Scaling up manufacturing of custom oligonucleotides for life science research
SelectScience speaks with Integrated DNA Technologies (IDT) to hear how the company has been able to increase its offering of customizable and robust nucleic acid products to support the life science industry
29 May 2022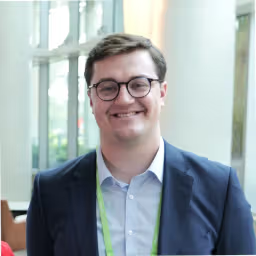
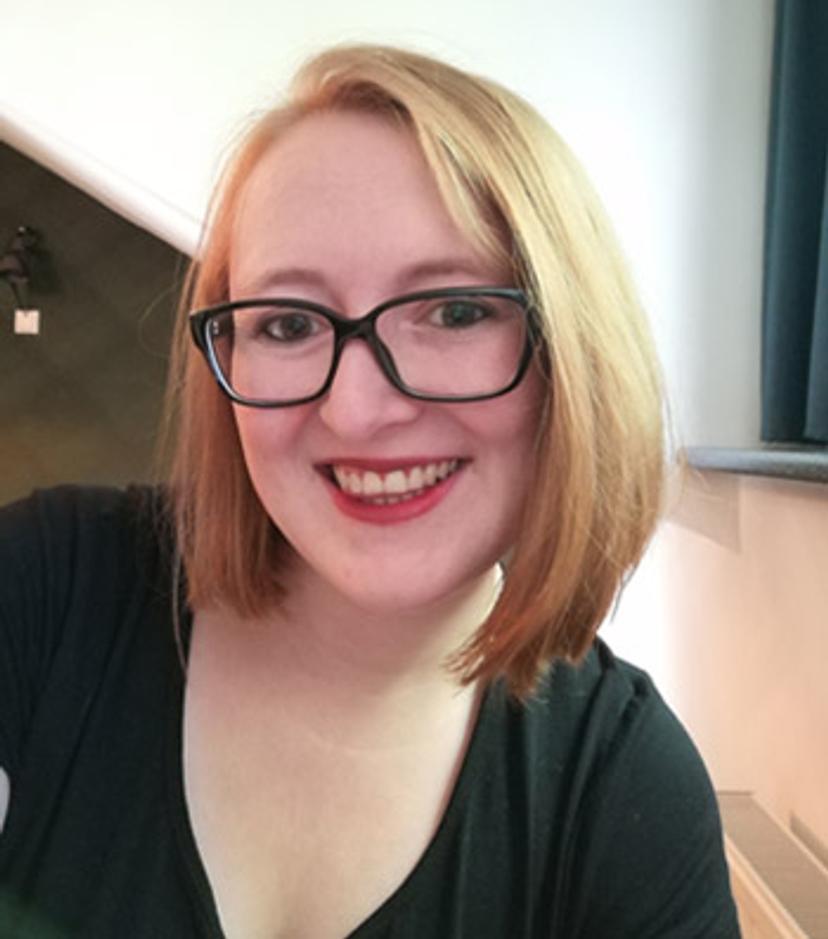
From academia and commercial research to medical diagnostics, pharmaceutical development, and synthetic biology, oligonucleotides form the foundation of almost any molecular technique. However, synthesis of these compound molecules can be incredibly complex, requiring a highly controlled reaction to ensure factors such as pH, temperature, and the quality of substrates are tightly regulated. This complexity increases even further when producing longer, more customized nucleotide sequences.
Naomi Cauwenberghs is an assistant manager of large-scale processing at Integrated DNA Technologies (IDT), a genomics solutions provider and manufacturer of nucleic acid products such as custom oligonucleotides. Cauwenberghs’ day-to-day role involves overseeing the final formulation step of the whole oligonucleotide production process, leading a team to quantify the final product, prepare quality control samples, interpret quality control results, and prepare the sample as per the customer’s request, among other duties.
In this SelectScience article, we speak with Cauwenberghs to hear what sort of decisions she and her team have made to overcome challenges with producing these complex products, how the company has been able to continuously expand its offering, and to gain some of the key considerations that need to be made when shipping these products.
An influx of demand
When it comes to any form of manufacturing in the scientific industry, Cauwenberghs states the biggest challenge lies in keeping up with customer demand. “Customer expectations are evolving, from their needs on the type of product, the needed yields, or amount of oligos. Upscaling IDT’s manual handlings can pose challenges, which is why we try looking into the possibility of automation where we can. But this isn’t always possible due to the very custom nature of our process.”
Cauwenberghs goes on to share how COVID-19 brought with it an urgent need to handle both larger batches and larger quantities of product. “Scaling up to those demands in a short period of time required us to handle product quickly, look for new solutions, and to think outside of the box,” she explains.
“We must question and challenge our processes regularly to ensure we optimize and grow together in ways that meet our customer’s needs.”
Process improvement and optimization
To overcome these challenges of high demand, IDT stresses manufacturers need to dig deep to see how and what they can improve, how they can be more efficient, and whether automation is possible. Cauwenberghs expands on this approach, “Our process is very organic. We keep learning, improving, and adapting to the needs of the current market. We’ve been busy expanding our capacity, both with machines and people. But we’re always looking into other machines and techniques to update and improve our processes for the future. It’s very important for us to think ahead as well, to forecast, and try to take actions to prepare us for what we’ll need in the future.”
