Unlocking the secrets to faster analytical methods in food quality and safety testing
Principal scientist Jane Guido discusses key issues facing the food industry, the innovative technologies helping to accelerate analytical workflows and her predictions for the future
15 Sept 2019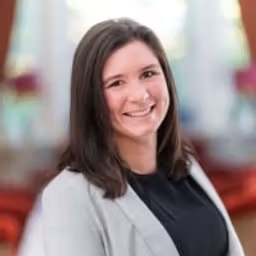
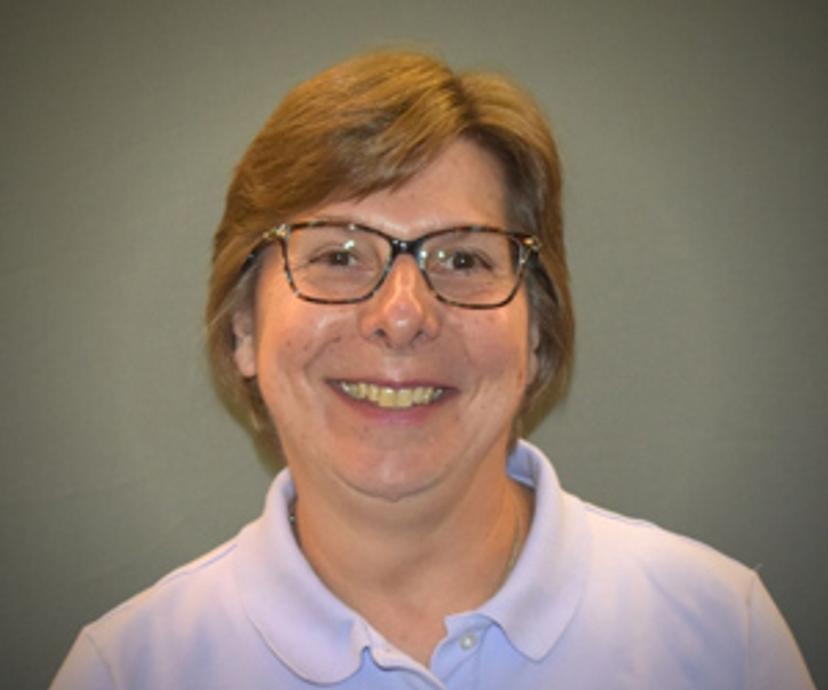
With the food industry under constant pressure to streamline quality and safety testing, one US-based company, Kalsec®, Inc., has hit on a winning formula as it works to accelerate quality control (QC) processes. In this exclusive SelectScience® interview, experienced analytical scientist Jane Guido shares insights into the challenges facing her lab and the novel technological solutions making all the difference by “unlocking the use of mass spectral detection to all of our scientists, even if they have never touched a mass spectrometer before.”
SS: Please introduce yourself and place of work
JG: My name is Jane Guido, I am a Principal Scientist in Analytical R&D at Kalsec, Inc. I have over 33 years of industrial experience, with the first 20 years in the pharmaceutical industry and the remainder at Kalsec® in the food ingredients industry.
Kalsec captures the best nature has to offer by providing innovative spice and herb flavor extracts, colors, antioxidants, and advanced hop products. Our products are translated into easy-to-use liquid extracts ideal for most formulations. Trusted since 1958, Kalsec is committed to providing value to the food and beverage industries for the next 100 years. Headquartered in Kalamazoo, MI USA, Kalsec has facilities in North America, Europe, and Asia.
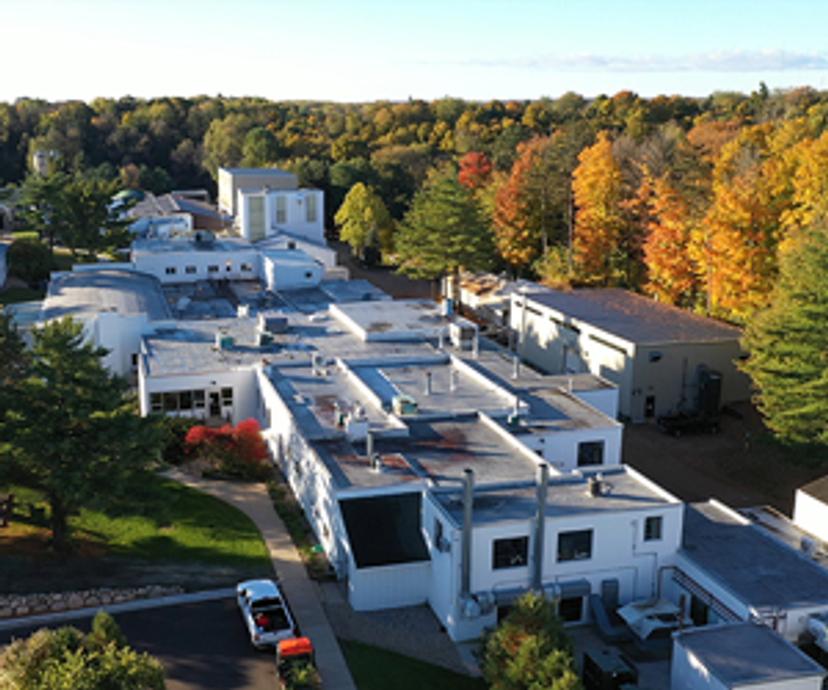
SS: What are the key goals of your lab?
