Degenerative eye diseases: Startup scientists devise pioneering curative treatment
How scientists at Kato Pharmaceuticals have expanded from early-stage development to biopharmaceutical production of clinical drug products
20 Sept 2021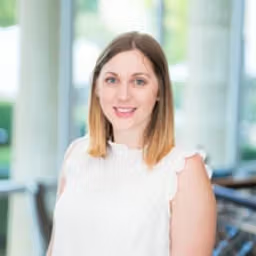
Diabetic retinopathy is the most common diabetic eye disease and is the leading cause of blindness in American adults1. Diabetic retinopathy can also lead to other serious eye conditions, including diabetic macular edema, neovascular glaucoma, and retinal detachment. While current treatments provide temporary relief of symptoms, they are not curative, and there is increasing demand for innovative therapies to inhibit the progression of this disease.
In this interview, we speak with the team of scientists at Kato Pharmaceuticals, Inc. to hear about their vision to bring new biopharmaceuticals to the market for site-specific treatments of degenerative ocular diseases and how a partnership with Thermo Fisher Scientific has enabled this startup to streamline its R&D and manufacturing processes and expand from benchtop to commercial-scale production.
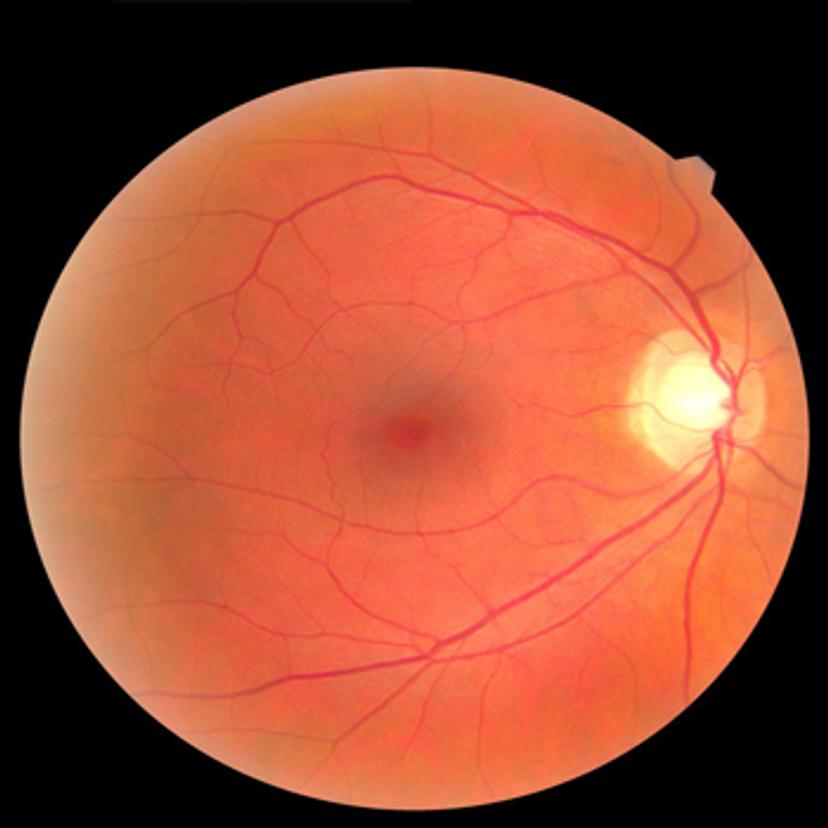
Curative treatment for diabetic retinopathy
Diabetic retinopathy is caused by spikes in blood glucose which stimulate growth factors secreted by the retina which trigger the proliferation of new abnormal fragile blood vessels – called neovascularization – in the retina and can lead to serious problems with vision, and ultimately vision loss.
In response to this, demand is growing for more sophisticated and curative treatments – something that the team at Kato, a startup based on the west coast of the USA, is passionate about.
“Currently on the market, there are options that treat the symptoms of diabetic retinopathy and provide temporary relief for patients. Patients have to see their doctors regularly to get the treatments every three to six months to slow the progression of the disease,” explains Jeda Voska, senior manager of R&D and engineering at Kato. In a huge step forward from that, the drug product developed by the team at Kato, currently in clinical trials, would provide a curative treatment for the disease, requiring just one or two injections, delivered to the eye – an innovative solution that could change the lives of patients. In addition, the patented technologies developed by the team at Kato offer site-specific intraocular treatment platforms that Kato will leverage for additional ophthalmic drug products to treat other degenerative ocular diseases.
