Shaping the future of polymer R&D: Advances in atomic force microscopy
How to get critical information about the structure and the properties of polymers down to the nanoscale — an expert webinar
25 Nov 2019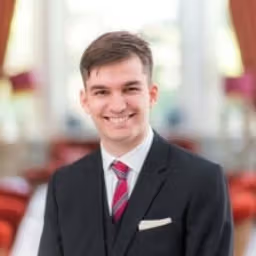
Today’s material characterization tools must provide critical information to ever-finer dimensions, down to micro- or even the nanoscale. Our on-demand expert webinar explores how atomic force microscopes (AFMs) are uniquely positioned to do this job.
In this webinar, application scientists Dr. Ted Limpoco and Dr. Jonathan Moffat look at how AFMs can reveal polymer structures down to the crystal lamellae, examine morphologies such as nanopores and nanofibers created from specific processes, and evaluate the dispersion of fillers and phase separation of components in composites and blends.
They also explore how to use AFM towards innovating high-performance polymer products and how to use the latest material and process innovations to reduce your time to market.
Read on for highlights from the webinar Q&A session or register to watch the webinar at any time that suits you.
Watch Webinar Now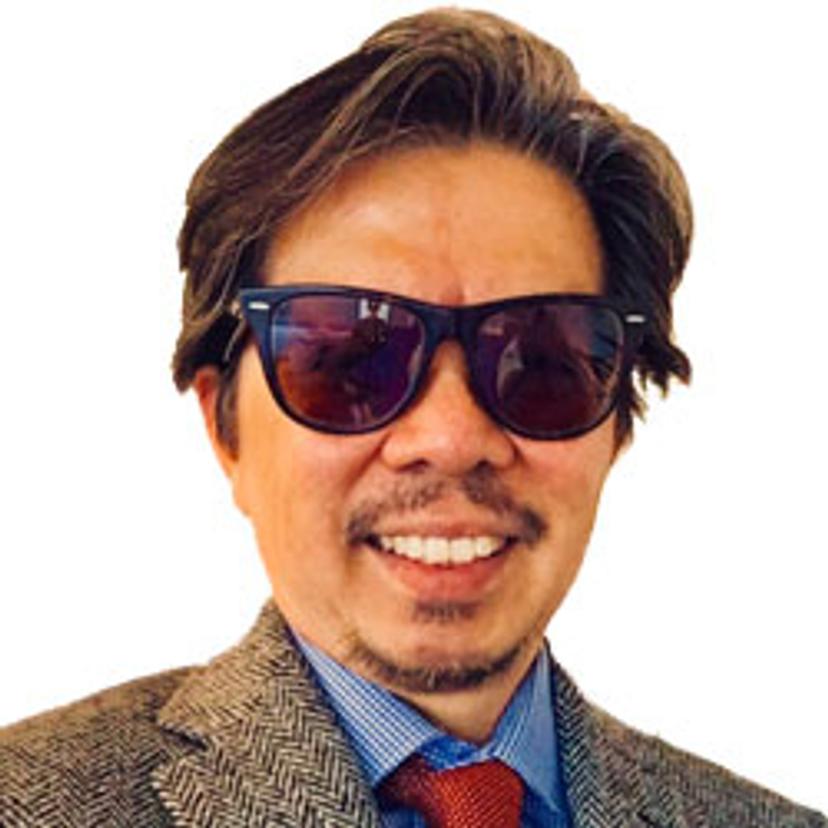
Q: How is phase able to differentiate components of rubber blends and what does the phase contrast mean?
JM: The phase signal is an indication of sample interaction. We obtain this signal by looking at the oscillation of the cantilever with reference to the drive signal. So, for example, when the tip interacts with something soft, sticky or adhesive, it has attractive interactions that will slow down the cantilever. Therefore, the phase will seem to increase. Conventionally, if we go over something stiff then the phase will decrease. If we can monitor this phase signal or plot this phase signal over our topography imaging, then we can get a qualitative indication of the mechanical properties of the sample.
Q: When performing phase imaging of a block co-polymer, what parameters do you suggest changing to, to get the best phase contrast of the two blocks?
JM: To get the best phase contrast in an AFM image, you want to be in what we call repulsive mode. This is whereby the tip and sample have repulsive interactions, so, i.e., where the probe is touching the surface rather than interacting with some long-range forces. To get the tip into repulsive mode, what we do is drive the probe a little bit harder so that it taps the surface. We can do that by either lowering our set point, increasing the force, or we increase our drive signal.
Q: How were you able to quantify the modulus of the polymers in the laminate sample?
TL: For this, we used the AM-FM Viscoelastic Mapping mode which is based on looking at the frequency shift in the second resonance or bending mode of a cantilever. The stiffness contrast is largely based on this frequency shift. If we can get the sensitivity of this frequency shift by measuring a sample of known modulus, we can determine the modulus of other test materials.
Q: Is it possible to quantitatively measure the local Young’s modulus and what method should be used for it?