Ensuring safe delivery
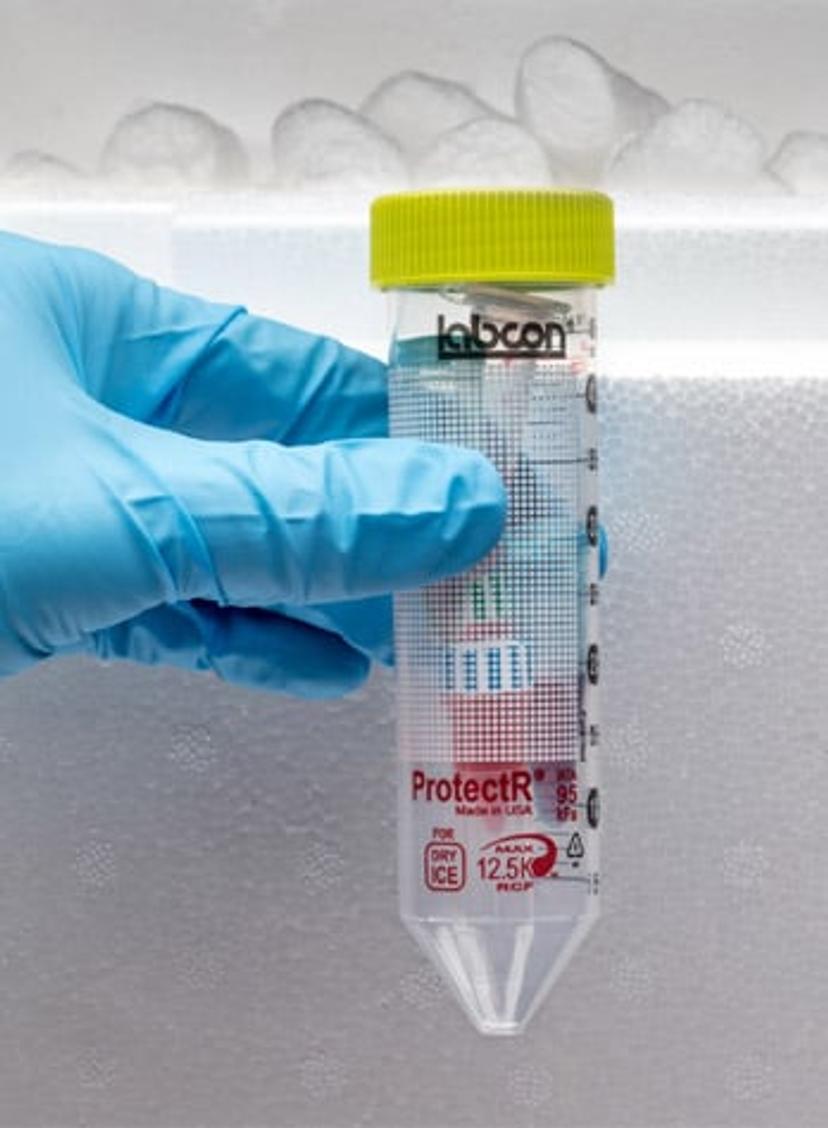
When shipping delicate nucleic acid products for genomic applications such as next-generation sequencing, CRISPR genome editing, qPCR, or RNA interference, Cauwenberghs explains it is crucial not to overlook the importance of having high quality shipping containers and packaging. “Making considered choices in our product packaging helps to make sure that our product stays safe and reaches the customer in the same condition and with the same quality as we shipped it in.” She continues to emphasize how it is the small details such as ease of use, volume markings, a dedicated place for labels, and information about the container specification on the tube that can provide added value to the manufacturer and the customer.
Cauwenberghs explains that when shipping on dry ice, it is important to make sure that the product is kept in its frozen state when dissolved in a buffer. It is imperative that the tubes are well sealed, leak-proof, and can withstand the low temperature of the dry ice without cracking and breaking. “For the majority of our large scale research use only products as well as some of our GMP* mid and large scale products, we ship to customers in the Labcon ProtectR® Tubes,” states Cauwenberghs. “These tubes are specifically designed to withstand dry ice and provide IDT with a great option for a standard shipping container for its product. They guarantee that the high quality of IDT’s product stays intact during transport. The dimensions and shape of the tubes are industry standard, which makes it easy to integrate them in the science and research environments that we’re active in.”
Confidence with supply chains
Being one of the largest manufacturers of custom oligo products in the world, we asked Cauwenberghs what IDT’s key considerations are when choosing a supplier to work with. She answers, “Our top considerations fall into three main areas. Firstly, we look at the quality of their products. The products need to meet the specifications that we need, to guarantee the best quality for our customers in return. Secondly, we are looking for a reliable supply with good on-time delivery. This is necessary to make sure we can keep producing at the same pace without having production stops due to stockouts. Finally, great communication and customer support are key to ensure that good decisions are made when purchasing, and that help is available if questions arise.”
For research use only. Not for use in diagnostic procedures. Unless otherwise agreed to in writing, IDT does not intend these products to be used in clinical applications and does not warrant their fitness or suitability for any clinical diagnostic use. Purchaser is solely responsible for all decisions regarding the use of these products and any associated regulatory or legal obligations.
*GMP refers to products manufactured under ISO 13485: 2016 QMS. Purchaser is solely responsible for all decisions regarding the use of these products and any associated regulatory or legal obligations for their legal marketing.