Lab relocation: How to overcome an outgrown lab
Explore the intricacies of Alnylam Pharmaceuticals’ move from 9 crowded labs to a spacious research facility
14 Jun 2021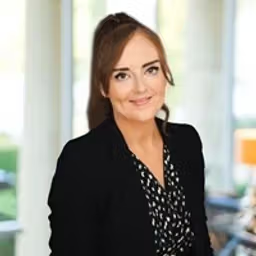
Alnylam Pharmaceuticals is an RNA interface therapeutics company that mainly focuses on advancing a robust pipeline of innovative RNAi-based medicines in four different therapeutic areas: genetic medicines, cardio-metabolic diseases, infectious diseases, and neurological and ocular diseases. These pipelines contain therapies in late-stage and early-stage trials.
Recently, Alnylam Pharmaceuticals experienced an increase in financial and staff growth, with little room to expand its current labs — meaning relocation was the only practical solution. At the heart of the planned move was Daniel O’Connell, Associate Director of Facilities Operations at Alnylam Pharmaceuticals. O’Connell’s relocation needs were common: a hands-off, cost-effective solution to safely transport and reinstall a full lab. At the same time, with so many personnel affected, it was vital to keep downtime to an absolute minimum. With over 1,000 research assets across nine labs needing to be relocated, O’Connell faced a variety of challenges – but he was able to overcome these issues by partnering with an experienced lab relocation company, which provided him with the resources and expertise he required to ensure a successful move.
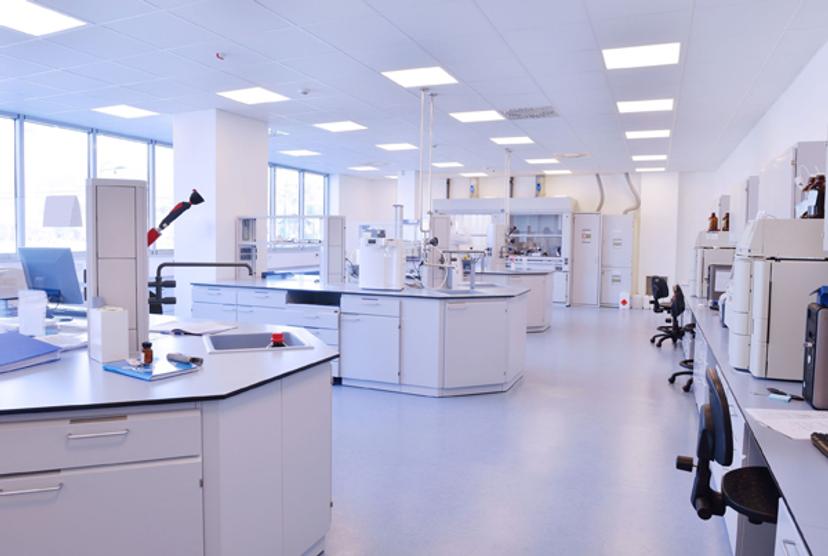
Lab relocation challenges
There are many reasons why labs may need to relocate, including changes in funding, lab expansion, and project and staff growth. Such moves bring their challenges, so extensive planning is essential for an efficient and cost-effective transfer of expensive and delicate equipment. Companies must comply with a range of policies including waste, contamination, and hazardous materials regulations.
Fulfilling regulatory needs is challenging enough when relocating, but Alnylam’s relocation came with its own set of unique hurdles.
Due to its previous location, external forces like a snowstorm called for major flexibility and temporary workflows were needed to prevent delays. Along with external forces, transportation of Alnylam’s hazardous and refrigerated material required special care where an explosion-proof room was essential at their new facility.
Implementing an effective move
Moves of this size do not happen often and, as a result, the necessary experience, knowledge, and skills required are usually unavailable internally. Just getting started by planning and evaluating risks can be more than enough to overwhelm the person tasked with handling the relocation. As a result, those overseeing such a transition often look to outside sources, such as original equipment manufacturers, local transportation services, or even dedicated project management companies.
During the quoting process, we were very impressed with the transparency of the quote from Agilent. It was clear before the project started that they understood what we were looking for and that they could bring a ton of value to the table.”
Daniel O'Connell
Associate Director Facilities Operation at Alynylam Pharmaceuticals
In Alynlam’s case, the team looked to Agilent. Agilent conducted asset inventories, origin and destination site visits, as well as numerous risk assessments at both starting and ending locations. O’Connell recalls: “Everything you could think of, they’d captured. Elevator issues, loading dock availability, you name it. And a number of those would have really become major issues had we not already had contingencies in place.”
Agilent project managers hosted daily briefings with Alnylam, ensuring full transparency around the status of the move, from details surrounding partners to vendors and assets. As relocation project managers have seen, these small details have the power to derail an operation like this. For example, Agilent coordinated the transportation of chemical standards along with instrument deinstallation. This may seem unimportant, but these standards are often needed as part of the deinstallation and reinstallation processes — if packaged and transported before the larger instruments, as is often the case, this can spell trouble for the reinstallation.
Pre-move checks and post-move performance verifications ensured all moved assets worked just as well post-relocation. Movers, contractors, and other suppliers were all managed, ensuring the new site was in good working order before assets arrived. The more routine parts of the move also called for acute attention to detail—after all, a new space is useless if, for example, the asset power supplies do not match the new lab’s outlets. Agilent’s pre-move inspection uncovered this very issue, among others, which helped prevent costly downtime post-move.
Looking to move
Agilent delivered just what Alnylam sought: a fully managed and expert-driven relocation, with a focus on minimizing downtime, from planning to reinstallation. “We really found value at every step of the relocation with Agilent,” says O’Connell. “Every piece of their process was done well, and they were genuinely focused on delivering the best experience and outcome possible.” After all 1,008 assets had been moved, Agilent was still able to save Alnylam 12% on its planned spend for service providers, and 9% of the costs for the project as a whole.
Do you use Agilent products in your lab? Leave a review here for a chance to win a $400 Amazon gift card>>