The power of piezo materials
Explore the significant and revolutionary effects of innovation across different sectors, including consumer electronics and medical applications in piezo materials
3 Feb 2025This guest editorial, written by Clara Ko, Sales and Marketing Director at Linkam Scientific Instruments, highlights the unique properties of piezoelectric and piezoresistive materials and their transformative impact across various industries, from consumer electronics to medical applications.
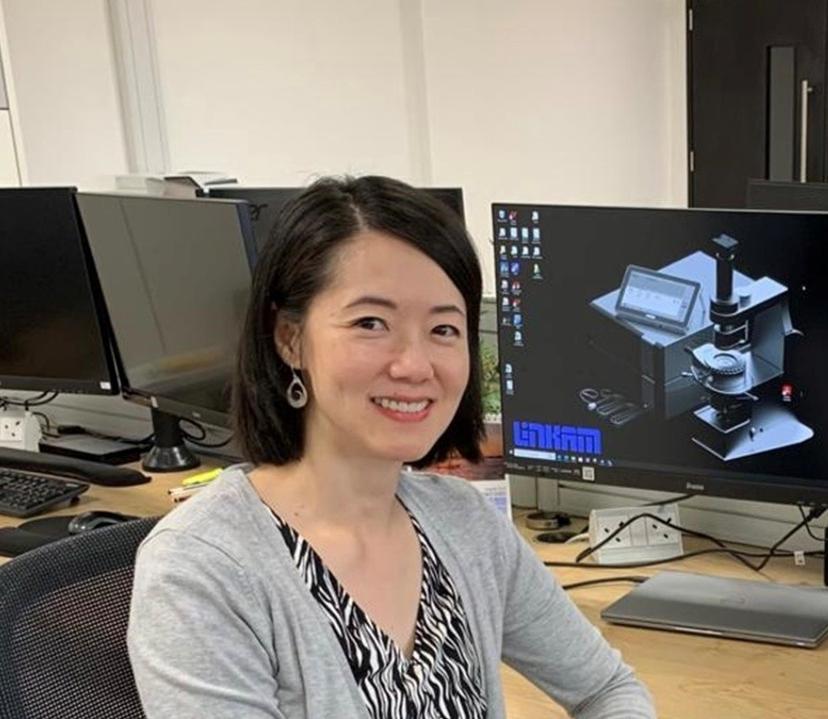
Clara Ko, Sales and Marketing Director at Linkam Scientific Instruments.
The power of piezo materials
Deriving from the Greek word piezin, which means ‘to press’1, the term piezo is most commonly used in materials science to describe how a material behaves when an external force is applied.
Many researchers in the semiconductor field will be familiar with the term ‘piezoelectricity’, which is defined as the phenomenon where there is a connection between the electrical and mechanical state of a material – more specifically, the electrical polarisation that occurs proportionally to the mechanical strain exerted on certain crystals2. Alternatively, ‘piezoresistivity’ describes the change of electrical resistance of semiconductors when external mechanical force is applied3.
Materials with piezoelectric and piezoresistive qualities display remarkable attributes, which makes them well-suited to a number of applications. Here, we will examine piezoelectric and piezoresistive materials in more depth, and highlight how these materials are shaping the future of electronics.
Piezoelectric innovation
The piezoelectric effect is observed in both naturally-occurring materials, such as quartz, and man-made materials, such as ferroelectric ceramics4. These materials produce an electric current when placed under mechanical stress, and there are no shortage of applications that benefit from this characteristic – from defence applications, including military sensors and course-changing bullets, to industrial applications, such as sonar and pressure sensors, to consumer electronics5.
Piezoelectric actuators are one example of a mechanism that uses this phenomenon. These systems convert mechanical stress, (in this case, a voltage or force), into a desired controlling motion6, which is ideal for small devices such as those within consumer electronics. For example, piezoelectric speakers are deployed in gadgets that need to efficiently produce sound from a small mechanism, such as mobile phones, earphones, and musical greeting cards. Another application is inkjet printers, where the actuators are situated in the head of the printer to push the ink onto paper7.
Piezoelectric transducers are another example, and are central to some applications such as ultrasonic testing (defined as the transmission of high-frequency sound waves to detect imperfections or locate changes in material properties)8. When an electrical pulse is applied to a piezoelectric material, the material changes dimension, which causes vibrations. This conversion also works in reverse, and received vibrations can be converted into electrical signals9. Real-world examples of this phenomenon in use include ultrasound imaging, and increasingly ultrasonic surgery (which is minimally invasive and requires a high level of accuracy to improve recovery times and minimise damage to surrounding tissue)10.
As modern technology continues to make use of piezoelectric transducers and actuators, there is a greater demand for researchers to improve their understanding of piezoelectric materials, and identify new ways that they can support emerging technologies.
Harnessing piezoresistance in sensors
Piezoresistive materials are characterised as displaying a change in electrical resistance when an external force is applied. Currently, these materials are mostly used for measuring mechanical strain, such as that associated with displacements and deformations of parts in buildings and machines. However, more recently, applications of these materials are emerging in sport and medical science. This is because piezoresistive materials have proven their worth in devices such as wearable sensors, to monitor heart rate and other small body movements.
