Webinar Highlights: Integrated Data Management at Shell Martinez Refinery
Read the highlights and Q&A from part two of the webinar series: Innovations in Laboratory Efficiency and Analytical Workflows
29 May 2020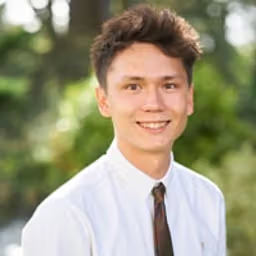
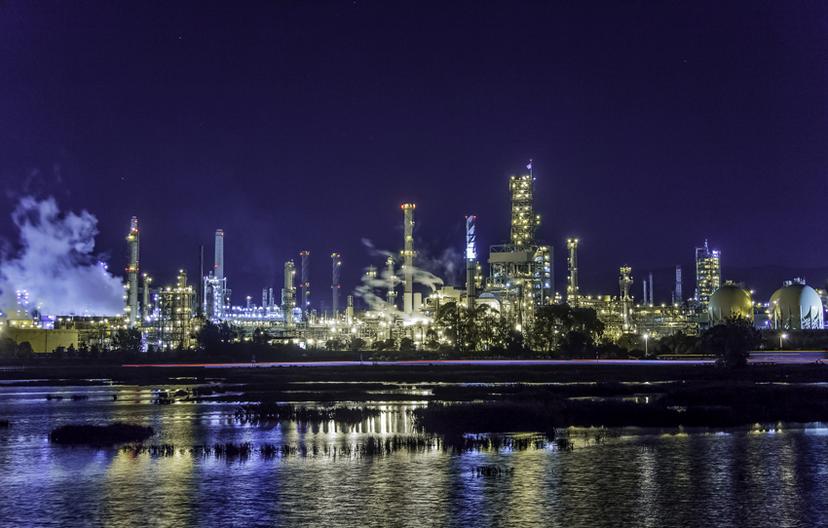
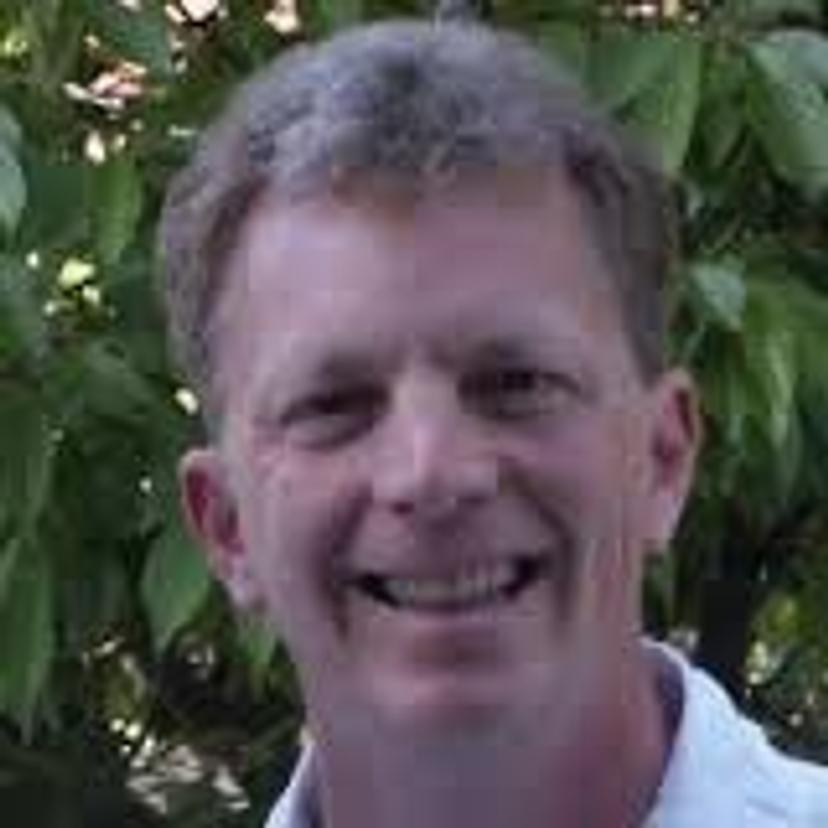
In this webinar, Steve Best, from Thermo Fisher Scientific, and Robert Carroll, Manager of Control Systems Engineering at Shell Martinez Refinery, discuss a new informatics solution to integrate on-line spectroscopy with lab data, producing a database for spectral analysis and large-scale model building.
