Thermo Electron to present broad range of analytical and process
9 Apr 2006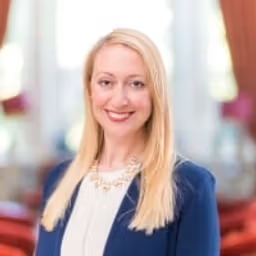
Thermo Electron Corporation, an industry leading producer of process and analytical instrumentation, will showcase a range of rheometry and measurement equipment for polymer applications at Chinaplas 2006, to be held April 26-29 in Shanghai, PR China.
Among Thermo Electron’s featured products will be the HAAKE PolyLab Open System (OS) torque rheometer platform designed for polymer processing applications. The platform’s system architecture incorporates an open industry standard that allows multiple sensors and systems to be added for comprehensive viscosity and spectroscopy measurement. One major advantage of the HAAKE PolyLab platform is the high degree of flexibility offered by the “plug & measure” design. The standardised CAN Open Bus and USB interface allow the torque rheometer to be adapted quickly and easily to different applications or new sensors.
The HAAKE Modular Advanced Rheometer System (MARS) for R&D applications also will be showcased. The instrument measures the viscous and elastic properties of a wide range of samples in rotation and oscillation. The HAAKE MARS’ modular design allows all key components to be interchanged, including the measuring head and electronic unit. The rheometer’s low mass moment of inertia combined with lightweight titanium moving parts allows measurements to be performed on diluted samples even at the lowest of torque levels. The motor is configured to allow solids to be deformed precisely.
A featured product from the Radiometrie product line will be the Radiometrie RM 200 EK/RM 210 EK system with its operator station on display. The Radiometrie system measures the thicknesses of extruded plastics film and biaxially stretched film. The system can be equipped with automatic die control of the foil thickness and the foil cross profile to enable significant improvements in product quality and to reduce time when making product changes. The die control includes power electronics connected to the measuring system via interface to control the heating power of each of the die’s individual expansion bolts. This allows for as many control loops as there are extrusion die bolts. Alternatively, temperature set-profiles can be transferred to the die instead of a heating power set-profile. Foil thickness is controlled by an additional control loop which adjusts the haul-off speed of the chill roll, dependent upon the measured thickness cross profile average (thickness control).
Finally, Thermo will display the Radiometrie RM 300 ED differential thickness gauge, which offers both uniform coating and raw material savings. The gauge is used in production lines when a base material is coated with one or more layers. The coating's basis weight cross profile is computed and displayed as the difference between the coated final product and the base material. Measurement of more than one layer can be accomplished by adding a gauge for each additional layer.