X-ray fluorescence for mineral analysis: Using the best tools for the job can make all the difference
Prof. Saúl Loaiza shares the importance of robust quality control in mineral analysis by using high-quality in-the-field analyzers
7 Jun 2022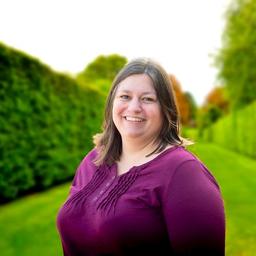
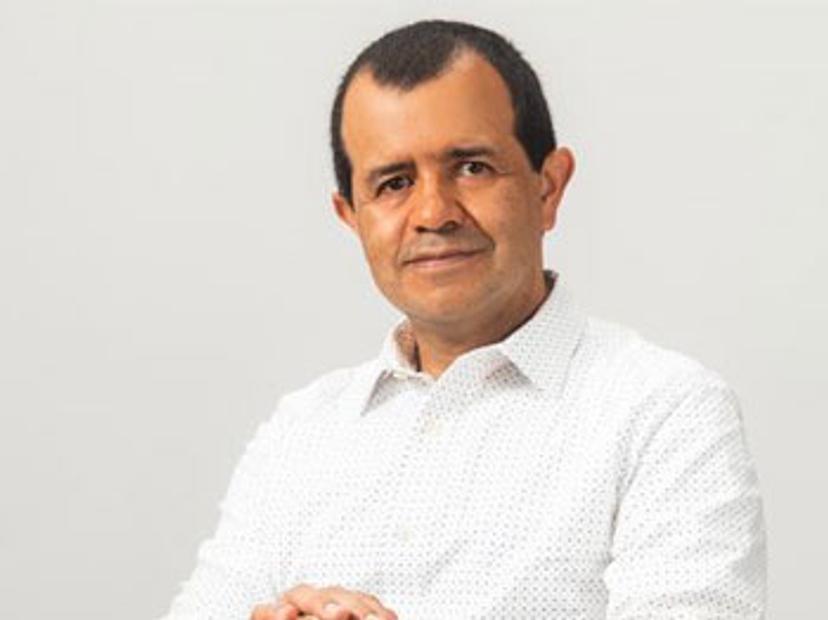
To get the big picture to fall into place, we must look at the smaller things. Every aspect of our lives – our buildings, our cars, products in our homes, and the food that we eat – needs to be safe and of high quality, and mineral analysis is a key method of ensuring this.
Given the importance of mineral analysis to a range of industries – and, ultimately, vast amounts of our modern lives – it is essential that scientists have access to the latest and best techniques so that analysis can be done quickly and accurately, as well as in the field if necessary.
In this article, we speak with Professor Saúl Loaiza, an independent advisor in applications and analytical technology, and Radioactive Safety Officer and Professor of Chemistry at Universidad del Valle de Guatemala. He tells us about the importance of fast, accurate mineral analysis in industry and how X-ray fluorescence delivers that.
The value of mineral analysis
Mineral analysis is a common quality control method for many industries. For example, food producers use the process to analyze and improve their growing conditions – including ensuring the perfect soil in vineyards1. In his consultations with the food industry, Loaiza has found “they require quality control analysis for fertilizer samples, vegetables samples, soil samples, raw material and final product.” Another field that takes advantage of the method is cement manufacturing.
Before joining the Universidad del Valle de Guatemala, Loaiza worked in the cement industry for over 25 years. Cement manufacturers use mineral analysis to ensure that their product is the right mix, and therefore the right quality. Concerning this work, Loaiza emphasized that: “You need to know the chemical composition in process samples to control the quality of the materials.”
Analysis is not just information-gathering and does not stop at sample taking - the information needs to be used to adjust the product or ingredients. “Adjustments must be made in order to ensure the quality of the products at each stage of the cement manufacturing process. Each element quantified by X-ray analysis plays an important role,” explains Laoiza. “The cement must comply with the regulatory and customer requirements. Quality control must be carried out through chemical measurements – for example, by X-ray fluorescence – and physical measurements to achieve the final performance of the product.”
Analysis improvements over time
Loaiza has used many analysis approaches over his career and is always looking for the latest techniques and technologies that can speed up and improve mineral analysis. One of his favored techniques is X-ray fluorescence (XRF), which he hopes can one day replace the use of other, potentially dangerous, techniques.
“XRF is an analytical technique that reduces analysis time, is non-destructive, and is very easy to use,” Loaiza explains. “XRF could replace the current method of analysis - inductively coupled plasma (ICP) spectroscopy – which involves digestion of samples with corrosive acids, longer preparation time, longer analysis time, and greater risk to the operator.”
The technique itself isn’t the only thing that supports effective mineral analysis. Improvements in products that support the use of XRF have made large changes in recent years, greatly increasing the number of minerals that can be analyzed, the types of samples that can be taken, and the processing speed.
These improvements have huge benefits for laboratories and their processes. “Analysis time reduction increases the decision-making time to make changes in the industrial process,” Loaiza explains. “It presents less risk for the operator in the preparation of samples because it doesn’t use acids, and it improves the precision and accuracy in the analysis.”
“I have seen a lot of changes in X-ray in my career,” shares Loaiza. “Twenty-five years ago, the XRF equipment only had the capacity to analyze six elements and the analysis time was five to ten minutes. We need to adapt and adopt new technology as time passes by us, if we want to get results faster and with accuracy.”
The perfect fit with the Epsilon 4
For his XRF analysis, Loaiza uses the Epsilon 4 by Malvern Panalytical for its promise of high throughput, analysis times of less than five minutes, and its ability to analyze liquid samples and different kind of samples.
“Some of the analytical options in the Epsilon 4 X-ray equipment mean you can create analytical curves for common elements in minerals, and general curves for analysis of unknown samples”, Loaiza says. “The type of sample to be analyzed can be in the form of press pellet, fuse pellet, solid samples on special cassette, and liquid samples in an environment with Helium gas.”
The product itself is also easy to set-up and use. “No large and special spaces are required for installation. The software is friendly to use, in the analysis and calibration for the operator,” Loaiza concludes. “Also, you can analyze different samples (up to 10) without supervision and it is possible to use it by remote access, so you can adapt it into an autonomous robotic system.”
References
M.Likar, K Vogul-Mikuš, M Potisek et al. Importance of soil and vineyard management in the determination of grapevine mineral composition. Sci Total Environ 2015.