Corning® Ascent® FBR PD Controller 230V
The Corning Ascent Fixed Bed Reactor (FBR) system is designed to enable process development and production scale cell culture capacities for cell and gene therapy workflows with greater yields that can result in substantial cost savings over competing FBR systems. Also, unlike competing FBR systems, the Corning Ascent FBR system is designed to provide viable cell harvest capability that can enable it to be used as seed train a…
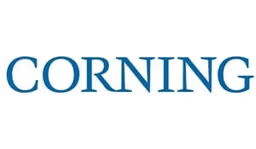
The supplier does not provide quotations for this product through SelectScience. You can search for similar products in our Product Directory.
The Corning Ascent Fixed Bed Reactor (FBR) system is designed to enable process development and production scale cell culture capacities for cell and gene therapy workflows with greater yields that can result in substantial cost savings over competing FBR systems. Also, unlike competing FBR systems, the Corning Ascent FBR system is designed to provide viable cell harvest capability that can enable it to be used as seed train and potentially for other applications that require the ability to harvest large quantities of cells. The novel fixed bed bioreactor platform is designed to deliver significant surface area intensification and high-yield bioproduction capability by providing uniform media flow, in order to enhance cell health and drive uniform high-density cell growth.
- High cell yield provides significant cost saving opportunities via specially treated woven mesh polymer substrate which provides
- Uniform fluid flow – efficient nutrient delivery and waste removal
- Uniform cell growth – even cell distribution and confluence at transfection
- High cell yield and per cell productivity with 20X greater AAV yield compared to competitive FBR systems
- Designed to harvest viable cells with >90% recovery
- Harvest capability enables the bioreactor to be used for seed train, streamlining vessel-to-vessel cell transfer
- Bioreactors scale from 1 m2 to 5 m2 with future capacities up to 1,000 m2
- Linear scalability from process development to production size can save process development time/cost (reduced time to market)
- Minimal set up required, no autoclaving necessary, no probe calibration required, can save many hours of your valuable time
- Set up system in as little as 20 minutes
- Ready to use consumables that are gamma irradiated
- Closed system
- Can be run outside a laminar flow hood
- Lynx® connectors or tube welding allow for easy benchtop aseptic cell sampling of the bioreactor
- Automated control, including disposable sensors that monitor DO, pH, temperature
- Reduced labor costs, hands-off operation, reduced risk of human error