Steve Best, Senior Sales Representative for North America, Informatics & Chromatography Software at Thermo Fisher Scientific, has over 34 years’ experience in the chromatography industry. Along the way, he has gotten to know the many difficulties faced by manufacturing plants in managing all of their data and so, to begin with, he underlines the importance of effective management of your data. He explains how integrated informatics solutions provide a link between a company’s manufacturing environment, the laboratory that supports it, and the quality of products tested in the lab. Used for virtually all large-scale spectrographic projects, the ultimate goal is to improve efficiency, which leads to increased revenue and reduced costs. Steve highlights how a key benefit of this technology is the ability to create models, enabling the creation of a real-time production environment. He adds that models can be extremely complicated, involving vast amounts of data, all of which needs to be catalogued, and so the use of an integration system is very important. One such system available is the Thermo Scientific™ GRAMS Suite 9.0, which, he explains, enables you to move on from outdated worksheets so as to boost the speed and efficiency of your processes, whilst providing a platform for continuous improvement.
Integrating informatics at the Shell Martinez Refinery
A working example is provided by Robert Carrol, Manager of Control Systems Engineering at Shell Martinez Refinery, who describes how his facility replaced its old online managers to integrate his online spectroscopy with laboratory data. The integration was so successful on the test scale that they ended up expanding the update to the whole refinery.
Robert recalls how, prior to the integration, he was using a lot of spreadsheets, requiring a lot of manual input. Model building was being outsourced and the monitoring of them was slow, causing a loss of productivity and quality overall. The GRAMS Software was built upon his current LIMS, making it very simple to upgrade, he explains. With the software in place, he is able to automatically link up the data being collected from Raman analyzers throughout the refinery, correlating it directly with his samples. The advantages don’t end here though and he adds that he is also able to monitor his processes easily with the software, to see if they are behaving as expected, producing models to observe trends when needed.
Since the introduction of the software, Robert comments that the transition has been highly successful at Shell Martinez. He highlights that the team can now successfully manage 40-plus online spectrographic streams with over 400 models and that the system is expected to scale over 1000 models in the future. Data is now easily accessible to technical lab and maintenance personnel to independently monitor as needed and, as a direct result of the upgrade, the organization is bringing in more staff to analyze the increasing amount of data being produced, which is a big boost to the plant’s productivity.
Read on for highlights from the Q&A session or watch the webinar on demand here.
What quality goals are addressed by the Thermo Scientific GRAMS Suite 9.0?
RC: This system is designed to give real-time data for analyzers. We couldn’t afford to have an individual system for each property, so we’re going to scale these models bigger than is possible for individual online analyzers alone.
How does this system improve efficiency and reduce man-power?
RC: Without this software, we were looking at having to hire two to three people just to manage all the software. With the 100 models, we thought we would need at least one more person just to get to the same level of response, and in fact we haven’t hired anyone. We’re very happy with the efficiency of this system.
What is the future for this system?
RC: We’re going to keep pushing larger and larger. Another thing we’re doing is mining the data that is in the system deeper, so we can tell when the lab measurements are good or bad and interact with the data.
We’re creating new models all the time on streams we didn’t think we needed additional properties on. When we discover we do need additional properties it’s quick to bring the next model online.
Who would be able to use this technology?
RC: I’m with Process Control and this software was new to us. The uninitiated will be able to get up-to-speed pretty quickly.
Which industries are using this type of system?
SB: We have numerous customers across several aspects of the oil and gas business, and also in the chemical industry, where these model building efforts have yielded quite exemplary results and where the tools that they deploy at the plant are becoming more and more complex. This has forged the opportunity to build these more complicated models, increasing the number of properties that those models manage. That has a lot of downstream effect and goes across a lot of our industry.