How Your Food Packaging Quality and Safety Are Ensured
Food packaging is subject to many regulations and challenges, learn how the team at global printing ink supplier Sun Chemical manages to stay one step ahead
9 Mar 2017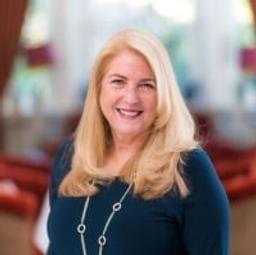
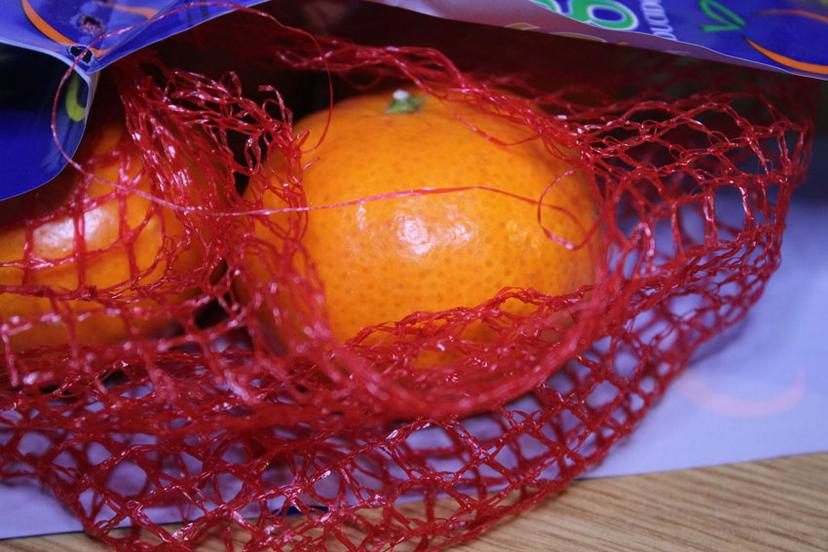
Learn about reliable technologies helping Sun Chemical to meet food packaging regulations
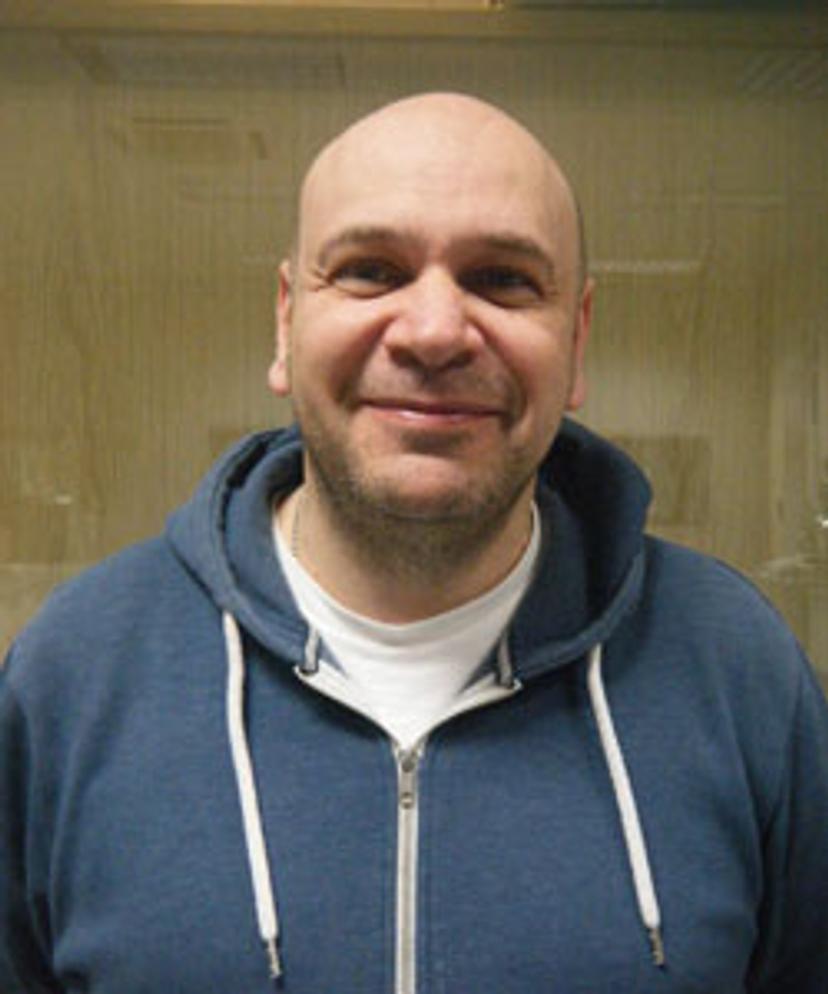
Neil Terry, Regulatory and Product Steward at Sun Chemical
Maintaining safety and quality standards within the food packaging industry is a lot more complex than the average shopper might realize. SelectScience® spoke to a man right on the frontline when it comes to meeting the many printing ink regulations and protecting consumers from any potential health risks. Neil Terry is Regulatory and Product Steward at Sun Chemical, the largest supplier of printing inks worldwide and is based at the company’s Rochdale Technical Centre. The department works, together with Sun Chemical’s suppliers and customers, to ensure food packaging is compliant with all the relevant regulations.
