Automate FIB Processing for High-Throughput TEM Lamella Preparation
Creating TEM lamellae with the new Ion-sculptor FIB column of ZEISS Crossbeam
18 Oct 2018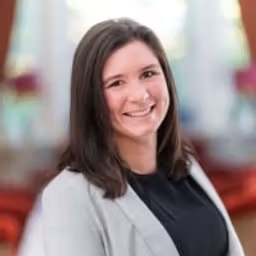
The ZEISS Crossbeam FIB-SEM combines the powerful imaging and analytical performance of a field emission scanning electron microscope (FE-SEM) column with the superior processing ability of a next-generation focused ion beam (FIB). It therefore enables applications like imaging & analytics, tomography as well as sample preparation & nanopatterning.
With the new Ion-sculptor FIB column you minimize sample damage and maximize sample quality – and perform experiments faster at the same time. You can customize your instrument to achieve both high quality and high throughput in TEM lamella preparation.
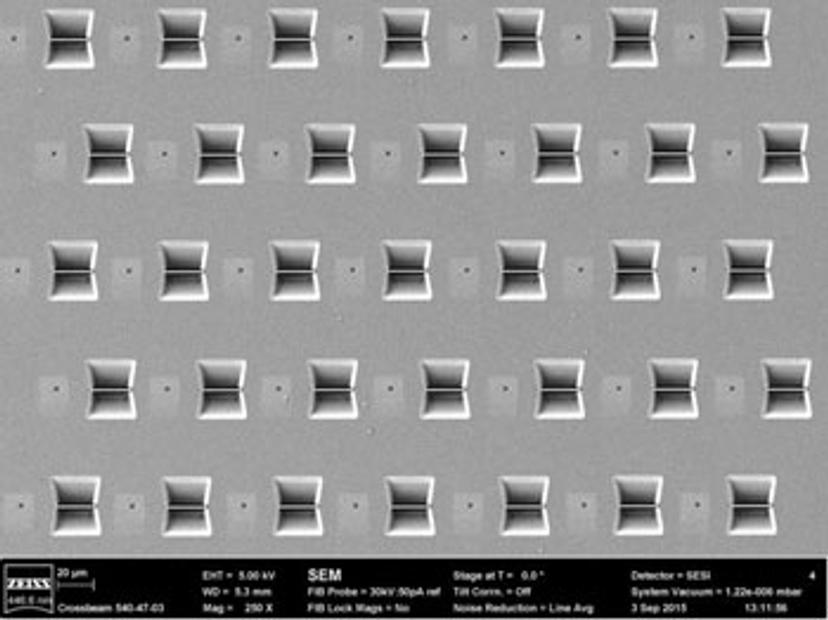
It’s easy to create TEM lamellae
When preparing TEM lamellae use the low voltage capabilities of the Ion-sculptor FIB: get ultra-thin samples while keeping amorphization damage at a minimum. Thanks to the automation of the first two steps it is even easier than before to create TEM lamellae with ZEISS Crossbeam.
How to prepare TEM lamella using ion-sculptor FIB
You begin the workflow without time-consuming search for the ROI and use the navigation camera on the airlock instead to locate specimens. The integrated user interface makes it easy to navigate to your ROI. You benefit from the large, distortion-free field of view in the SEM.
You start the preparation with a simple three-step process: ASP (Automated Sample Preparation) and define the recipe including drift correction, deposition and coarse and fine milling. The ion optics of the FIB column enables high throughput for the workflow. You can duplicate the recipe and repeat as often as required in order to start a batch preparation.
You bring in the micromanipulator, attach the lamella to its tip and cut out the lamella from the bulk. The lamella is then ready for lift out and can be transferred to a TEM grid.
The instrument’s design allows you to reach a desired thickness of the lamella by enabling live monitoring of the thinning. You use two detector signals in parallel to judge lamella thickness and to obtain reproducible end thickness on the one hand (with the SE detector) and to control surface quality on the other hand (with the Inlens SE detector).
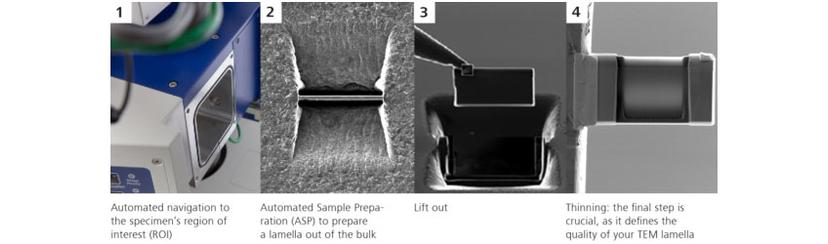