Dealing with unpredictability: Manufacturing COVID-19 lateral flow tests during the pandemic
An insider’s look into the bottlenecks and challenges associated with manufacturing and supply chain workflows within lateral flow diagnostics
17 Dec 2020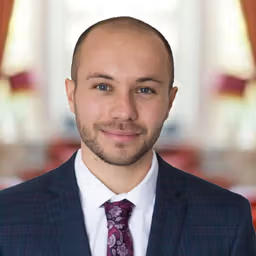
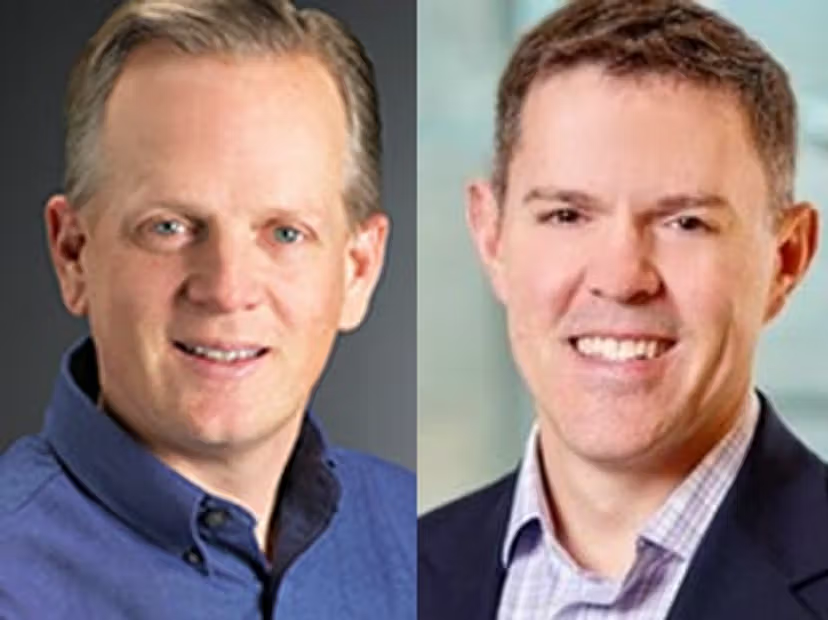
Dr. Michael Mansfield, Applications Development Scientist, and Shawn Gaskell, Head of Diagnostic Manufacturing Materials, MilliporeSigma
The COVID-19 pandemic is notoriously different from previous pandemics such as H1N1 or MERS in terms of the magnitude of its impact on global health. It has not only tested the very core of health systems worldwide, but also the resilience of multiple industries. Access to raw materials globally has been a major challenge, one that is also seen in the field of diagnostics. Being both flexible and pragmatic are proving critical while manufacturing, supply chain and logistics systems are compelled to adapt.
In this SelectScience interview, Shawn Gaskell, Head of Diagnostic Manufacturing Materials, and Dr. Michael Mansfield, Applications Development Scientist, MilliporeSigma, expand on how the global pandemic has created a substantial demand for rapid diagnostic assays, while simultaneously posing serious capacity and production challenges in manufacturing these tests. Together, they describe the applications and advantages of lateral flow testing, provide an insider’s look into the current manufacturing bottlenecks and outline plans for the future expansion of MilliporeSigma’s diagnostic capabilities.
Rapid, effective and inexpensive testing
An example of how a pre-existing solution has been aptly adapted for the present situation is that of lateral flow testing. “This is a widely-used, easily understood, time-saving technology that has been around for over 40 years now,” says Gaskell. “A common application of this is the pregnancy test kit. People are very familiar on how to administer them and are well aware of the quick turnaround of the results within three to five minutes.” So, when these tests were adapted to provide rapid, portable solutions to testing for COVID-19, the response was positive. “The application is certainly well suited for COVID-19 diagnostics, giving almost instantaneous results while waiting at the doctor's office or an emergency room or a drive-thru parking lot, instead of waiting three or four days as required for some of the molecular testing approaches.”
Expanding on specific advantages that lateral flow testing offers, Gaskell adds: “You can even test for multiple pathogens in the sample via multiplex testing. This helps to distinguish whether the patient has influenza, COVID-19 or some other disease like dengue or malaria, all in one test within the span of a maximum of 15 minutes.” The tests may not be quite as sensitive as PCR tests, but the dual strength of their rapidity and portability helps to quickly develop a plan of action. This can be hugely advantageous, especially in COVID-19 positive cases where an immediate quarantine may be vital. Looking beyond determining infectivity, Mansfield adds: “Where I see lateral flow tests having a lot of utility is when large-scale vaccinations begin. These tests will help to confirm whether the vaccine has taken hold by determining the presence of circulating antibodies for the virus in the bloodstream.” For either application, “the cost is still the biggest driving factor,” asserts Gaskell. “Major diagnostic manufacturers are releasing coronavirus rapid lateral flow tests as an effective way to manage this crisis at a very inexpensive price of $5 to $10.”
