Tackling a problem from the monomers up: How can we create plastics from renewable sources?
We speak with Niklas Warlin to learn about his research into plastics made from renewable sources and how researchers are developing the monomers to build these
7 Jun 2022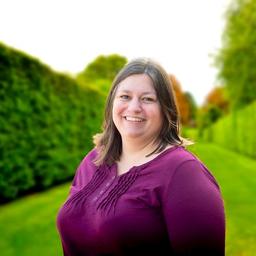
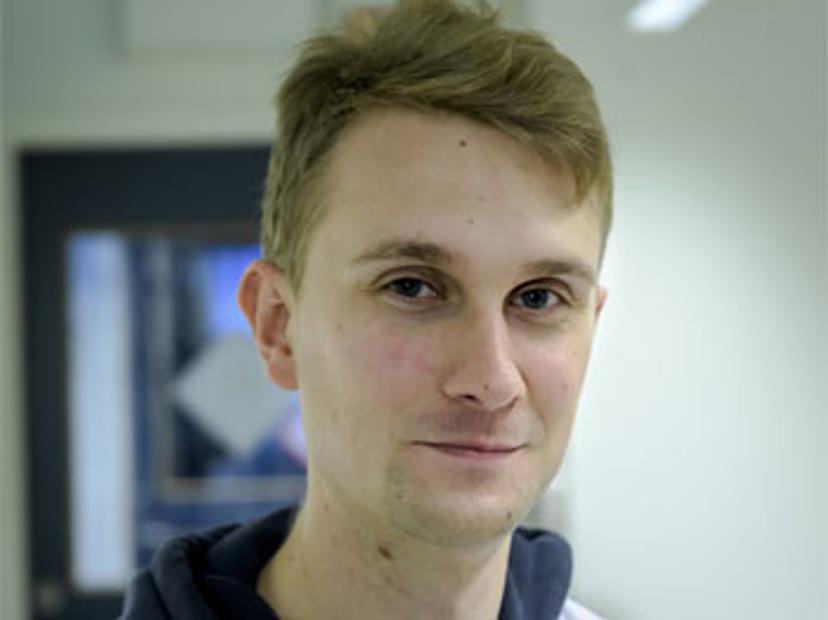
Niklas Warlins, Ph.D. candidate at Lund University
Despite their ubiquity in the modern world and value as extremely useful materials, plastics also come with a cost – they are currently manufactured using fossil fuels, and recycling can be difficult, leading to further pollution. In order to maintain our use of plastics while reducing their environmental impact, scientists and researchers are working together to develop new kinds of plastics from renewable sources, improving their recycling potential and creating new properties.
One researcher who is working in this area is Niklas Warlin, a Ph.D. candidate at Lund University. In this interview, he discusses the challenges with the development of plastics from renewable sources and tells us about his work developing monomers and polymers as a building block for these new plastics.
Searching for a renewable source
While incredibly useful, and essential in various settings, plastics can also cause vast amounts of pollution – from their manufacture using fossil fuels to their disposal, with evidence of plastics in oceans, the food chain, and throughout landfills. The challenge for researchers and manufacturers is to develop plastics with the same useful properties as those currently in use, without this environmental impact, by making them from renewable sources instead.1
“By using bio-based sources to design new molecules with unique and superior properties to current fossil-based ones, we aim to design plastics with decreased carbon footprint and improved material properties to facilitate commercialization,” Warlin explains, and this work starts with the development of monomers derived from renewable sources.
“In my research, I try to replace common fossil-based monomers by using starting materials derived from the sugar or forestry industry. More specifically, I have been working a lot with a molecule called 5-hydroxymethylfurfural (HMF), which is widely recognized as one of the most important platform molecules needed for transitioning to a bio-based chemical industry,2” explains Warlin. “HMF can be synthesized from sugars (more specifically hexose carbohydrates) and there is a lot of research investigating how to produce these molecules from food waste.”3
We aim to design plastics with decreased carbon footprint and improved material properties to facilitate commercialization.
Niklas Warlin Lund University
Manufacture isn’t the only part of the plastic lifecycle that is harmful to the environment. Researchers also need to consider how the material breaks down after use, or if it can be easily recycled for re-use. “By taking the end-of-life aspect of the material into consideration when designing the monomers, we also hope to enable chemical recycling for polymers that currently cannot be recycled by conventional means,” shares Warlin.
Testing for the right properties with the right equipment
When creating new monomers and polymers, researchers assess them for the right properties before being further developed. This often means working with incredibly small amounts of molecules, which has its own difficulties. “When designing new bio-polymers it is crucial to ensure they meet the high requirements necessary to be potentially processed into a useful product,” explains Warlin. “This task is often difficult when working with new monomers since we often have a quite limited supply of these – I often synthesize polymers in relatively small scale (< 1 g).”
For delicate work with precious samples, it’s important to have the right equipment in place. In his research, Warlin uses the Malvern Panalytical OMNISEC GP/SEC system. “The user interface is intuitive and easy to learn. The system is reliable and gives accurate results quickly,” attests Warlin. “Another major benefit compared to other size exclusion chromatography (SEC) systems I have used is that this one has very easy access to the columns and the pump which makes routine maintenance easy (e.g. changing columns, replacing pump filters, purging etc.). It also has several vapor detectors in the different compartments of the machine, which is useful for detecting leaks.”
Warlin’s research aims to change the way that we not only produce plastic, but also expand and improve the useful properties that these plastics can exhibit. This analysis requires the ability to accurately measure the polymers’ molecular weights, which is especially difficult when they only exist in very small quantities. “It is necessary to be able to determine the molecular weight in an easy and reliable way, without using up too much polymer,” shares Warlin. “This is exactly what we use the OMNISEC system for.”
Molecular weights are a crucial piece of information when assessing the potential for the created polymer to be developed into a sustainable, useful plastic. “The most fundamental property of a polymer is its molecular weight, and in general, the physical properties of a polymer improve with higher molecular weight. As a rule of thumb, a polymer needs to have a molecular weight of at least 15,000 g/mol to be considered useful for any application,” Warlin explains. “By determining the molecular weight of a polymer, we can quickly predict whether our new polymerization has been successful and we have obtained a promising polymer that is worth analyzing further, or if we have to start over and try to optimize the polymerization conditions before doing further analysis.”
This is where the OMNISEC really works for Warlin: “We use it for a wide range of polymers, and still get reliable results.” By being able to reliably test a wide range of polymers, even with only small amounts produced, researchers like Warlin are leading the way in the search for renewable plastics.
References
J. Zheng & S. Suh. Strategies to reduce the global carbon footprint of plastics. Nature Climate Change 9, 374-378 (2019). https://doi.org/10.1038/s41558-019-0459-z
J.J Bozell & G.R Petersen. Technology development for the production of biobased products from biorefinery carbohydrates—the US Department of Energy’s “Top 10” revisited. Green Chem, 12, 539-554 (2010). https://doi.org/10.1039/B922014C
M. Sayed, N. Warlin, C. Hulteberg et al. 5-Hydroxymethylfurfural from fructose: an efficient continuous process in a water-dimethyl carbonate biphasic system with high yield product recovery. Green Chem, 22, 5402-5413 (2020). https://doi.org/10.1039/D0GC01422B