Validair launches new gassing decontamination solution
29 Jan 2021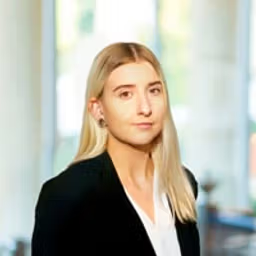
Validair Monitoring Solutions Ltd (VMSL) has announced the launch of a new gassing solution for cleanroom facilities to enable safe, rapid and effective decontamination.
The launch is the result of a successful in-house development project that brings together high-end valve hardware, cleanroom applications expertise, installation and commissioning services, and support as a complete packaged customer solution.
The new VMSL isolating gassing solution comprises high-specification three-way diverter valve hardware packaged with Validair’s contamination control expertise. The company expects the solution to appeal to the constructors and owners of the increasing number of smaller, more cost-effective cleanrooms and isolators being built across the pharma manufacturing sector.
A key customer benefit to the comprehensive new package is the Validair expertise included with the superior valve hardware. As particle counting and contamination control experts, the company is best placed to deliver the applications knowledge and support services needed to guarantee the optimum set up for rapid Hydrogen Peroxide Vapor (HPV) gassing decontamination.
The hardware element of the gassing solution is a superior, industrial-grade valve assembly that meets Validair’s exacting requirements. “Scrutinizing and thoroughly specifying the quality and functionality of the value solution was critical,” explains Technical Lead Steve Moss, who headed up the Gassing Valve development project. “We evaluated many products before settling on a high specification diverter valve mechanism that features Teflon coating for all wetted interior surfaces to prevent the shedding of any particles and a robust, chemically-inert stainless-steel construction.”
The three-way diverter valve protects an attached airborne particle counter (APC) from contamination, degradation and damage. In its working position, the valve allows the air within the cleanroom or isolator chamber to be continuously monitored by the APC, validating the contamination integrity of that sensitive environment. In the safe position, which can be an automatic switchover process controlled by a Facility Monitoring System during a clean & purge cycle, the valve opens a channel to the cleaning agent while completely shielding the sensitive optics and components of the airborne particle counter. The internals of an APC can be irreparably damaged by exposure to the cleaning agent, typically hydrogen peroxide vapour (HPV).
An electrical switch is activated when the valve has moved to its safe position. As well as a practical failsafe, this can provide feedback to a Facility Monitoring System, such as TSI’s FMS 5, to automate the gassing process. Actuation of the diverter valve can be electric or pneumatic.
Want the latest science news straight to your inbox? Become a SelectScience member for free today>>