JG: Analytical R&D is responsible for developing and validating methods for quality control, assisting QC in maintaining methods, supporting QC with method and instrument issues/failures, and running QC methods for which QC staff does not possess the expertise or instrumentation. In addition, we provide support to product R&D, sales, manufacturing, and we are an integral piece of the puzzle for solving customer challenges and addressing industry concerns. Our primary goal is to provide analytical support to all areas of the company in a timely fashion using innovative analytical technology.
SS: Are there any key molecules you detect in your food samples to ensure quality?
JG: The list is far too long to enumerate! We analyze for known active ingredients in all of our raw materials and finished products and we subject our raw materials to extensive analytical analysis to assure the absence of contaminants that would affect the quality and safety of our products.
SS: What are the key challenges you face?
JG: There is always the need for more specific, faster analytical methods with lower LOD/LOQ in our very complex matrices. We are always searching for new sample preparation techniques to decrease the amount of matrix left in our sample preparations in order to minimize matrix effects in mass spectral methods and to keep instruments cleaner for longer periods of time thus decreasing downtime.
SS: How are UPLC and ACQUITY QDa technologies helping you meet your laboratory operational goals and outcomes?
JG: We have found that the ease of use of the ACQUITY QDa technology has made it very straightforward to develop methods for use in the QC environment. We currently have two UPLC/QDa methods implemented into QC for two of our high-volume product lines and a third method is being implemented as we speak; it will support one of our highest volume and most valuable product lines. This product line contains a large number of active components, many of which overlap in retention time; this makes the ACQUITY QDa Detector an invaluable addition to the analytical methodology. The decrease in run time and increase in confidence of peak identification, combined with the ease of use of the instrument, are the key selling points for this technology in the QC environment.
In the Analytical R&D environment, the accessibility of the ACQUITY QDa unlocks the use of mass spectral detection to all of our scientists even if they have never touched a mass spectrometer before. The fact that it runs on Empower software is a definite advantage since all of the other LC systems in our laboratory also utilize Empower software; training is thus simplified.
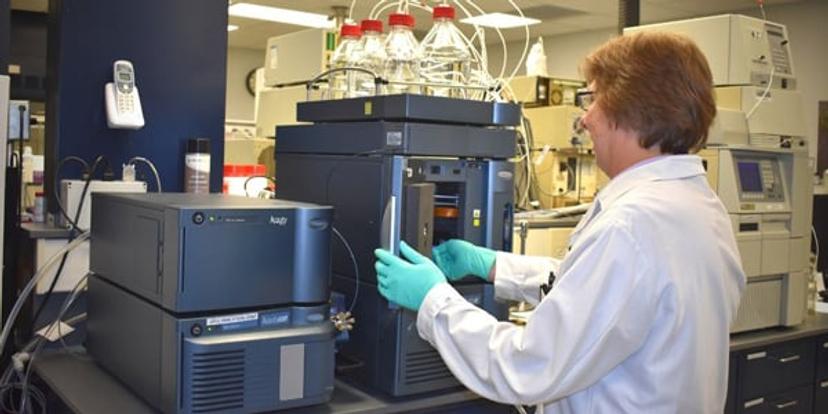
SS: Which systems do you use?
JG: In Analytical R&D, we use Waters HPLC and UPLC systems with PDA detection and UPLC/MS systems with QDa, TQD, and QTof mass spectrometers for all of our research work and contaminant analysis. The use of all Waters systems helps us save money on service plans and software training (Empower for the HPLC/UPLC PDA and QDa systems and MassLynx for the TQD and QTof systems).
SS: What do you see for the future of food quality control both in terms of technology and changes in QC?
JG: I expect to see an increased use of UPLC technology to increase the QC laboratory throughput and decrease the time that production waits for analytical results of in-process samples. Mass spectral detection will become more common as the need for the analysis of complex matrices containing a variety of active components continues to increase. This rise in the use of mass spectral detection will also necessitate increased computing power and data storage.
Do you use Waters products in your lab? Write a review today for your chance to win a $400 Amazon gift card>>