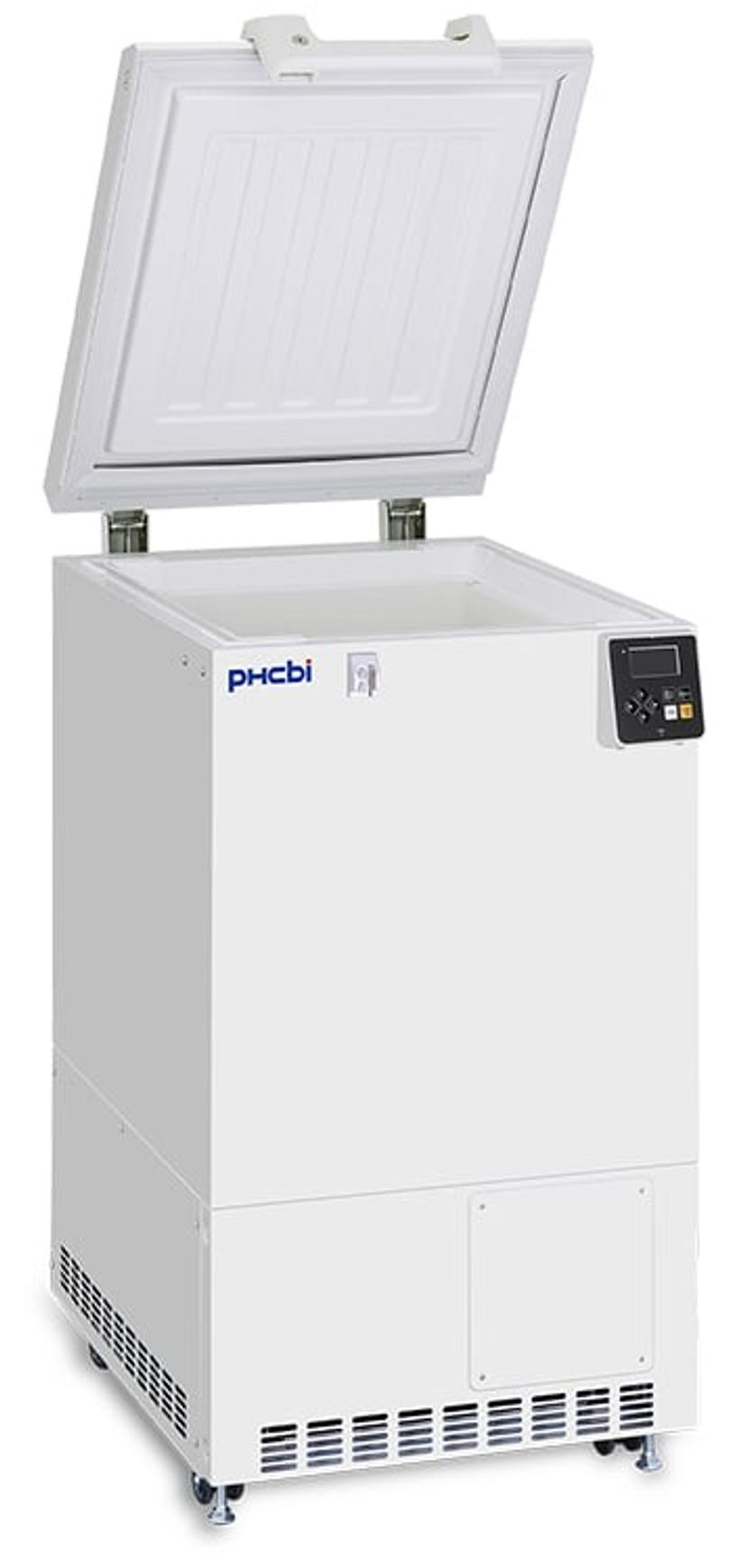