Edwards' Dry Pump Technology Improves Energy Efficiency and Lowers Costs
28 May 2013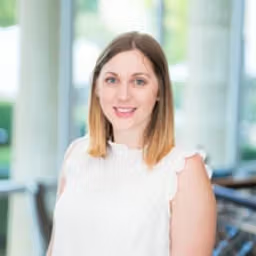
Edwards Group Limited, a leading manufacturer of sophisticated vacuum products and abatement systems and a leading provider of related value-added services, has aided a large pharmaceutical company to reduce its costs and improve efficiencies by supplying them with an order of XDS dry scroll vacuum pumps. Since installing the pumps, downtime has been significantly reduced, as have maintenance and servicing costs, and operational efficiencies have increased.
A large company with more than 400 vacuum pumps at its research and development centre on the East Coast of USA was looking for a simple and reliable vacuum pumping solution that would enable it to reduce maintenance requirements.
They were previously using rotary vane pumps in their laboratory freeze dryers, but as oil-sealed pumps they need regular oil changes. The company also had prior experience of using an Edwards XDS dry vacuum pump on a laboratory freeze dryer and was impressed by its reliability and performance.
Edwards worked closely to understand the requirements from the pump and recommended its XDS35i dry scroll vacuum pumps. The XDS range incorporates a unique dry pumping scroll mechanism that provides a robust and clean pumping solution for scientific applications.
Dry pumps have no lubricants under vacuum, eliminating the need for regular oil changes, therefore reducing maintenance and environmental impact. It also means there is no possibility of process contamination, an important benefit in high cost pharmaceutical applications.
Alternative pumping technology was also reviewed, but Edwards’ XDS pump performance and maintenance requirements proved to be superior. Annual repairs, labor and maintenance for Edwards’ XDS10 and XDS35i dry pumps are on average three times less than that for oil- sealed pumps.
As a result of installing the XDS dry vacuum pumps in its freeze dryers, significant savings to maintenance costs, a reduction in downtime and a more efficient process have all been achieved. The pump’s water vapor capability has improved drying time on laboratory freeze dryers by 50% and there has also been a significant reduction of noise and heat in their labs.
“We are delighted with the opportunity of being able to help our client benefit from the operational and environmental advantages of dry pump technology,” says Bob Campbell, Industrial and Process Market Sector Manager - Americas, Edwards. “The patented XDS design means the bearings are isolated from the vacuum so no bearings, bearing purges, grease or oil are under vacuum. As a result, the pump is virtually maintenance free and provides the perfect solution for ‘plug and play’ vacuum pumping in scientific applications.”