Biopharmaceutical development and manufacturing in-house
Voska, who oversees everything from R&D to product development, engineering, manufacturing and quality activities, is part of the small team of scientists driving the development of high-quality innovative biopharmaceuticals for degenerative ocular diseases. The company has transitioned from purely R&D discovery and development in the lab to manufacturing drug products in GMP cleanrooms in-house. “We have our own cleanrooms now, where we build our clinical product and have carried out all process development activities, starting with the manufacturing of benchtop-size lots and scaling up all the way through commercial size batches,” says Voska.
This process did not come without its challenges. Voska explains: “Naturally, the first challenge that we faced here at Kato was the formulation development work. To do scientifically sound development work, you need a reliable laboratory setup with the appropriate laboratory equipment and tools to be able to measure the chemical and physical properties of the formulations you're trying to develop.”
The group also needed to scale up production, from small benchtop batch sizes to the clinical batch sizes required for clinical trials. A process where, again, Voska highlights the importance of stocking the laboratory with the appropriate equipment and supplies to handle large volumes and processing, as well as analytical instruments used to monitor this work.
Hand in hand with this scale-up was the ability to increase testing throughput. “We also face the challenge of being able to have a higher throughput for our testing capabilities, to handle both process and product development testing, as well as stability testing for all of our drug product batches,” says Voska.
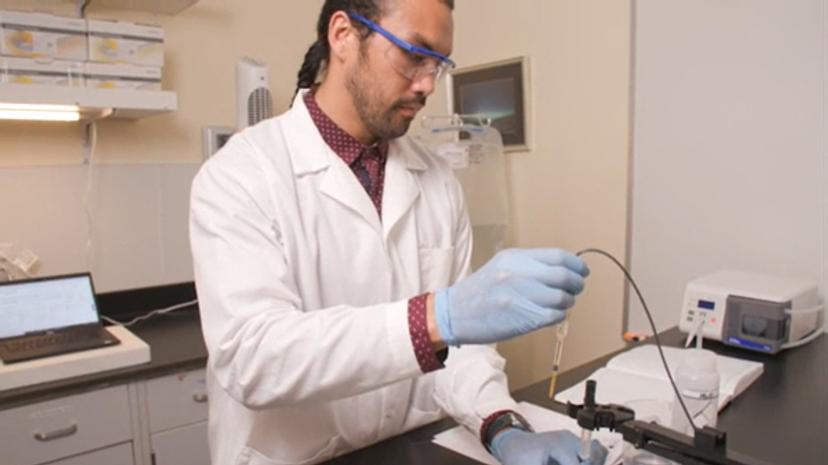
An ideal partnership for scaling up
Key to the success of the lab has been a partnership with Thermo Fisher Scientific, which the company works with to source equipment – from items as simple as pipette tips through to sterile bioprocessing containers and raw materials. “As a small company, we move very quickly, we can change direction, and then almost immediately, we'll need a material or consumable product that we may not have on hand,” notes Voska.
The team highlights the ability to purchase the exact equipment they need to the necessary timelines as well as a wealth of expertise and technical assistance from Thermo Fisher Scientific that has helped identify the best products for its work. “We work closely on sourcing, purchasing consumables, the equipment for production, R&D, and our testing needs. Which goes hand in hand with purchasing every material we require for making our drug product itself,” says manufacturing engineer Kory Alpichi.
Voska adds: “One thing that I found very beneficial, and that we love working with Thermo Fisher for, is their technical support. We can go to them, and we can say we need something as simple as a heated water bath or a centrifuge or a pH meter, and they're able to put us in contact with the right support to help us find the item that will benefit us the most, from research and development on the bench through to the production of a clinical trial product.”
The importance of reproducible analytical testing
“Our policy is to manufacture the drug at its highest quality. It has to be safe and it has to be effective,” says Maria Rosadel ‘Madel’ Dionisio, Kato’s senior regulatory and clinical engineer.
Analytical testing plays an important role throughout the development and processing of biopharmaceuticals to ensure quality and safety. Some of the key tests that the team at Kato performs are to measure pH, ammonia, and dissolved oxygen. Associate quality engineer Edward Fahman explains: “Essentially, these tests are our first line of defense in regard to confirming and determining the quality of our drug product. That's because pH and ammonia are the most vital and critical testing that we use, for not only release testing but also stability testing down the line, to ensure that our product is still stable.”
The nature of Kato’s product means that it was essential to find the right equipment for this work. “Our drug product is atypical in the sense that it has very high concentrations of chemicals, extreme physicochemical properties that make testing trickier than if you were measuring the pH or ammonia of something like water,” says Voska.
