Formlabs create 3D printed nasal swabs during emergency shortage situation
With medical equipment in short supply, the 3D printing company steps up in coronavirus crisis
15 Apr 2020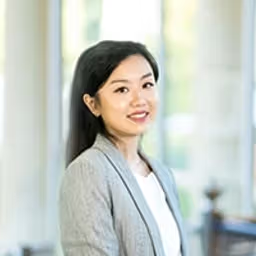
The University of South Florida (USF) Health, Formlabs, a leading 3D printing company, and Northwell Health, New York's largest healthcare provider, have announced they have successfully produced and tested a 3D printed nasal swab to address emergency shortages that hospitals and health care teams may face as testing for COVID-19 increases.
Key milestones in testing the swabs were conducted by USF Health faculty researchers in the Departments of Radiology and Infectious Diseases in collaboration with Northwell Health, including validation testing (24-hour, 3-day, and leeching), and rapid clinical testing at Northwell Health and Tampa General Hospital. All testing showed that the 3D printed nasal swabs perform equally to standard swabs used for testing for COVID-19.
After identifying that nasal swabs for testing COVID-19 were in high demand and extremely limited in supply, a team from the USF Health’s 3D Clinical Applications Division created an initial design, working with Northwell Health and collaborating with Formlabs to develop prototypes and secure materials for a 3D printed alternative. Over the span of one week, the teams worked together to develop a nasal swab prototype and test it in the USF Health and Northwell Health labs. In two days, USF Health and Northwell Health, using Formlabs’ 3D printers and biocompatible, autoclavable resins, developed prototypes. The swabs were tested by clinicians at Northwell Health, USF Health and Tampa General Hospital for patient safety and comfort. Now that clinical validation is complete, 3D printers at USF Health and Northwell Health will produce the swabs and provide them to their patients.
“This is a prime example of the incredible impact we can have on human lives when teams of experts across academia, health care delivery, and the tech industry come together,” said Charles J. Lockwood, MD, MHCM, senior vice president for USF Health and dean of the USF Health Morsani College of Medicine. “During this current COVID-19 outbreak, there is little time for delay, and the swift, agile and adept action of everyone on this effort will greatly improve this nation’s ability to test patients.”
“When we were notified of the shortage of swabs by Dr. Lockwood, we immediately began working as a team to create a novel design in a printed material that was proven safe for patients, as is Formlabs’ surgical grade resin,” said Summer Decker, PhD, associate professor in the USF Health Morsani College of Medicine and director for 3D Clinical Applications in USF Health’s Department of Radiology. “We reached out to Northwell Health and Formlabs to work with us on this response initiative. With our collaborators in USF Health Infectious Diseases, we’ve been able to validate the printed swabs utility for this purpose and are extremely optimistic about the pending clinical testing results. With 3D printed swabs, we will be able to add thousands of swabs a day to testing kits developed here at USF Health, and treat more patients safely and effectively. We look forward to continuing to work with Northwell Health and Formlabs to further combat the COVID-19 pandemic.”
“Northwell Health is proud to collaborate with Formlabs and USF to address the global health crisis of COVID-19,” said Todd Goldstein, PhD, Director of Northwell Health 3D Design and Innovation. “When we saw that the testing kits were limited in supply, our 3D printing lab immediately changed focus from creating materials for surgeries to designing and creating materials that help our front line healthcare providers treating COVID-19 patients. In one weekend, we worked together to develop a nasal swab prototype and test it in the lab. After our positive testing results, we then immediately went to work and have already started producing 1,000-1,500 swabs per day. Not only will these swabs be provided to Northwell Health patients, we are also proud to be sharing the design with other institutions that can 3D print so that patients across the country can benefit from our work."
Formlabs’ CEO and co-founder, Max Lobovsky, said: "Formlabs has been working around the clock to provide assistance in the wake of the COVID-19 pandemic, and we’re hopeful that our efforts will help patients get the care they need. It is important that the medical devices we supply to medical professionals on the frontlines battling this disease are safe and work effectively so as not to put workers or their patients at risk. By working hand-in-hand with Northwell Health and USF Health to design and safely produce these swabs, Formlabs is providing a viable solution to the current shortage of nasopharyngeal (NP) swabs and can now produce them at scale to help hospitals better treat patients.”
“During this unprecedented time, Tampa General Hospital is proud to unite with USF Health, Formlabs and Northwell Health to ultimately help save lives. I’ve been humbled and inspired by the perseverance, sacrifice and teamwork of our clinical teams collaborating to create the 3D printed nasal swabs to test patients in need, during emergency shortage situations. Thank you to Formlabs 3D printers for being a true partner to all of our physicians and teams working tirelessly to protect the health and safety of our community and beyond,” said John Couris, president & CEO of Tampa General Hospital.
It is worth noting that the “FDA believes that a nasopharyngeal specimen is the preferred choice for swab-based SARS-CoV-2 testing,” and that “collection should be conducted with a sterile swab.” With years of experience in the medical industry and hundreds of hospitals already using its technology to develop tools for surgery on-premises, Formlabs adheres to a wide range of required sterilization, regulatory, safety, biocompatibility, and manufacturing standards. The company produces sterilizable, surgical-grade plastics for use in medical and dental applications, and its FDA-registered manufacturing site has an ISO 13485 certification. By turning to proven 3D printing technology to improve production processes, shorten supply chains and localize manufacturing, healthcare providers can quickly and efficiently gain better access to the supplies they need to combat COVID-19.
For more of the latest science news, straight to your inbox, become a member of SelectScience for free today>>