Manufacturing during a pandemic
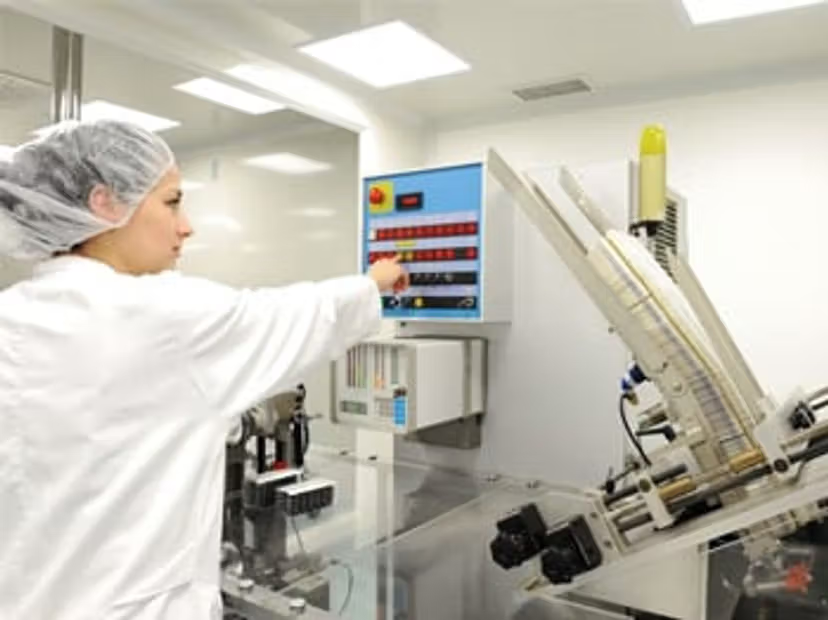
Manufacturing must continue during the pandemic © J. Merdan @123rf.com
The advantages these tests offer make them popular, and with the surging demand come the manufacturing and supply chain challenges. The performance of each of these test kits is driven by the components involved – from the core membranes themselves, to the many ancillary reagents such as antibodies, surfactants, detergents, buffers, detector particles and more. “All of these raw materials are sourced in very different ways,” explains Gaskell. Increasing biological capacities can take years as a result of important regulations and the inherent challenges associated with the process. Differences in the procurement and usage of raw materials between test development and manufacturing pose additional challenges, as Mansfield explains: “A major question is whether the state of materials used during the R&D stage is representative of the level of variation that could be expected in the large-scale utilization of the materials on a manufacturing line.” And this difference is exacerbated in the current climate: “Right now what’s going into manufacturing is being cycled into finished tests within weeks of receipt, whereas pre-COVID-19, materials could sit around for two to three months before being allocated to a final test.”
Prior to the pandemic, market success and additional demand for lateral flow products had already prompted MilliporeSigma to start expanding capacity. While aiming to ramp up membrane production by 2021, COVID-19 has presented new challenges when looking to bring these plans to life. Since the pieces of equipment are designed and built in various geographies around the globe, Gaskell elaborates that the acceleration of production had to be adjusted for construction restrictions and social distancing-mandated limitations in workspaces. Travel restrictions and quarantine rules also resulted in knowledge transfer delays, for example from experts in MilliporeSigma’s membrane center of excellence in Ireland to vendor facilities worldwide.
Key to addressing such unpredictable challenges, notes Gaskell, is building flexibility into the process rather than simply buying additional equipment or making capital expenditures. Manufacturers have to make a continuous effort to assess their theoretical and actual capacity versus utilization rates, which is in turn driven by market needs. Being pragmatic is also crucial because “you could build a second machine or increase biological capacity to be ready for an event 20 years from now, but the technology changes so quickly that you won't be able to use half of these materials then,” he adds.
Thinking ahead
Focusing on customer needs, with an adaptable approach, MilliporeSigma offers a wide variety of products that are unique to the life science marketplace. Its facilities in the U.S., the U.K. and Ireland offer custom antibody development services. Other offerings include cell lines and cell line development, cell banking, kit assembly, and unique OEM contract manufacturing and diagnostic solutions for customers who face capacity challenges but lack production capabilities.
Currently, MilliporeSigma teams support all aspects of the lateral flow workflow except for the finished device manufacturing. “Along with adapting supply chain and development capabilities, we continually explore opportunities aimed at expanding our services business to support the changing needs of the IVD industry”, explains Gaskell. “Down the road, we would aim to manufacture lateral flow devices or custom-made kits for our customers. As companies scale and grow their own diagnostic capabilities and look for help in doing that, we see ourselves as a very critical partner.”
For more information on COVID-19 and the design, application, and manufacturing of lateral flow tests, see the related article: COVID-19 testing using lateral flow assays: sensitive, rapid, easy to use and point-of-care
Request a free sample pack to see how Hi-Flow™ Plus membranes can enhance your tests.