TL: There are two basic methods you can use for quantifying Young's modulus. You can do force curve type measurements, such as force mapping or fast force mapping, where the slope of the force curve in the contact region is a measure of stiffness. You can also use the AM-FM Viscoelastic Mapping mode, which is a tapping mode technique and get the frequency shift which is related to the local stiffness of the sample.
Q: Would it be possible to image the battery separator membrane material in the battery electrolyte solution rather than in air?
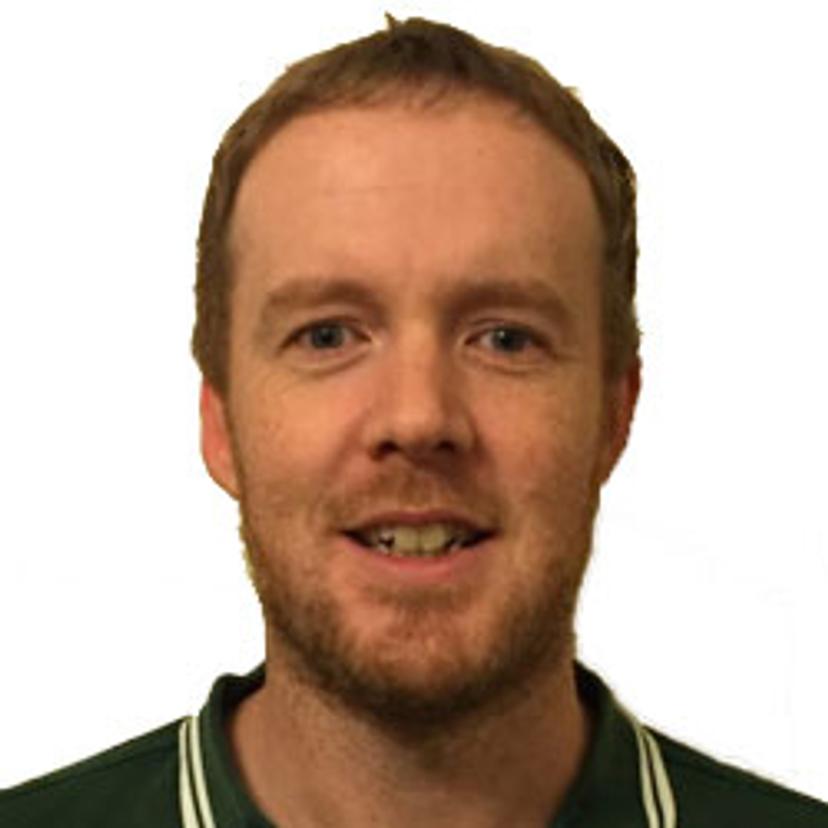
JM: Yes, that's possible. One of the major advantages of AFM over other microscopy techniques is that we can image our samples in a native environment. We can have the sample in a liquid environment, say an electrolyte solution. If you're looking at biological materials, you can look at them in pH buffered solutions. We can also look at samples at raised or different temperatures and in different gas environments.
Q: How do we choose a cantilever for a particular application?
TL: For nanomechanical applications, where you need to measure the stiffness of the sample, you need a cantilever that has a commensurate stiffness with your sample. That means you should be able to deform the sample with a cantilever, so it can't be too soft. The cantilever is also your force sensor, so it also needs to deflect to measure the force that you apply. It also depends on the dynamic range of a particular mode, AM-FM, for example, has a wider dynamic range than force curve. You can, for the same lever, probe a wider variety or stiffness of materials than with a force curve. For electrical modes, you need to have a probe that's coated with a conductive material so you can measure current, or sense electrostatic forces or surface potential.
Q: What is blueDrive and what is it used for?
JM: Asylum’s blueDrive technology is a method of oscillating the cantilever. When we say we're oscillating a cantilever it means we're in a mode known as tapping mode. The traditional method to excite or oscillate the cantilever is typically mechanical. That means we have a small device within our system which shakes the cantilever physically. This can cause a few issues when we come into liquid. We couple these vibrations into the liquid, which causes many complications when imaging. It causes significant instability. One method to get around this is just to oscillate the cantilever alone. So, we do this by shining a blue laser on the back of the cantilever, hence the name, blueDrive. This causes a very small amount of localized heating on the cantilever and causes the probe to bend due to the bimetallic strip effect. If we can then modulate the power of that laser, we can accurately control the oscillation of the cantilever. This gives us very stable oscillations and thus for quantifying nanomechanical properties based on oscillations of the cantilever, gives us very reliable and very accurate measurements on our mechanical properties.
Q: Can you explain how you can get stiffness and dissipation contrast in tapping mode imaging?
TL: In this mode, AM-FM Viscoelastic Mapping, we track two resonances or bending modes of the cantilever. We use the first resonance to obtain topographic information as well as phase contrast like in regular tapping mode. Then we look at the second mode to measure frequency shift related to the stiffness of the material being imaged. We can also look at how amplitude decays, which is related to the energy dissipation.
Q: How do you compensate for thermal drift when doing heating experiments?
