3 Ways Pharma Can Reduce Costs and Increase Innovation with ‘Green Chemistry’ Technology
29 Sept 2014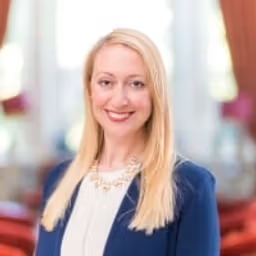
An expert panel at CPhI, one of the leading pharma industry conferences, warns “IPR is stifling innovation”; predicts that a “process-centric approach will achieve global revenue savings of 20 to 25%”, with “green chemistry set to help drive manufacturing cost reductions”
Revolutionary ideas to help make drug development and manufacturing more efficient, along with new technologies such as ‘green chemistry’, were identified in the first part of the CPhI annual report by world-renowned experts Vijay Shah, Executive Director & COO of Piramal Enterprises, Dilip Shah CEO of Vision Consulting and Girish Malhotra, President of EPCOT International. Each forecast their predictions for the industry, advocating radical changes that will revolutionize production processes and profits, and reduce environmental impact.
What is green chemistry?
Industrial chemical manufacturing processes use a number of organic solvents for separation and purification of products. The manufacturing process is energy intensive and is associated with generation of waste that is environmentally hazardous in nature. An important parameter to understand the efficiency of chemical reactions is the Environmental (E)-factor, which measures the kilograms of waste produced per kilogram of product. Green chemistry technology seeks to reduce the negative impact of chemistry on the environment by preventing pollution at its source and using fewer natural resources.
Three ‘Green Chemistry’ technologies:
1. Catalysis Systems
When scalable and inexpensive enzymatic conditions are screened and identified at the process research stage, the process ultimately becomes significantly more cost-effective, resulting in reduced E-factors, fewer steps and therefore less waste. A process research program can excel when expertise available in catalysis is well utilized toward green synthetic routes. This video from HEL Ltd demonstrates how a parallel reaction system for the rapid development of high pressure reactions and heterogeneous catalysis systems can work.
2. Flow Chemistry
When a chemical reaction is run in a continuously flowing stream, rather than in batch production, it can minimize the amount of waste generated, increase productivity and decrease capital at the large scale. The flexibility of recent flow chemistry technology allows the design of a reactor based on the reaction, with products available for all aspects of the drug discovery process. Technology advances include coupling and hydrogenation reactions using SiliaCat catalysts; FlowSyn Continuous Flow Reactors for reaction optimization, synthesis and scale-up; and the 1260 Infinity Preparative Scale Purification System for high throughput requirements of combinatorial and medicinal chemistry core facility labs, or as a method scale-up solution for optimizing the resolution and recovery of individual compounds.
3. Parallel Screening
With the aid of high throughput screeningand technology such as the BMG LABTECH’s CLARIOstar® and BellBrook Lab’s Transcreener® HTS Assays, it is possible to conduct hundreds of reactions in parallel for a given transformation during the feasibility stage of route scouting.
“Already we are seeing big pharma looking increasingly to explore greener ways of working and the manufacturing process is a natural progression of this trend. Technologies such as catalysis, flow chemistry, and parallel screening are revolutionizing process research, by creating efficiencies and cost savings” commented Vijay Shah.