LPW Technology Invests in Freeman Technology’s FT4 Powder Rheometer to Optimize Metal Powders for Additive Manufacture
28 Nov 2013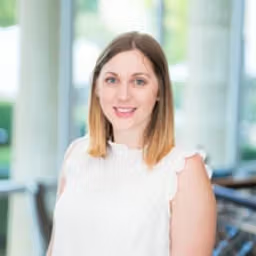
LPW Technology, a leading supplier of optimized metal powders for high end additive manufacturing (AM) applications, is using the FT4 Powder Rheometer® from Freeman Technology to research new powders and exert control over product performance. LPW Technology develops and supplies customized metal powders for high performance, functional component manufacture, supplying, amongst others, the automotive, aerospace and biomedical industries. Comprehensive powder testing using the FT4 Powder Rheometer provides the information needed to engineer powder behavior for specific AM processes and applications and to ensure a consistent quality product.
“Powder testing is a critical part of what we do, both in the development of new powders and as a service for customers looking to optimize existing AM processes,” explains Dr. Robert Deffley, Research and Development Manager at LPW Technology. “We’ve long used traditional testing techniques such as angle of repose, but these have inherent limitations. We have seen examples of two powder batches which meet the same specification showing very different behavior, which made it necessary to look for a new method of characterization with greater sensitivity. We considered shear cell testers, which are good for silo and hopper specification, but this test alone couldn’t accurately measure powder properties under the conditions needed to provide relevant data for additive manufacture. With the FT4 we still have shear cell capability, if we need it, but also bulk property measurement and, most importantly, dynamic characterization capability.”
Additive manufacturing, also known as 3D printing, is a potentially transformative, highly efficient manufacturing technique. It involves ‘printing’, often intricate, components to a tight specification by gradually building up powder layers which are, in the case of metal powders, selectively melted together. Controlling the performance of the powders is crucial for process efficiency and end product quality. How the powder flows and packs, as the layers are formed, are defining aspects of this performance.
“AM is advancing fast and this creates new demands for the powders used,” says Dr Deffley. “AM processes are currently used to produce components with ‘fit and form’, that is prototypes used for advanced product development. The next goal is to robustly engineer in ‘function’ – the controlled porosity for a replacement bone, for example, or complex channels for a more efficient aerospace cooling system. We’re learning that to rigorously cater for these applications we need a more robust understanding of our powders and that these must have tightly controlled, repeatable behavior which is consistent from one batch to the next.”
The dynamic powder characterization capability of the FT4 Powder Rheometer is based on measurement of the powder in motion and directly quantifies how the powder flows. Powders can be tested in a consolidated, conditioned, aerated or even fluidized state to fully understand the response to the process conditions. Complementary bulk and shear property measurements add to dynamic data to fully characterize the powder.
“We started with the measurement of Basic Flowability Energy, a dynamic method,” says Dr. Deffley, “but now we’re measuring everything we can. All of the powder tests offered by the FT4 contribute to our understanding of how our powders behave and support us in delivering exemplary products.”