Meet the graphene pioneer taking the wonder material mainstream
Dr. Marco Caffio reveals how his team took on a seemingly impossible mission – to produce pristine, scalable, and reproducible graphene at a low cost
1 Jun 2021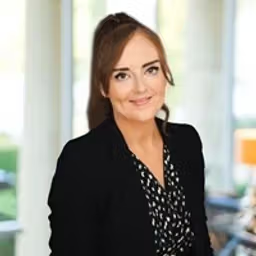
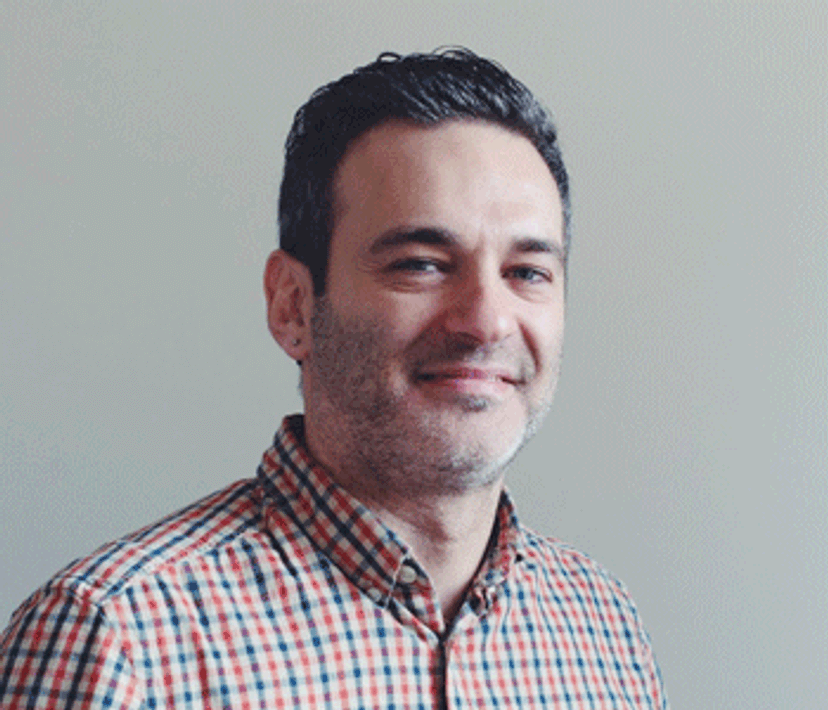
In this exclusive SelectScience interview, we speak with Dr. Marco Caffio, co-founder and chief scientific officer at Integrated Graphene, to find out more about his pioneering work on graphene production and how his expert team has found the winning formula to manufacture pristine, reproducible, and high-quality graphene at a surprisingly low cost. This technological breakthrough could soon make it possible for the thinnest of all known materials to move out of the lab and into the market, changing the way we build biosensors, transistors, energy storage devices, solar cells, and much more — a concept few believed would ever be realized. Caffio also reveals his hopes for the future and explains why Integrated Graphene is a company to watch, as it continues to accelerate graphene into commercialization at long last.
At one time, it seemed almost impossible that at only one atom thick, graphene sheets could be studied in isolation. Graphene was successfully isolated in 2004 by two physicists, known as Geim and Novoselov. In 2010, the two academics were duly awarded the Nobel Prize in Physics. The researchers effectively isolated graphene by repeatedly peeling a graphite sample with adhesive tape until a single, atomic layer of graphene was finally extracted. This pioneering, yet modest method allowed for ballistic transport, as well as the quantum Hall effect (QHE) at room temperature (T) to be experimentally observed. Since then, however, difficulties in producing affordable and scalable graphene that is free from impurities have proved an obstacle preventing this so-called wonder material from entering commercialization.
