Freeze drying and sublimation: The importance of precise vacuum technology
Watch this on-demand webinar to learn more about the principles of sublimation and freeze drying, and hear top tips on selecting the best vacuum technology
31 Jan 2022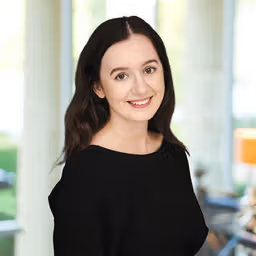
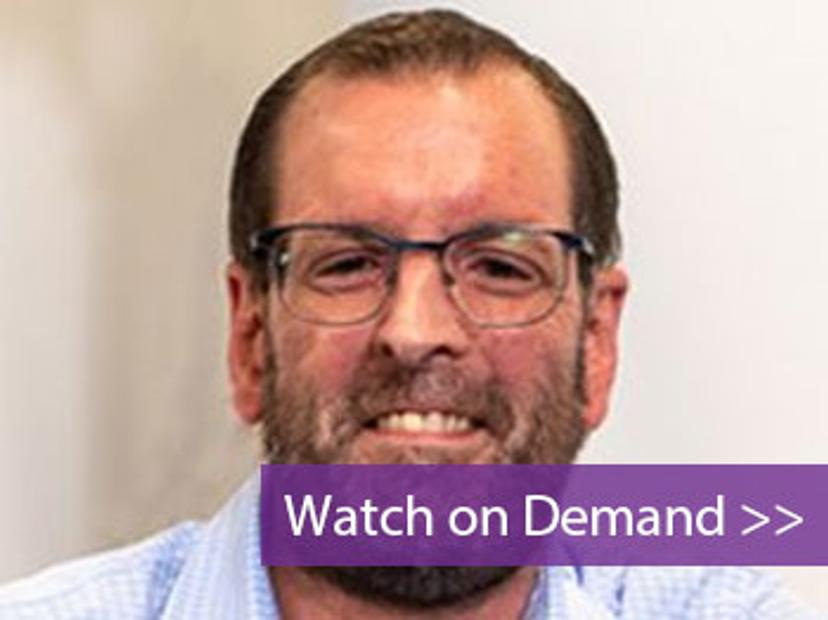
The goal of freeze drying is to dry samples as gently as possible. The physical principle of sublimation is used to let ice turn directly into a gaseous state without melting water forming. Vacuum plays a key role here, as sublimation is only possible under exact pressure conditions.
In this on-demand SelectScience® webinar, VACUUBRAND expert Carsten Ruth explains why precise vacuum is crucial in this application and why too low pressure is counterproductive. He will also share valuable advice on how to not only achieve optimum results and process times, but also how to effectively protect your vacuum pump from wear.
Watch on demandRead on for the live Q&A session or register to watch the webinar at a time that suits you.
What are the advantages of choosing a vacuum pump like the VACUU·PURE compared to rotary vane pumps for freeze drying?
CR: The VACUU·PURE is revolutionary technology for the field of freeze drying because it introduces a tremendous level of process and user safety that is not possible to achieve with an oil-driven or oil-sealed system. The freeze-drying process itself works completely fine with a common oil pump or the two-stage rotary vane pump, as long as you take good care of your pump and keep it in good condition.
An oil-driven pump always bears the risk of failure whenever it accidentally catches moisture or chemicals. Whereas the VACUU·PURE is a dry technology with reasonable chemical resistance, which simply eliminates these risk factors. It is not sensitive to accidental moisture or even slide chemical loads, and it is a dry, maintenance-free system. You have much more flexibility and you eliminate all the worries on the pump side. That's the benefit of the VACUU·PURE technology
Can you apply these vacuum pumps to a regular LC-MS system?
CR: LC-MS systems are a clear option for the use of the VACUU·PURE technology by means of being used as a backing pump to the integrated high vacuum pump in the MS system.
What is the lowest vacuum achievable with the VACUU·PURE?
CR: The VACUU·PURE is in the performance range of a two-stage rotary vane pump. The specified ultimate vacuum of VACUU·PURE is 5 x 10-3 millibar.
Can a VACUU·PURE vacuum pump replace an existing pump within a freeze-drying system?
CR: The VACUU·PURE does the same job that is done by the initial pump. The replacement option itself depends on the specific layout of the freeze-drying system. If you have a system where the pump is external it's as easy as just swapping the pump. For systems with integrated pumps, we may have to look a bit deeper, as different pumps have different dimensions and the direction of the connectors might be different. In general, it is possible to update your existing freeze dryer with a VACUU·PURE pump.
What is the ideal vacuum for the lyophilization process?
CR: The ideal vacuum condition for freeze-drying process depends on your drying media. For example, if you're drying an aqueous sample and you have a sample temperature at pre-frozen stage in the range of -20°C, you will have a resulting vapor pressure of 1 millibar. This is the minimum vacuum you need to achieve to realize the sublimation process. But certainly, you need to build in some additional tolerance.
As a general guideline, you can estimate the sublimation pressure of your sample at your process and temperature condition. From there, you reduce by 50% and this should be your optimal process vacuum. In our example, if our resulting sublimation pressure was 1 millibar, we would run our process at 0.5. For every mixture you may be working with, you can make this simple estimation of the optimal process condition.
Is it possible to apply freeze drying to dairy products?
CR: It certainly is, and freeze drying is commonly applied in the dairy industry. It may not be applicable for each type of dairy product, but freeze drying is a common procedure in the dairy industry to achieve milk powder, for example. It does not mean every milk powder comes from freeze drying, but freeze drying is an established process in this industry.
Do you have any specific recommendations for acquiesce protein samples?
CR: The important point in freeze drying is to achieve the equilibrium stage between sublimation and resublimation. If you work with protein samples, you have to pay specific attention as protein samples are very sensitive to intermediate melting. If there's a slight liquid building up, it will destroy your entire sample.
Here, it is advisable to move lower in the pre-freezing process to build in some additional safety tolerance during the pre-freezing. Specifically, if you have to carry your sample from the deep freezer to the freeze dryer, then focus attention on very precise process guidance. For protein samples, I would even advise to use a programmable vacuum control. If your freeze-drying system does not have this, this can be updated externally on the pump side in order to pre-program your process and to have a precise process guidance on the vacuum side.
Do you believe lyophilization can be successfully applied to lipid nanoparticles, such as existing vaccines containing fragile mRNA, in lieu of conventional freezing?
CR: Yes, absolutely. Freeze drying is by far the most gentle drying method for removal of solvents or liquids. In the area of vaccines, freeze drying is a commonly applied process for preserving the vaccines over time as they are very difficult to store and transport in their initial stage. The freeze-dried vaccine is much less sensitive than the active vaccine and therefore much easier for storage and transportation.
Activated vaccines, in many cases, have to be stored at ultra-low temperatures. While after freeze drying, they can be stored in normal cooling temperatures, which is a big benefit for logistics. It makes them stable over the long term, so their expiry dates are by far extended. Whenever they are needed, they can be rehydrated and reactivated for instant use. In this area, freeze drying is a very good option.
SelectScience runs 10+ webinars each month, discover more of our upcoming webinars>>