One of the major regulations the inks must comply with is Regulation (EC) No 1935/2004, article 3, which states that Materials and Articles must be manufactured in accordance with Good Manufacturing Practices (GMP) so that they do not transfer constituents to food in quantities that could:
- Endanger human health
- Bring about an unacceptable change in the composition of food
- Deteriorate the organoleptic characteristics of food
In basic terms, explained Mr Terry, this means stopping any component potentially migrating from Sun Chemical's inks, through the packaging and into the food at levels that are above the ‘specified migration level’.
The company plays a vital role in all this by issuing ‘Statements of Composition’ to its customers, listing the potentially migratable components and the level they are present. It provides this information following similar declarations gathered from suppliers of the 5000-plus raw materials it currently uses. In addition, the department is called upon to answer the many regulatory questions its customers and the final end-users might ask.

Sun Chemical is a leading provider of printing inks and materials for packaging.
Alongside the safety aspect, there is a practical need to ensure printed inks reach customers in a good condition. When the inks are printed, they are stored in large reels which are then sent to the customer.
The pressure within these reels is immense which means there is a danger of an issue known in the industry as ‘blocking’. Blocking happens when the reel is unwound and the printed side sticks to either the reverse of the print or to the printed side, depending on which way the reel has been wound on the press.
Mr Terry explains: “If this happens, it can be costly both in terms of loss of materials and press-time.”
There are various additives which can be added to the ink to prevent this, so to guard against such eventualities, Sun Chemical uses Specac presses to test for potential blocking. Pieces of print are simply put in a Specac manual press for a certain length of time at a certain pressure in order to test to see if blocking could occur.
Despite the changes within the industry, the team has been able to stick with these same machines from Specac for years and is happy to sing their praises.
“Our machines are very old, but the fact they are regularly used and reliable is proof about the quality of them,” says Mr Terry, whose job it is to oversee the calibration of all lab equipment on site. “We believe the presses we use to be around 30 years old and envisage using them as they are for many years yet. When they are serviced and calibrated they are always in good working order.”
We believe the presses we use to be around 30 years old and envisage using them as they are for many years yet.
Neil Terry Sun Chemical
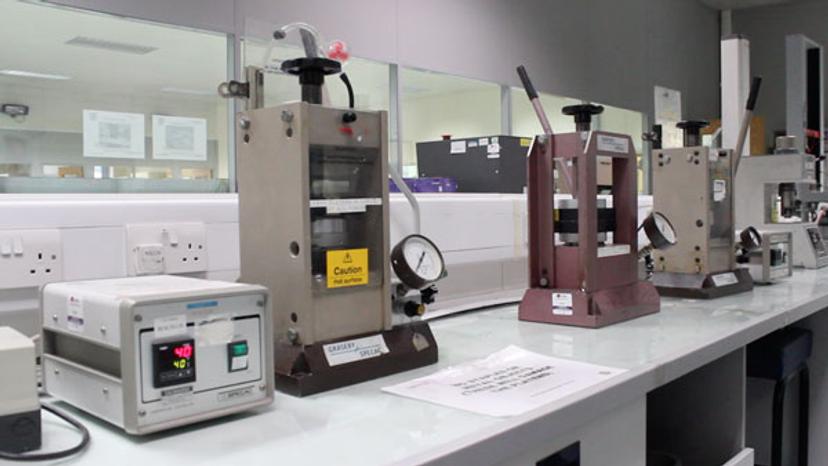
The Specac manual presses at Sun Chemical
The longstanding dependability of these presses must come as some relief to the team at Sun Chemical as it gets to grips with an ever-increasing array of regulations and fresh challenges.
“From a regulatory point of view, printing inks are more regulated than they were 10 years ago,” says Mr Terry.“There are always many new challenges facing staff in the R&D laboratory as each customer, press and end-use has its own unique challenges. To stay still in this business means that you can fall further behind the competition.”