In these analyses, the team uses a range of products from the Thermo Scientific™ Orion™ range of meters and electrodes to support high-throughput testing, including the Thermo Scientific™ Orion™ Dual Star™ pH, ISE, mV, ORP and Temperature Bench Meter andThermo Scientific™ Orion™ Versa Star Pro™ pH/ISE/Conductivity/Dissolved Oxygen Multiparameter Bench Meter. To attain accurate readings, they pair the meters with Thermo Scientific Orion electrodes, including the ROSS Micro pH Electrode, ROSS Ultra Triode pH/ATC Electrode and the Orion™ Ammonia Gas Sensing ISE Electrode.
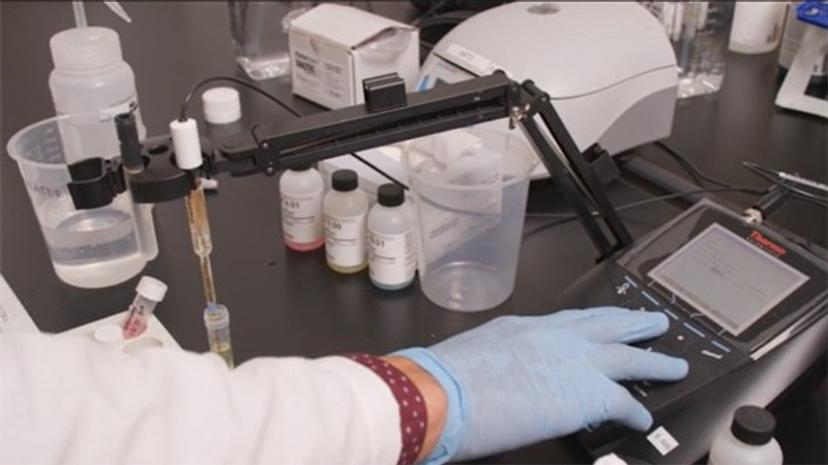
The team at Kato speaks highly of its experience working with Thermo Fisher Scientific to source, install and maintain the equipment. “They have been wonderful in working with us to really fine-tune a lot of our testing needs related to use of their meters, various options for pH probes, dissolved oxygen probes, or ammonia probes, and supply us with the correct pieces of equipment so that we can scale up from fewer measurement reps to performing high-throughput testing,” says Voska.
The team has found the instruments to be easy to use, accurate and reliable. Fahman highlights: “I believe that Orion ROSS electrodes, equipment, and materials have saved us hours and hours of frustration and have led us to find a reliable source for our testing.”
The team also highlights the role these instruments have played in the success of the company’s efforts to develop new treatments. “This has enabled us to provide reassurance and confidence that our drug product will be safe for use in our clinical trials as well,” says Alpichi.
Voska adds: “Without having the right equipment and the right source for the right supplies in a laboratory and in a cleanroom, you can't make discoveries that will help change people's lives. This really enables us to make great strides in the discovery and development of novel drug products that will change the face of intraocular treatment and cure degenerative ocular diseases such as diabetic retinopathy.”
The future at Kato
In the future, the team at Kato is looking forward to seeing their products improve the lives of patients. “For the future here at Kato, our goal is to get our diabetic retinopathy drug product through clinical trials and on to the market as soon as possible and to continue to develop more site-specific drug delivery systems that treat degenerative ocular diseases in a space where curative intraocular treatments are highly needed,” says Voska. “The eye is such a complex, unique part of our body, and to be able to bring a more elegant treatment to the market, cure degenerative ocular diseases and prevent blindness in as many people as we can, that's what drives us and that’s we're looking forward to in the future!”
Meet the scientists behind Kato Pharmaceuticals
Jeda Voska, Senior Manager, R&D and Engineering
Jeda is an experienced CMC and R&D biopharmaceutical scientist with over 10 years of experience in pharmaceuticals and medical devices and she has a B.S. in chemistry from UCSB and a master’s degree in chemical engineering from USC. At Kato, Jeda oversees R&D, product development, manufacturing, quality and regulatory activities with support from the Kato scientific consulting team.
Kory Alpichi, Manufacturing Engineer II
Kory has a bachelor of science in chemical engineering from Hampton University and has worked at Kato for over three years. In this role, Kory oversees manufacturing, process development and engineering activities.
Edward Fahman, Associate Quality Engineer
Edward has a bachelor's degree in biomedical engineering from University of California Irvine. At Kato, he specializes in quality, manufacturing and R&D activities.
Maria Rosadel ‘Madel’ Dionisio, Senior Regulatory and Clinical Engineer
Madel has a bachelor's degree in chemistry and a wealth of experience in regulatory affairs, clinical trials and quality activities for the pharmaceutical industry. At Kato, Madel is responsible for the clinical, quality, and regulatory affairs activities.
References
1. National Eye Institute. Diabetic Retinopathy Data and Statistics. [Online]. 2020. Available here.