JM: When you heat up your sample, there's going to be thermal drift due to expansion of different materials within the system. One way to try to overcome that is to scan faster to minimize the drift rate. But, for some heating experiments, this may not be sufficient. Another method to get around this issue is to use the image stabilization feature in our software. This continually images and tracks the last two scans and looks for certain features on the surface, it then recognizes these as a pattern and monitors these features as they drift due to thermal expansion. It changes the offsets for the next scan and keeps tracking these features as we keep scanning.
Q: What is your recommended approach to prepare samples for AFM imaging?
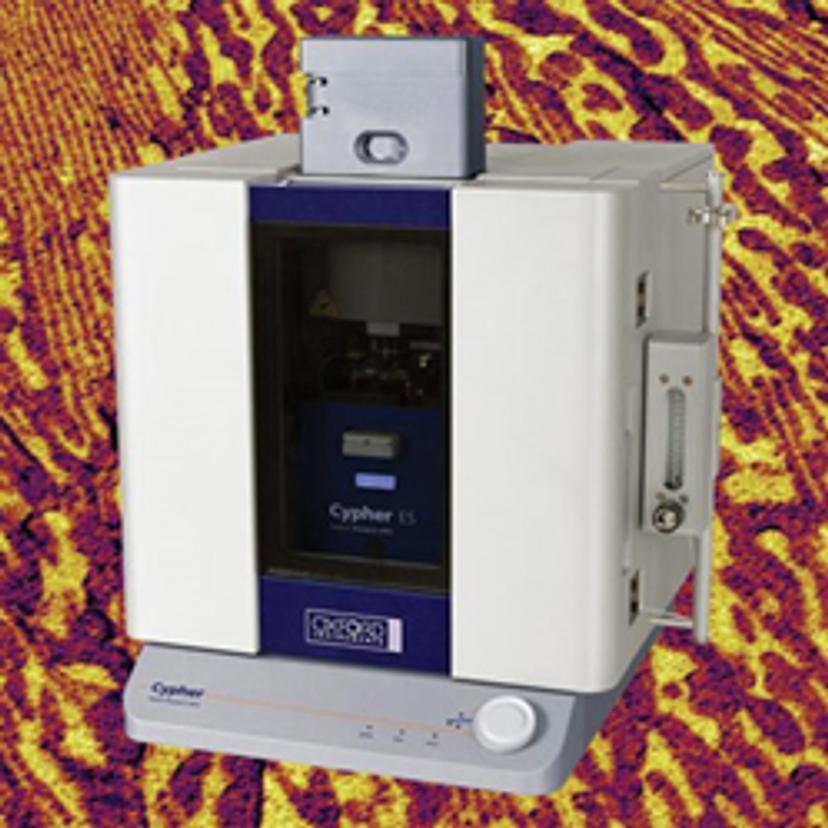
TL: AFM, in general, is a very robust imaging technique. You can essentially put anything under the tip and image it. But there are certain things you can do to help in successful imaging. The Z-piezo range of the AFM can be from 5 microns to 40 microns, so having the sample smooth enough for imaging would be ideal. Microtoming is a good way to prepare the sample. If you're measuring stiffness based on the contact stiffness between the tip and the sample, that depends on the area of contact between the tip and the sample. Having a sample that is not very rough or smooth is advantageous for this.
Q: Can AFM be used to characterize harder materials such as ceramics with larger modulus?
JM: Yes. We have a range of nanomechanical modes that can characterize different materials based on the modulus. We have techniques for looking at very soft materials like biological matter, and also for looking at very stiff materials like ceramics or metals. This is called contact resonance. The probe is placed in direct contact with the surface, the probe and sample are excited, and we look at the frequency of the probe as it's in direct contact with the surface. From this, we can then measure the viscoelastic properties of materials by tracking the resonant frequency and the amplitude of the probe as it scans over the sample.
Q: With old AFM devices, is it possible to obtain polymer surface morphology with contact mode regarding stick-slip effects, or is tapping mode better?
TL: The issue with contact mode is that you're dragging the tip basically at a constant force or load on the sample. It depends on how stiff or soft your polymer is. If your polymer is on the soft side, then this mode might create wear on the surface and contaminate the tip. Tapping mode is a gentler way of imaging a polymer surface and is quicker for getting the morphology of polymer surfaces.
Q: Is it possible to apply AFM for powder samples to know their surface characteristics?
JM: Powder samples are tricky because if they're placed on a surface, they are only slightly immobile. When the AFM tip interacts with the powder particles, it can move them. We have to consider some way of immobilizing the powder particles. This can be done by setting them in resin, for example, or simply by just having electrostatic interactions between the powder and the substrate. You also have to consider the size of your powder particles. If your powder particles are in the micron-scale or above, then it's probably not a suitable technique for AFM. But if you can get your powder particles down to the nanoscale it's definitely possible.
Do you use equipment from Oxford Instruments in your lab? Write a review today for your chance to win a $400 Amazon gift card >>