To deploy piezoresistive materials more widely across wearable sensor technology, sensor devices must be cost-effective while also maintaining suitability for mass production. Techniques such as roll-to-roll printing can meet these requirements by facilitating efficient printing of both the substrate and electrical component of a device.
Already, this technique is being deployed across wearable sensors. Researchers at the University of Oulu and the VTT Technical Research Centre of Finland have used these printing methods to develop fully printed sensor devices, by printing electrodes and connecting inkjet-deposited piezoresistive carbon nanotube micropatterns (SWCNT) alongside polydimethylsiloxane (PDMS) substrate. The sensor’s functionality has also been tested against variables such as stress, strain, humidity, and temperature, to understand how it will perform in real-world conditions11.
Mechanical deformation and simultaneous electrical measurements were taken to ensure the sensors performed their intended purpose throughout testing. A mechanical testing stage was used to exert stress, while repetitive cyclical testing allowed researchers to examine how the sensor responded to repetitive movement. A temperature-controlled stage was also used to examine how the resistance of the SWCNT pattern was temperature dependent.
As part of the research, the team also investigated optimal sensor printing patterns. Traditionally, straight line patterns are used for sensors that require higher sensitivity, whereas in other sensors, zig-zag patterns might be used to reduce sensitivity to strain and improve durability. In this investigation, researchers tested both straight and zig-zag SWCNT micropatterns, and concluded that pattern design has a large impact on response characteristic of piezoresistive materials.
It was found that the sensor network became less resistant alongside higher temperatures, due to the dependence of electron movement on temperature. When humidity was tested between 10-65%, resistance increased, as the water on the sensor decreased conductivity. The researchers noted that piezoresistivity has a greater influence on the device than temperature and humidity, and thus the sensor could be calibrated to remove these influences if needed.
These experiments showed that the structure and developed stretchable printed material demonstrated high tensile strain sensitivity (up to 400 gauge factor), pressure (∼0.09 – 1 Pa sensitivity) and bending deformation (<10 mm radius); making it ideal for its intended application as a wearable sensor.
With the piezoresistive sensor proving its worth as a viable avenue for wearable sensors, offering a low-cost, versatile, and easy-to-manufacture solution, researchers mounted the device onto skin. The sensor monitored radial artery cardiac pulses, finger flexing and detected chest movement during breathing, at the level of sensitivity required. Furthermore, results suggest that this method of inkjet deposition of nanomaterials can also be used with other printing technology, which opens up a new world of application, from infrastructure to aeronautics.
The future of piezo materials?
Piezoelectric and piezoresistive materials have a firm place in electronics development, with their versatile qualities making them ideal for use across consumer electronics, clinical applications, and more. As research continues into these materials and the benefits they can offer, there is potential for even more applications to be uncovered. The future looks bright for piezoelectric and piezoresistive materials, and they have established themselves as a mainstay in new technologies.
References
1. https://www.collinsdictionary.com/dictionary/english/piezo
2. Smith, A. H. (2008). The Quartz Crystal Microbalance. 133–169. https://doi.org/10.1016/s1573-4374(08)80008-8
3. Rahamim, G., Aliev, S. B., & Zitoun, D. (2019). Inorganic Nanowires for Sensing Applications. https://doi.org/10.1016/b978-0-12-803581-8.11402-x
4. Damjanovic, D. (2005). Piezoelectricity. Encyclopedia of Condensed Matter Physics, 300–309. https://doi.org/10.1016/b0-12-369401-9/00433-2
5. Chandra Sekhar, B., Dhanalakshmi, B., Srinivasa Rao, B., Ramesh, S., Venkata Prasad, K., Subba Rao, P. S. V., & Parvatheeswara Rao, B. (2021). Piezoelectricity and Its Applications. Multifunctional Ferroelectric Materials. https://doi.org/10.5772/intechopen.96154
6. Types And Applications - Piezo Actuators | APC International. (n.d.). Www.americanpiezo.com. https://www.americanpiezo.com/knowledge-center/piezo-theory/actuators/ [accessed 3 June 2024]
7. The Top Uses of Piezoelectricity in Everyday Applications | APC International Ltd. https://www.americanpiezo.com/blog/top-uses-of-piezoelectricity-in-everyday-applications [accessed 16 May 2024]
8. Nondestructive Evaluation Techniques: Ultrasound – Piezoelectric Transducers (n.d.). https://www.nde-ed.org/NDETechniques/Ultrasonics/EquipmentTrans/piezotransducers.xhtml [accessed 3 June 2024)
9. Nondestructive Evaluation Techniques: Ultrasound – Characteristics of Piezoelectric Transducers. (n.d.). https://www.nde-ed.org/NDETechniques/Ultrasonics/EquipmentTrans/characteristicspt.xhtml [accessed 16 May 2024]
10. Sharma, M., Shashikant, Singh, R., Pandey, V., & Sahni, M. (2023). Application of Piezoelectric Material in Surgery. Advances in Intelligent Systems and Computing, 229–236. https://doi.org/10.1007/978-981-19-9906-2_19
11. Ervasti, H., et al., Inkjet-Deposited Single-Wall Carbon Nanotube Micropatterns on Stretchable PDMS-Ag Substrate–Electrode Structures for Piezoresistive Strain Sensing. ACS Appl. Mater. Interfaces 2021. https://doi.org/10.1021/acsami.1c04397