The importance of thermal management in optimizing battery performance
19 Apr 2023
The number of e-bike and e-scooter fires has surged by almost 150% over the past year; in 2022, the London Fire Brigade alone attended 87 e-bike and 29 e-scooter fires. This has prompted warnings from the UK’s Chartered Trading Standards Institute, encouraging consumers to only purchase devices from reputable retailers. Many of these fires have been attributed to non-compliant lithium-ion batteries, or incompatible charging infrastructure. While many of the incidents have not been severe, serious fires, injury and fatality have been reported and demonstrate the devastating impact of an ineffective battery management system.
Manufacturers must continue to meet stringent safety regulations to ensure the safety and stability of these batteries is not compromised. One factor that must be considered during development and testing is the impact of temperature on battery chemistry.
When exposed to prolonged low temperatures, many electrolytes used in batteries become viscous, steadily decreasing battery performance until the electrolyte freezes, leading to a complete loss in functionality – an irreversible physical change.
Transient exposure to moderate-to-high temperatures can decrease the lifespan of rechargeable batteries, but has minimal impact on performance. In contrast, far more severe consequences are observed if the battery reaches extreme temperatures high enough to trigger electrode decomposition, separator melting, cathode decomposition or thermal runaway.
By carrying out extensive thermal testing, key zones of battery operation can be determined for different environments and applications. This enables manufacturers to take suitable precautions to ensure the safety of users either by constraining battery performance to limit heat generation, or incorporating thermal management systems to cool batteries while in use. Balancing with aesthetics and design streamlining with additional performance driven safety requirements is an important consideration for manufacturers in the development of new battery powered vehicles, devices etc.
Characterizing thermal behavior
Heat generated by an isolated battery cell may be rapidly dispersed into the local environment and may not result in a significant temperature increase, but this may not be the case for the same cell when assembled into a module or battery pack. When the cell is surrounded by other similar cells also generating heat, less energy can escape the system and the temperature will rise. To understand battery thermal behavior, it is therefore important to determine the heat generation rate or power during use under a variety of conditions. Though it is possible to calculate the power from temperature measurements, e.g. using thermocouples or thermistors, the result depends upon use of a suitable thermal model and accuracy is dependent on the model and defined parameters. Direct measurement of power or the thermal energy release profile of a battery can be achieved with suitable battery calorimeters.
Reaction calorimetry
Reaction calorimetry and adiabatic calorimetry are used in cell and battery development, but are less applicable when integrating batteries into products. Reaction calorimetry is used to understand the heat generation profile of a reaction under certain conditions and to identify hazards associated with specific materials used or intermediaries generated during the reaction. During development and transition into cell/battery manufacturing, it is desirable to expand the limits of the safe and optimum zones, producing batteries that work effectively in a range of applications and environments. These characteristics can be determined using adiabatic calorimetry, supported by isothermal calorimetry.
Destructive safety testing will also include a form of adiabatic testing, where the battery is exposed to a range of extreme conditions including thermal abuse, mechanical stress or short circuiting. Data generated during these tests inform the developer of the mitigation required to prevent failure or spontaneous combustion when the battery is in regular use. The adiabatic calorimeter will mimic a worst case scenario where excess thermal energy is not able to dissipate and the cell cannot cool down, leading to a thermal runaway. This can cause structural failure, release of gas or potentially an explosion.
These tests provide the manufacturer with two pieces of information –the maximum safe operating temperature, and the maximum temperature the battery will reach if it catches fire or explodes, allowing suitable protective measures to be installed.
Performance testing
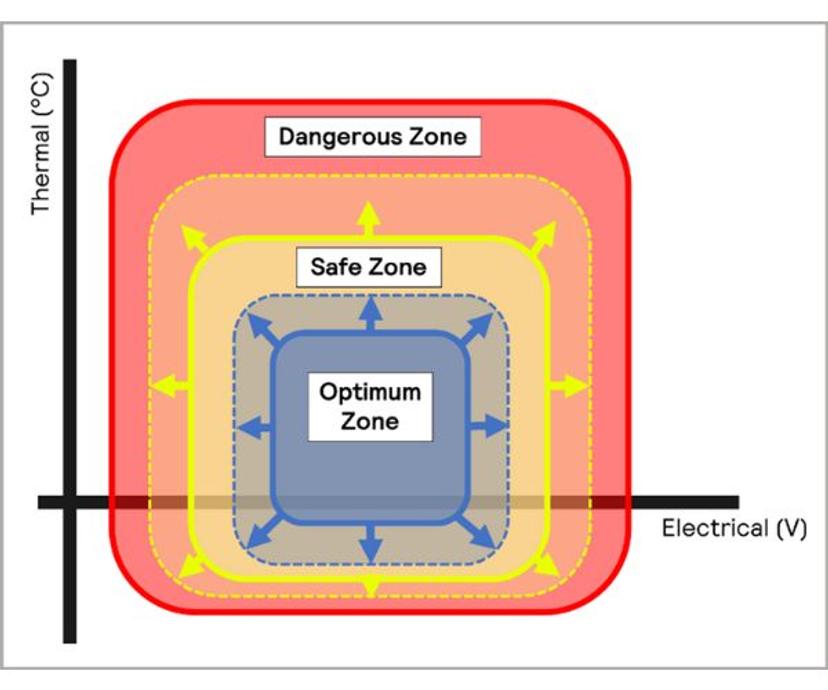
There are two types of calorimetry which can be used to evaluate performance characteristics of a cell – isothermal and isoperibolic calorimetry. These are both non-destructive techniques where the battery is connected to a cycling unit so performance can be assessed under a range of operating conditions.