Now, Caffio believes he and his team have found a solution to this frustrating issue. “We have created a process that really reduces the cost of graphene production. We produce a 3D graphene foam, which is reliable. Our production technique does not require high temperatures or vacuum environments. We have even reduced graphene production from taking ten hours to now only a few seconds,” explains Caffio. The three-dimensional graphene foam Integrated Graphene manufactures is termed Gii. Gii has a sponge-like structure, with a distribution between one, two or three layers of graphene. “Our 3D foam delivers high electrochemical activity, high-specific surface areas, and low levels of contamination,” says Caffio, going on to explain how this 3D foam is ideal for electrochemical applications, including supercapacitors, batteries, and electrochemical biosensors.
Removing impurities
The transfer of graphene to a substrate surface can introduce unwanted impurities, along with polymer residues that reside between the graphene-substrate interface. These impurities have the potential to degrade graphene properties, leading to limiting factors that can contribute to performance degradation, including contact resistance and impedance. To avoid such setbacks, a transfer-free method is desirable, which is often why epitaxial graphene is the chosen method. “We have successfully removed the transfer process; we do not have one,” Caffio says. “We have managed to move away from 2D epitaxial graphene, which is certainly a good R&D tool, but it is not scalable for the commercialization of products.” The expert team at Integrated Graphene deposits 2D graphene directly onto plastic polymers to provide flexibility when designing a device. “We are not limited to a classical, four-millimeter circular working electrode, such as traditional screen-printed electrodes,” says Caffio. “We are now known as an advanced material provider, and we are aiming to tackle every single market. We are focusing on two big markets: energy storage systems and the biomedical sector. We are also collaborating with many universities to explore different applications so we can work in all markets. We are becoming the graphene company that everyone wants to work with, whether they choose to use our materials in their products or simply their R&D activity.”
Apart from unwanted impurities, graphene production is also associated with many other challenges, including a lack of reproducibility from batch to batch and high costs. “We have managed to overcome all of these issues. For instance, the cost of 3D graphene is extremely low, whilst combined with a reproducible process that does not require any additive or binder in the graphene, so users can use purely carbon material,” says Caffio. There is no nitrogen or oxygen originating from binders or additives present in the 3D foam, which is often seen when using screen-printed technology, or even when using chemical vapor deposition (CVD) graphene. CVD graphene is one of the most popular methods used to grow scalable graphene, but its use is traditionally limited by funding restraints, as Caffio points out: “Many choose to use CVD graphene, but are unable to tackle the point-of-care market, because of the high cost associated with it. Our Gii technology means we can tackle the point-of-care market, making use of the intrinsic, extraordinary properties of graphene, without the cost.”
Bridging the gap from the lab to the market
Gii-Sens is an electrochemical platform produced by Integrated Graphene that is often used for R&D activity in industry, research, and universities. “Many are choosing to use our materials for their proof-of-concept work, without the need of dealing with the issues associated with contamination and lack of reproducibility,” says Caffio. “However, we also offer the possibility to move from product design to commercialization.” Integrated Graphene not only offers users its unique Gii technology but can also support the customer through the entire lifecycle of a product, providing the necessary microfluidic systems, expertise and detection systems needed to progress a proof-of-concept device into commercialization. “We can offer the full package,” Caffio continues. “To accelerate medical research, materials must be of a reasonable price, which we offer. In terms of microfluidics, we provide buffer pouches, mixing units, blood filtrations, onboard pumps, you name it. We have a team of scientists and engineers that work on all of the different aspects of production and can assist our customers, from microfluidics to graphene functionalization and development of the chemistry, and also an expert team that takes care of the instrument itself.” Caffio believes that Integrated Graphene is the only company that can resolve every single issue that the graphene production industry is facing, “We offer a low-cost, reproducible, high-performing graphene, without contamination. We also have the ability to grow our graphene on any substrate. As far as I know, there is not another graphene company that can do that.”
Looking ahead, Caffio is fully focused on continuing his ambitious plan to develop the Gii technology and tackle an array of different markets. “The final goal is to integrate the Gii technology onto a single platform, which can be used from the medical industry to the energy sector to the environmental sector,” says Caffio. He concludes by sharing his vision of Integrated Graphene’s pioneering work paving the way for innovation, finally allowing this extraordinary material to transform healthcare and revolutionize materials science with its combination of flexibility, transparency, durability, strength, and conductivity.