In isothermal testing, the battery under test is maintained at a constant setpoint temperature and this is critical to achieving accurate results. By measuring the amount of power used by the heaters to maintain the temperature, the heat generated or consumed by the battery under different testing conditions can be calculated.
Isothermal calorimeters typically allow software-integrated control and data collection for common models of battery cycler. This saves time when introducing thermal behavior characterization where measurements can be combined with standard tests. Software integration with a battery cycler simulates normal and atypical usage, and is used to determine the effect of changing charge/discharge rates and repeated cycling.
In isoperibolic testing, the battery’s test environment is maintained at a constant temperature allowing the temperature of the battery itself to undergo slight variations during the measurement. When the battery heats up, heat flow to the cooling system will increase. When the battery cools, heat will be absorbed, reducing the heat flow rate. Once the charge-discharge protocol is complete, the battery and system will return to thermal equilibrium. The greater the difference between the battery temperature and test set point, the faster it loses or gains heat.
Conclusion
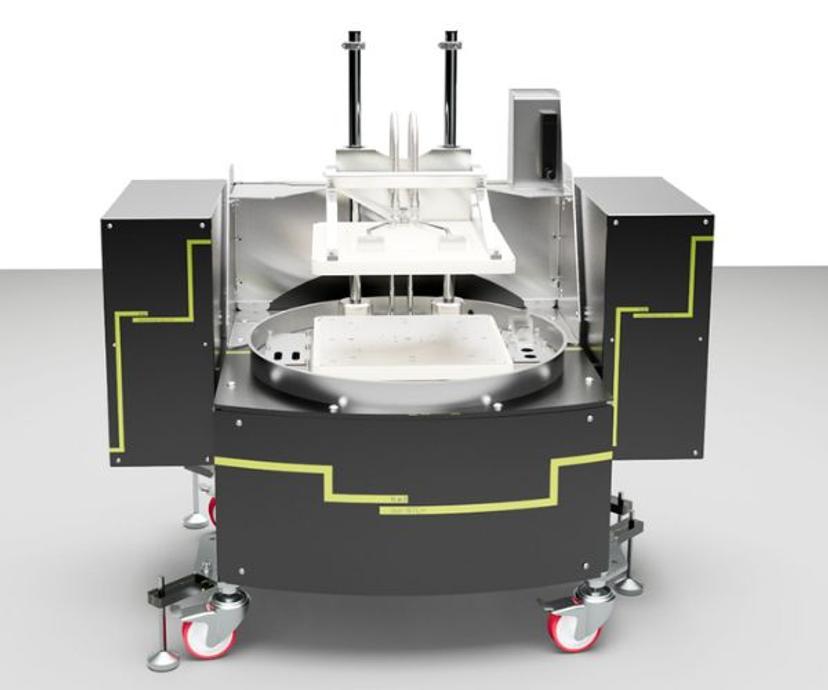
Poor understanding of battery thermal behavior can lead to unsafe batteries being integrated into devices with inadequate safety precautions in place. Alternatively, overly cautious manufacturers produce batteries with avoidable limits on performance, operating environments and optimal safe zones, as well as incurring additional development and material costs due to the inclusion of unnecessarily complex battery thermal management systems.
The heat profile of a battery is dependent on the charge rate, state of charge, device temperature and cell age, the effects of which can be investigated using calorimetry techniques. The data obtained through battery calorimetry can be used to define thermal management requirements, optimum usage conditions, safe operating zones and to maximize product performance. It is imperative to have an in-depth understanding of heat generated by a battery to ensure appropriate safety precautions and usage recommendations put in place, and to minimize the risks of thermal runaways and combustion.
As batteries become more prevalent in electric vehicles and e-scooters, it is imperative that manufacturers continue to research and develop efficient and safe cells, appropriate for all environments and applications.
Want the latest science news straight to your inbox? Become a SelectScience member for free today>>